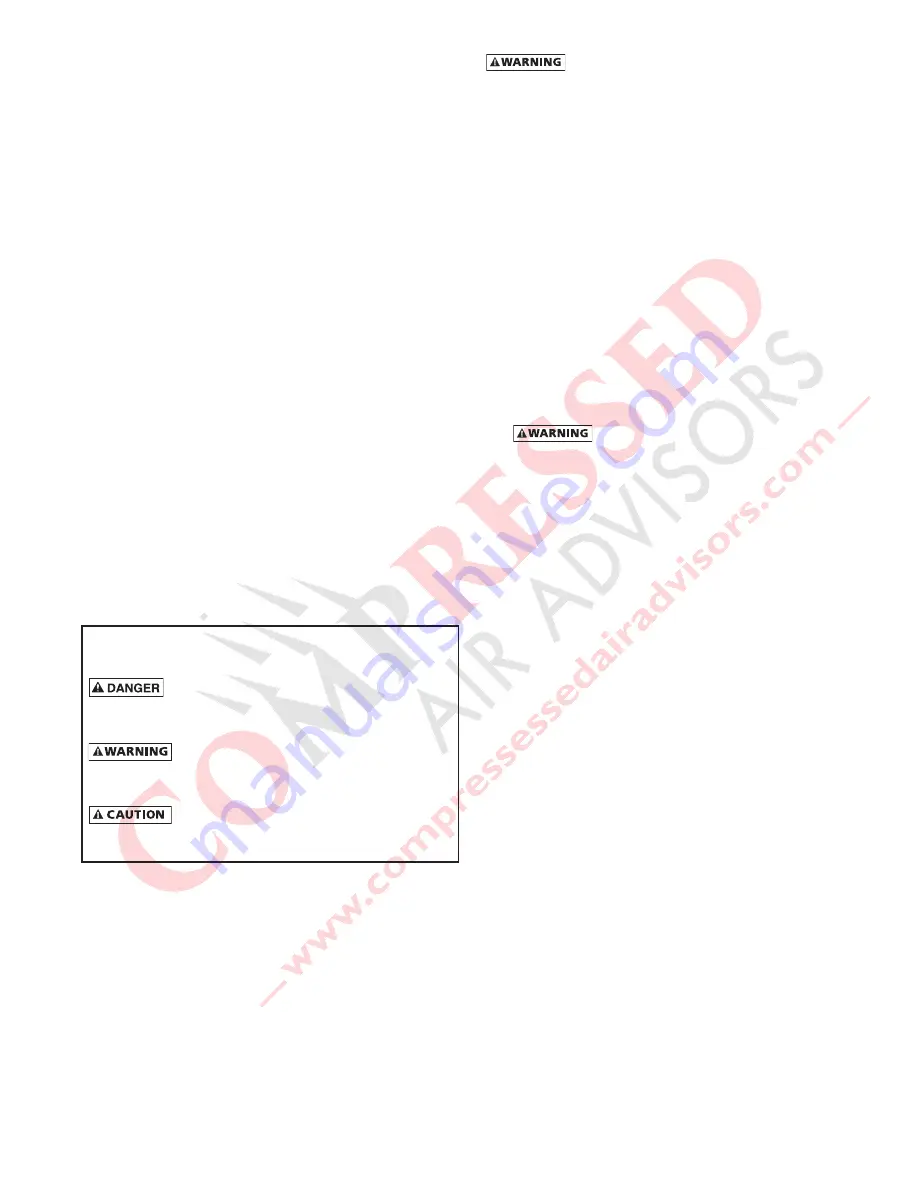
1
INTRODUCTION
Compressed air is generated by compressing atmospheric air
of which contains moisture and other containments, into high
pressure air. After compression, the air is not saturated but when
it is cooled by the aftercooler, the RH remains 100%.
If it travels down the pipe line and cools further, moisture starts
to condensate into liquid water. Condensate water in the pipe
line is harmful to the manufacturing process as it causes rust
or sludge etc.
In order to avoid this problem, the only solution is to dry the
compressed air with an air dryer. Refrigerated compressed air
dryers are used as a cost effective and energy efficient solu-
tions for eliminating moisture from the compressed air system.
SPX Flow’s discovery of using Phase Change Material (PCM) as
a component in the refrigerated compressed air dryer to pro-
duce latent heat has encouraged great energy savings. Through
latent heat properties, it is able to save up to 99% of energy at
no load condition. This is indeed a breakthrough in refrigerated
compressed air dryer technology.
SAFETY
The dryers are designed and built with safety as a prime con-
sideration; industry accepted safety factors have been used in
the design. Each dryer is checked at the factory for safety and
operation. All necessary adjustments are made before shipment.
Follow the maintenance schedules outlined in this manual for
good performance and safe operation.
Only qualified personnel with proper tools should do mainte-
nance.
Safety instructions in this manual used to indicate hazard
seriousness levels are classified as follows:
Immediate hazard which WILL result in severe injury or
death.
Hazard or unsafe practice which COULD result in severe
injury or death.
Hazard or unsafe practice which COULD result in minor
injury or product damage.
Carefully read the following safety rules before proceed-
ing with installation, operation or maintenance. The rules
are essential to ensure safe dryer operation. Failure to
follow these rules may void the warranty or result in dryer
damage or personal injury.
1. Do not install or try to repair a dryer that has been damaged
in shipment. See Receiving and Inspection for instructions.
2. Compressed air and electricity have the potential to cause
personal injury or equipment damage. Before doing any
work on the dryer, be sure the electrical supply has been
locked and tagged and the internal pressure of the dryer
has been vented to the atmosphere.
3. Do not operate the dryer at pressures or temperatures
above the maximum conditions shown on the data plate.
4. Always supply electrical power that complies with the volt-
age shown on the data plate.
5. Do not readjust the dryer without factory authorization.
6. Do not operate the dryer with any dryer cabinet panel
removed.
Cooling air flow across the condenser may be reduced
if a dryer panel has been removed while the dryer
is operating, resulting in the dryer not functioning
properly and/or dryer failure. Failure to follow these
instructions may result in a non-warrantable dryer
failure.
7. Only a competent refrigeration mechanic works on the
refrigeration system.
8. Use only manufacturer’s genuine replacement parts. The
manufacturer bears no responsibility for hazards caused
by the use of unauthorized parts.
INSTALLATION
Inspect the dryer closely when it is received. Record any indica-
tion of damage on the delivery receipt, especially if the dryer
will not be immediately uncrated. Obtain the delivery person’s
signed agreement to recorded damages to facilitate future
insurance claims .
Since the dryer is shipped F.O.B. Factory, the manufacturer’s
responsibility for the shipment ceases when the carrier signs
the bill of lading.
If goods are received short or in damaged condition, notify the
carrier and insist on a notation of the loss or damage across
the face of the freight bill. Otherwise no claim can be enforced
against the carrier.
If concealed loss or damage is discovered, notify your carrier
at once and request an inspection. This is absolutely necessary.
Unless you do this, the carrier will not consider any claim for
loss or damage. The carrier will make an inspection and may
grant a concealed damage notation. If you give the carrier a
clear receipt for the goods that have been damaged or lost in
transit, you do so at your own risk and expense.
The manufacturer is willing to assist you in collecting claims for
loss or damage. Willingness does not make the manufacturer
responsible for collecting claims or replacing material. Claim
filing and processing is your responsibility.
Summary of Contents for SPX Flow FLEX Series
Page 25: ...23 NOTES ...