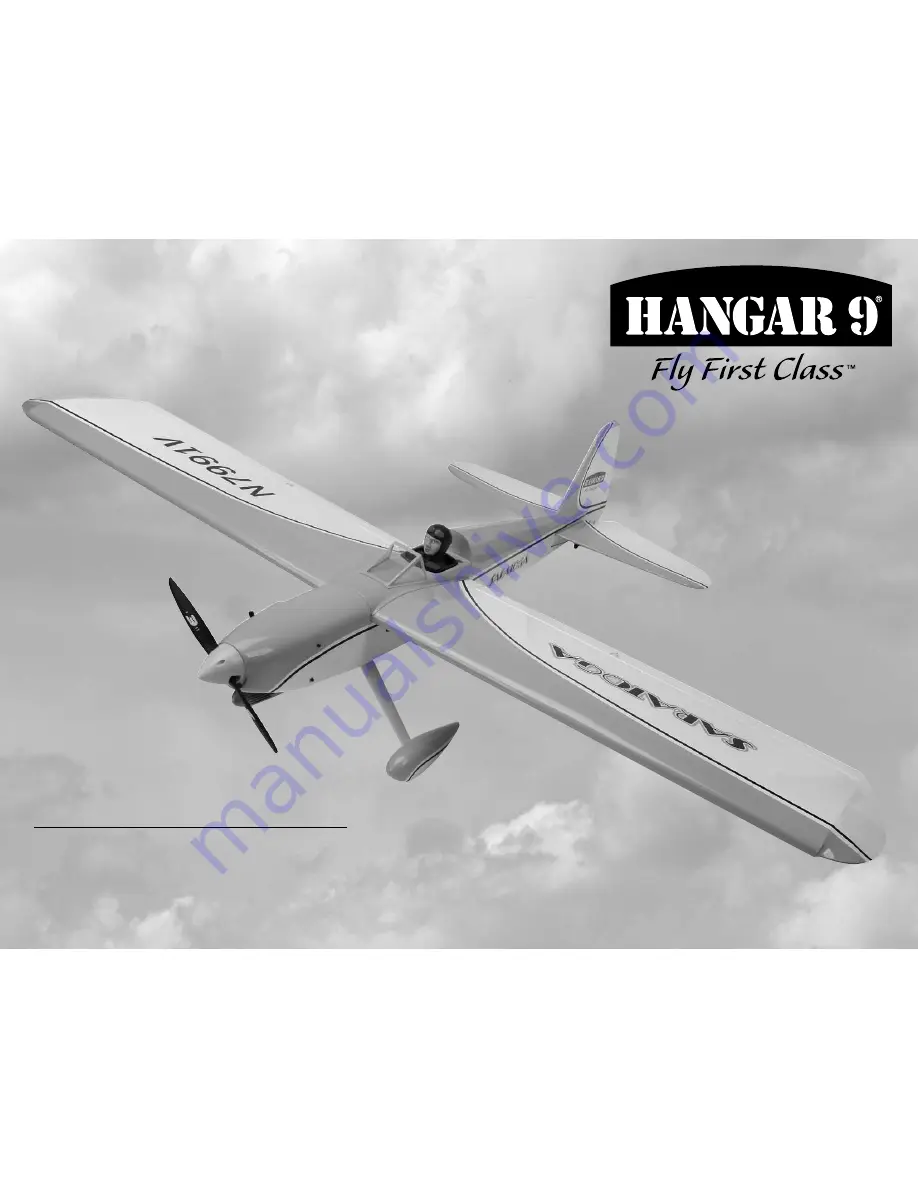
Specifications
Wingspan: ........................................................... 64.2 in (1630mm)
Length: ............................................................49.25 in (1251.8mm)
Wing Area: ................................................694 sq in (44.77 sq dm)
Weight: .................................................. 5.5–6.25 lb (2.49–2.83 kg)
Radio: .......................................................4-channel w/4–5 servos
Engine: ..................... .40–52 2-stroke; .56–82 4-stroke; Power 46
Saratoga 40
Assembly Manual