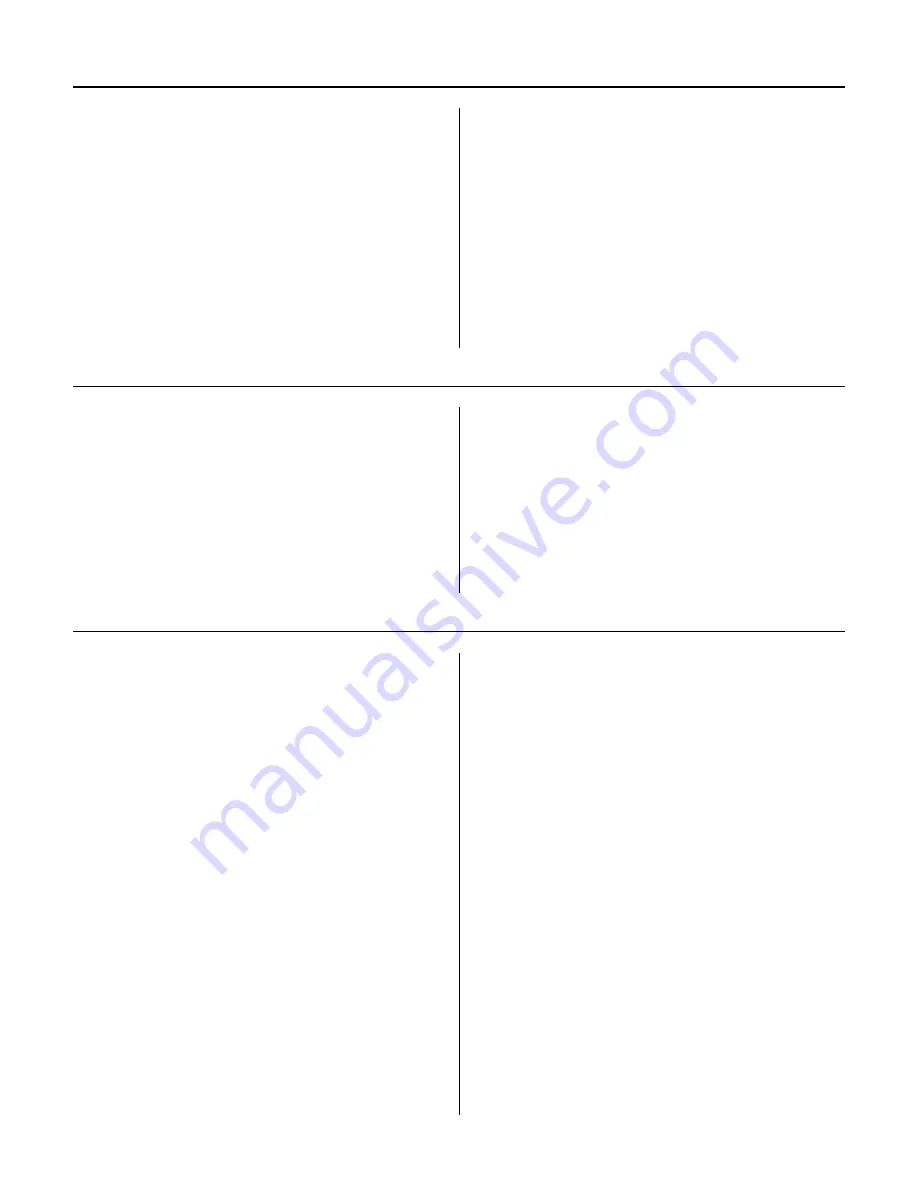
33
Correctly balancing an aerobatic model is critical
to its performance and flight characteristics. Checking
the balance on large-scale models is best done with
two people.
Step 1
Measure back 7
7
/
16
" from the leading edge at the root
rib and mark the location on the bottom of both wing
panels with a felt-tipped pen. This is the recommended
center of gravity (CG).
Step 2
Fully assemble the model. With the airplane upright, lift
the airplane with your index fingers to find the balance
point. The balance point (CG) should be at the marks
made on the bottom of the wing. If not, move the receiver
battery, receiver, or add the necessary weight to the nose
or tail to obtain the correct balance.
Aileron (Measured at inboard end of aileron)
Low
2" (22°) Up
1
7
/
8
" (21°) Down
High
3
3
/
4
" (45°) Up
3
5
/
8
" (43°) Down
Elevator (Measured at trailing edge)
Low
5/8" (9°) Up
3/4" (11°) Down
High
3
1
/
8
" (45°) Up
4
1
/
2
" (50°) Down
Rudder (Measured at counterbalance)
Low
1
5
/
8
" (30°) Right
1
5
/
8
" (30°) Left
High
2
1
/
2
" (45°) Right
2
1
/
2
" (45°) Left
Range Test Your Radio
Step 1
Before going to the field, be sure that your batteries
are fully charged, per the instructions included with
your radio. Charge both the transmitter and receiver
pack for your airplane. Use the recommended charger
supplied with your particular radio system, following the
instructions provided with the radio. In most cases the
radio should be charged the night before going out flying.
Step 2
Before each flying session, be sure to range check your
radio. See your radio manual for the recommended
range and instructions for your radio system. Each radio
manufacturer specifies different procedures for their radio
systems. If using a gasoline engine, check the range first
with the engine not running and note the distance. Next,
start the engine. With the model securely anchored, check
the range again. The range test should not be significantly
affected. If it is, don’t attempt to fly! Have your radio
equipment checked out by the manufacturer.
Step 3
Double-check that all controls (aileron, elevator, rudder
and throttle) move in the correct direction.
Step 4
Check the radio installation and make sure all the
control surfaces are moving correctly (i.e. the correct
direction and with the recommended throws). Test
run the engine and make sure it transitions smoothly
from idle to full throttle and back. Also ensure the engine
is tuned according to the manufacturer’s instructions,
and it will run consistently and constantly at full throttle
when adjusted.
Check all the control horns, servo horns, and clevises to
make sure they are secure and in good condition. Replace
any items that would be considered questionable. Failure
of any of these components in flight would mean the loss
of your aircraft.
Balancing the Model
Control Throws
Preflight at the Field