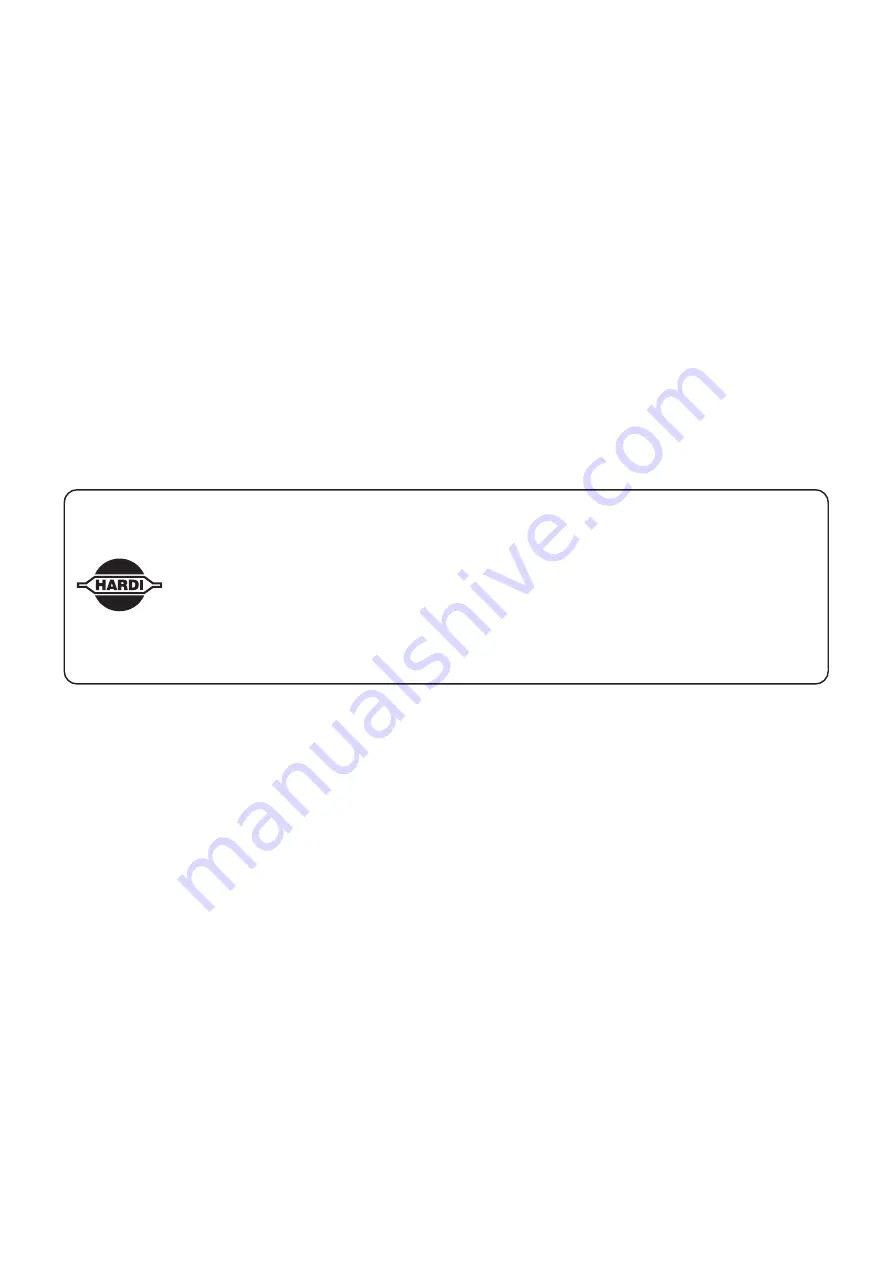
1
GB 01 00 MA
MASTER
VHY/HVZ
Instruction book
679025-GB-2003/12
We congratulate you for choosing a HARDI plant protection product. The reliability and
efficiency of this product depend upon your care. The first step is to carefully read and
pay attention to this instruction book. It contains essential information for the efficient
use and long life of this quality product.
As this instruction book covers all MASTER models with VHY or VHZ boom, and all
models with either BK or EVC operating unit, please pay attention to the paragraphs
dealing with precisely your model.
This book is to be read in conjunction with the “Spray Technique” book.
Illustrations, technical information and data in this book are to the best of our belief correct at the time of printing. As
it is HARDI INTERNATIONAL A/S policy permanently to improve our products, we reserve the right to make
changes in design, features, accessories, specifications and maintenance instructions at any time and without
notice.
HARDI INTERNATIONAL A/S is without any obligation in relation to implements purchased before or after such
changes.
HARDI INTERNATIONAL A/S cannot undertake any responsibility for possible omissions or inaccuracies in this
publication, although everything possible has been done to make it complete and correct.
As this instruction book covers more models and features or equipment, which are available in certain countries
only, please pay attention to paragraphs dealing with precisely your model.
Published and printed by HARDI INTERNATIONAL A/S
Summary of Contents for MASTER VHY Series
Page 2: ...2...