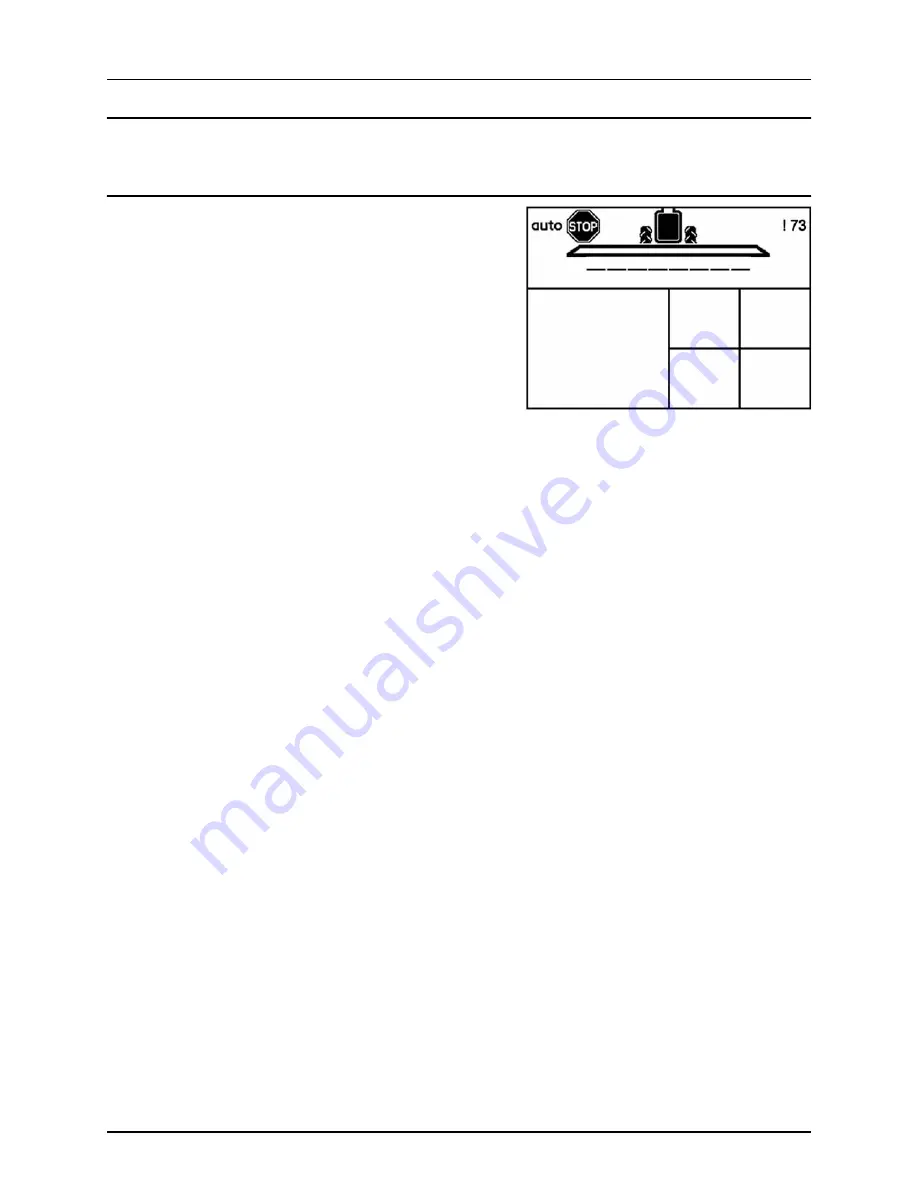
6.1
6 - Menu 2 Setup
Menu 2.1 Display readout
General info
The following menu explanations assume you have mastered the general keystrokes and you can “find your way” to the
specific menu. If this is not so, please re-read section “Keys”.
Menu 2.1.1 Display readout
It is possible to choose which functions are shown in the 4 different
boxes (A, B, C and D) of the display.
1.
Go to menu [2.1 Display readout].
2.
Use ¿ or ª to choose which of following boxes you want the
data shown in and press # to confirm.
2.1.1 Show upper middle (A)
2.1.2 Show upper right (B)
2.1.3 Show lower middle (C)
2.1.4 Show lower right (D)
3.
Choose a submenu e.g. menu [2.1.1.04 Work rate]. Press # to
confirm.
4.
Press ~ to leave menu.
See next page for a complete list of possible display readouts.
A
B
C
D
Summary of Contents for HC 6500
Page 1: ...CONTROLLER HC6500 Instruction book sw 1 2x 67021903 Version 1 20 US 08 2010 ...
Page 2: ......
Page 4: ......
Page 10: ...1 Welcome 1 2 ...
Page 30: ...4 System setup 4 8 ...
Page 62: ...8 Menu 4 Toolbox 8 4 Menu 4 4 Reserved Reserved function This menu is not used ...
Page 70: ...10 Soft keys 10 2 ...
Page 72: ...11 Maintenance 11 2 ...
Page 80: ...12 Fault finding 12 8 ...
Page 89: ...Notes ...
Page 90: ...Notes ...
Page 91: ......