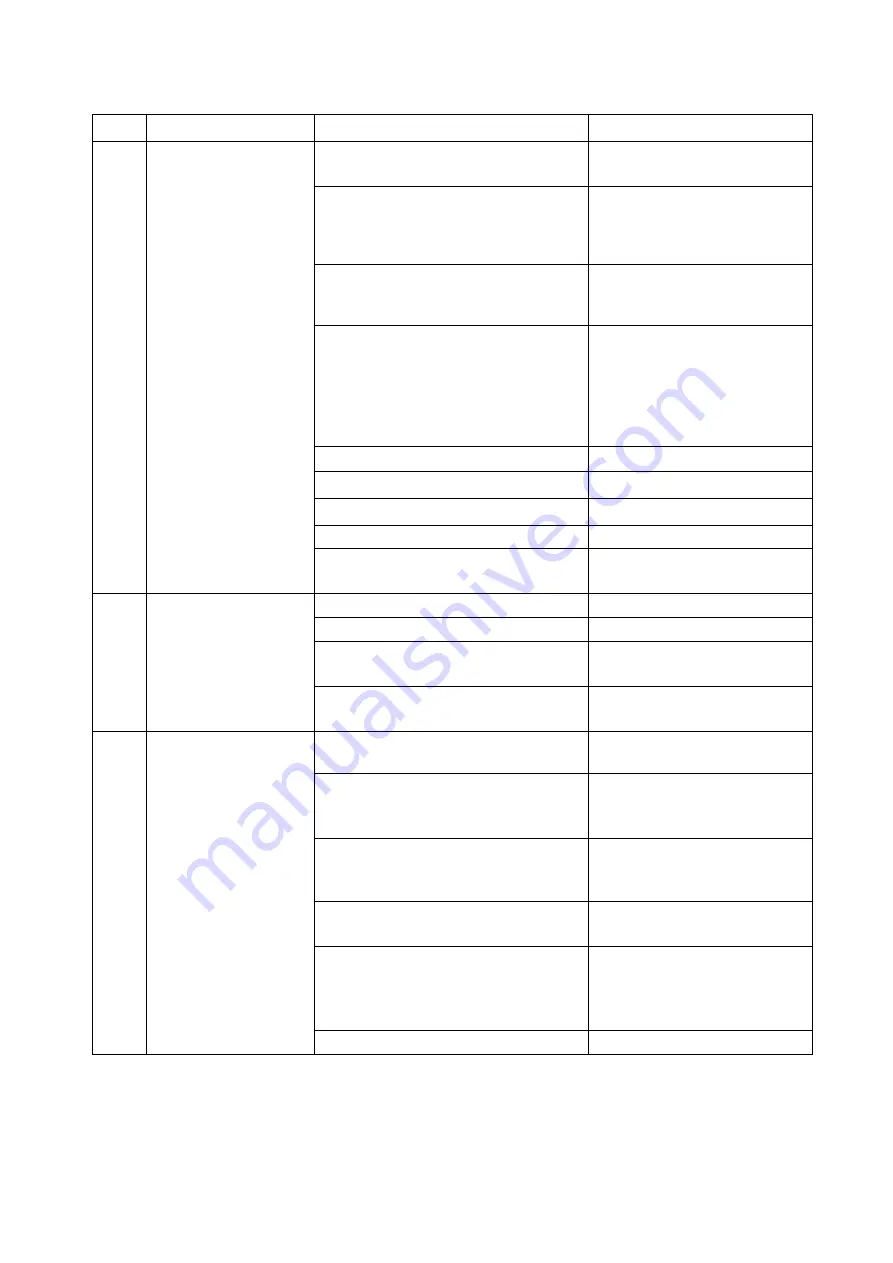
17
NO.
Failure
Causing
Solution
7
Setting cutting
thickness cannot be
achieved
1
、
Input voltage cannot get to
rated voltage
Inputting voltage
2
、
Input power supply capacity is
toosmall and cutting line
preesure is too big
Increase input power supply
capacity
3
、
Input compressure air pressure
is too low or too high
Adjusting the air pressure
4
、
Input air flow is too small,such
as preesure meter drops to
0.3Mpa during the
operation ,and pressure recover
after stop working
Increase the compressed air
flow to 300L/min
;
If the air
hose is small ,please change
the hosediameter to more
thanΦ8mm
5
、
Cutting speed is too fast
Reduce cutting speed
6
、
Nozzle burned
Change
7
、
Electrode has burned
Change
8
、
Nozzle size is not fitted
Change to the right size
9
、
Air hose or cutting cable
damaged
Repair or change
8
Kerf with wide
incision and poor
quality
1
、
Cutting speed is too slow
Adjusting speed
2
、
Nozzle and electrode burned
Change
3
、
material
、
thickness and option
of thickness have wrong position Adjusting
4
、
Nozzle type is wrong and
diameter is too big
Change a right size one
9
Torch burned
1
、
Nozzle or electrode loosing
Fasten the nozzle or
electrode
2
、
Torch wire connector
loosing ,or cable /hose
damaged
Check on time
3
、
Torch connrctor with poor
insulation condition
Make sure the torch
connector with good
insulation
4
、
Shield cap of cutting torch has
been damaged
Change on time
5
、
Compressed air is over wet
Clear the water in “air
pressurevalve”,if the air wae
over wet ,please install
water flilter Lv1~2
6
、
Electrode burned
Change a new one