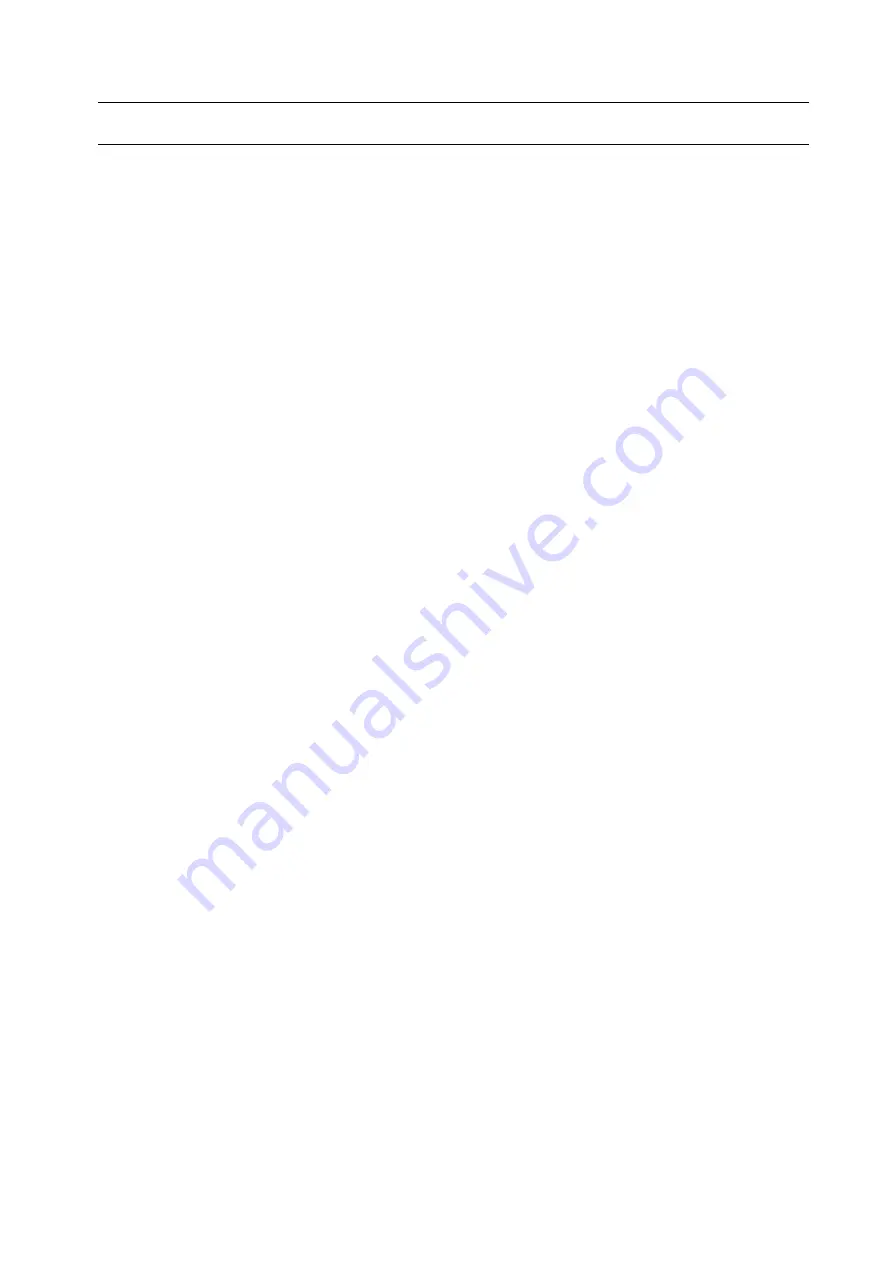
-12-
6
、
OPERATION
6.1 GMAW operation
6.1.1 Preparation
(1)Connect machine according to FIG 1.
(2)Open up the middle panel, shift“MMA/TIG/CO2”swith onto “CO2”model.
(3)Switch on the power supply MCB, the machine’s “power”indicator turns
light, cooling fan begins running and regulator turns heating.
(4)Select suitable wire for work piece, and select suitable wire-feeding roller
and contact lip of torch according to wire diameter.
(5)Press “feed sire by manual”knob and adjust “welding current” knob for
feeding the wire into torch.
(6)Shift “gas test/weld”switch onto“gas test”position, adjust regulator valve
for suitable flow value. After gas test shift the switch onto “weld” position.
6.1.2 Welding Operation
6.1.2.1 Spot welding or short welding
(1) Shift “crater arc on/off”onto “off” position
(2) Adjust “welding current” and “welding voltage” onto suitable value
according to welding technology (FIG 7 refer to GMAW technology
criterion).
(3) Press torch switch for welding, loosen torch switch for stop welding.
6.1.2.2
Long welding or welding in large current
(1)Shift “crater arc on/off” onto “on” position.
(2)Adjust “welding current”, “welding voltage”, “crater current” and “crater
voltage” according to welding technology.
(3)Press torch switch for arc ignition, then the machine goes onto normal
welding position. Here the welder can loosen torch switch for continuous
welding. If wants to stop welding, press torch switch again, now the
machine turns onto “crater arc” position, and the output current is
decreasing. After loosening the torch switch the welding stops.
(4)During welding process, adjust “Arc Characteristics” knob could change
arc stability, penetration and spatter loss coefficient.
6.2 SMAW Operation
6.2.1 Preparation
(1) Connect machine according to FIG 2.
(2) Shift “MMA/TIG/CO2” switch onto “MMA” model.
(3) Switch on the power supply MCB, the machine’s “power” indicator turns
light, cooling fan begins running.
(4) Select suitable electrode according to work piece.