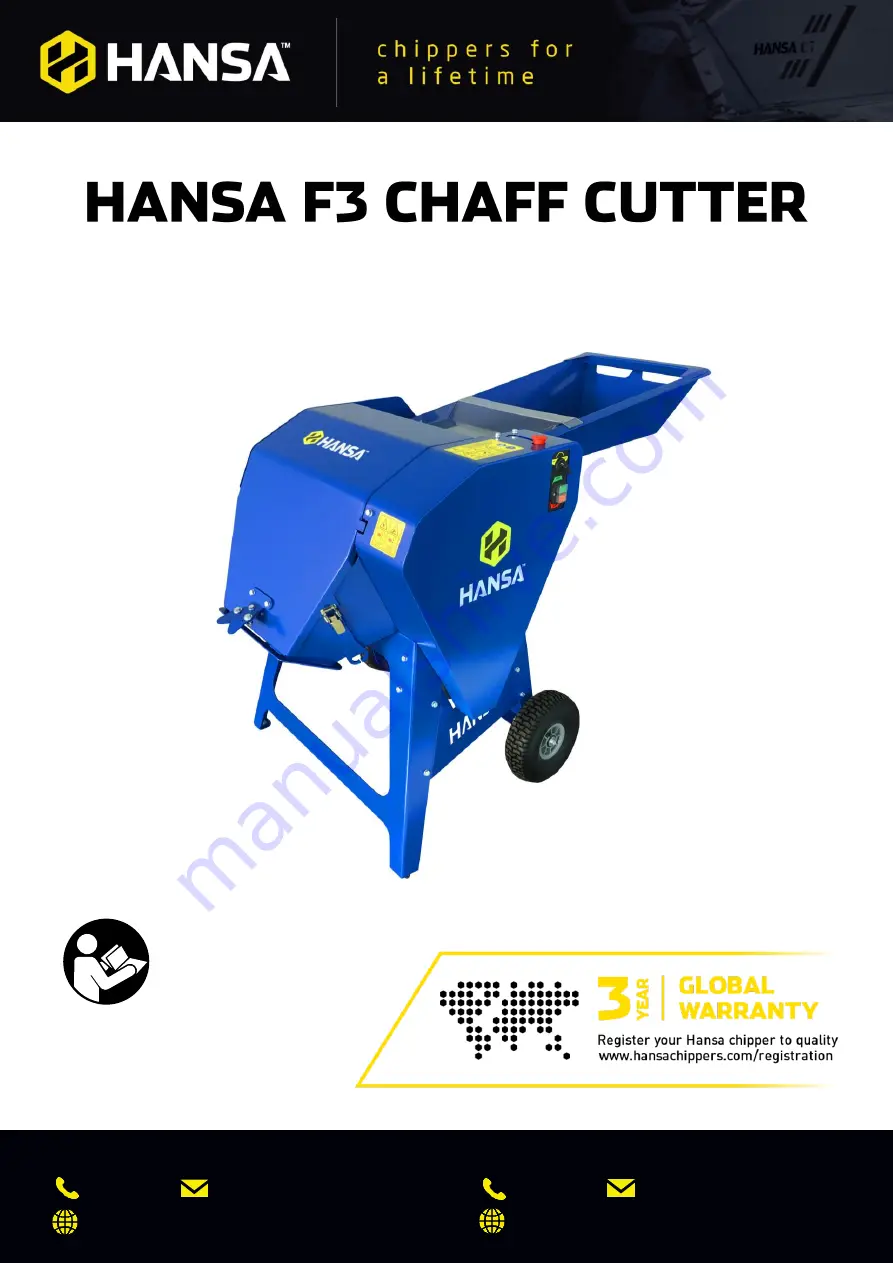
HANSA NEW ZEALAND
+64 7 849 4749 [email protected]
www.hansaproducts.co.nz
HANSA AUSTRALIA
1800 426 722 [email protected]
www.hansaproducts.com.au
Operation, maintenance and safety manual
All operators must fully read and understand
this operator’s manual
before using the chipper.
Keep this manual for future reference.