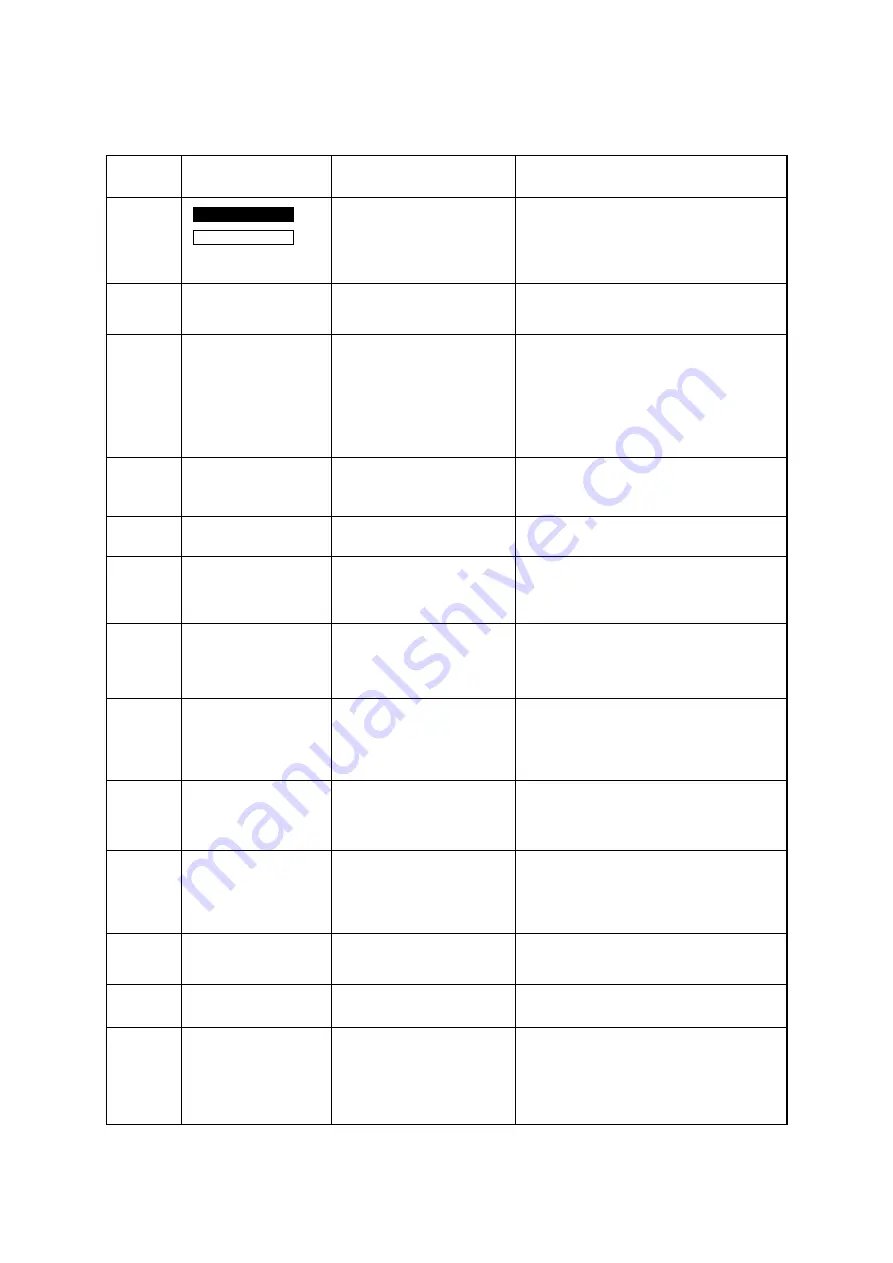
36
Fault table of lift (oil pump) controller
LED
code
PROGRAMMER
LCD DISPLAY
EXPLANATION
POSSIBLE CAUSE
off
On
NO voltage or controller
is not working, error (such
as MCII defective)
0,1
■ ¤
controller work normally,
no error
1,1
¤ ¤
EEPROM defective
1.
EEPROM miss data
2.
EEPROM data check error
,
use
programmer 1311 to change any
parameter can delete the error.
1,2
¤ ¤¤
Hardware defective
1.
MOSFET short down.
2.
Motor circuit is an open circuit.
2,1
¤¤ ¤
Low voltage
Battery voltage is too low.
2,2
¤¤ ¤¤
Lifting lock.
The function of lifting lock of the
controller is touch off.
2,3
¤¤ ¤¤¤
Order
fault
(
Startup
lockout
)
Any switch of SS1-SS4 closes earlier
than KSI or INTERLOCK.
3,2
¤¤¤ ¤¤
Contact err
1.
Main contact bonded
。
2.
The set of parameter
―CONTACT
CNTRL‖
is wrong.
3,3
¤¤¤ ¤¤¤
Pre-charge fault
1.
Pre-charge circuit work with err.
2.
Motor short down.
3,4
¤¤¤ ¤¤¤¤
Contact has not been
installed or is not close.
1.
The connection of main contact
coil loose.
2.
Main contact works abnormally.
4,1
¤¤¤¤ ¤
Low -voltage protect.
The voltage of battery is lower than the
set value of
―LOVOLT CUTBACK‖
4,2
¤¤¤¤ ¤¤
Over-voltage protect.
The battery voltage is too high.
4,3
¤¤¤¤ ¤¤¤
temperature
protect
(
over-/under-temp
)
1.
The temperature of controller is
too high or too low.
2.
Temperature
sensor
works
abnormal.
Summary of Contents for CPD10J
Page 2: ......
Page 4: ......
Page 6: ......
Page 22: ...16 ...
Page 57: ...51 ...
Page 58: ...52 WIRING DIAGRAM OF CPD10 15 18 20 25 30J ...
Page 59: ...53 ...
Page 60: ...54 ELECTRICAL SYSTEM PRINCIPLE DIAGRAM OF CPD10 15 18 20 25 30 40 45 50J C2 ...
Page 61: ...55 ELECTRICAL SYSTEM PRINCIPLE DIAGRAM OF CPD10 15 18 20 25 30 40 45 50J D1 ...
Page 63: ...57 7 Maintenance record Date Maintain content Maintainer ...