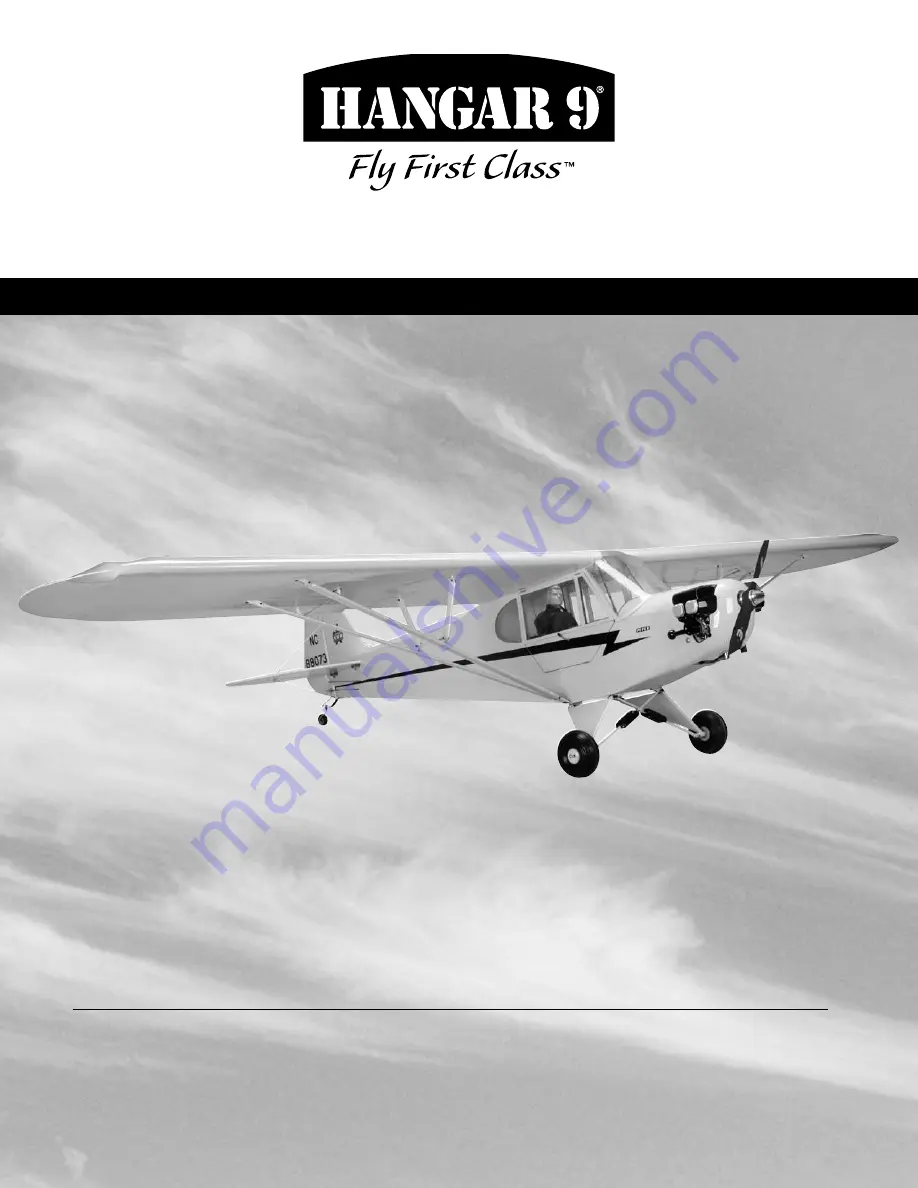
Wingspan....................................106.in.(2692.5mm)
Wing.Area.........................1630.sq.in.(10.52.sq.dm)
Length..............................................68.in.(1727mm)
Weight........................ .14.5–16.5.lb.(6.6.kg–7.5.kg)
Assembly mAnuAl
Piper J-3 Cub
Engine................................... .1.00–1.80.Four-Stroke
............................................. 1.00–1.60.Two-Stroke
....................................................20–26cc.Gasoline
Motor............................................. E-flite.Power.110
Specifications
Summary of Contents for Piper J-3 Cub 40
Page 41: ...41 Building and Flying Notes ...