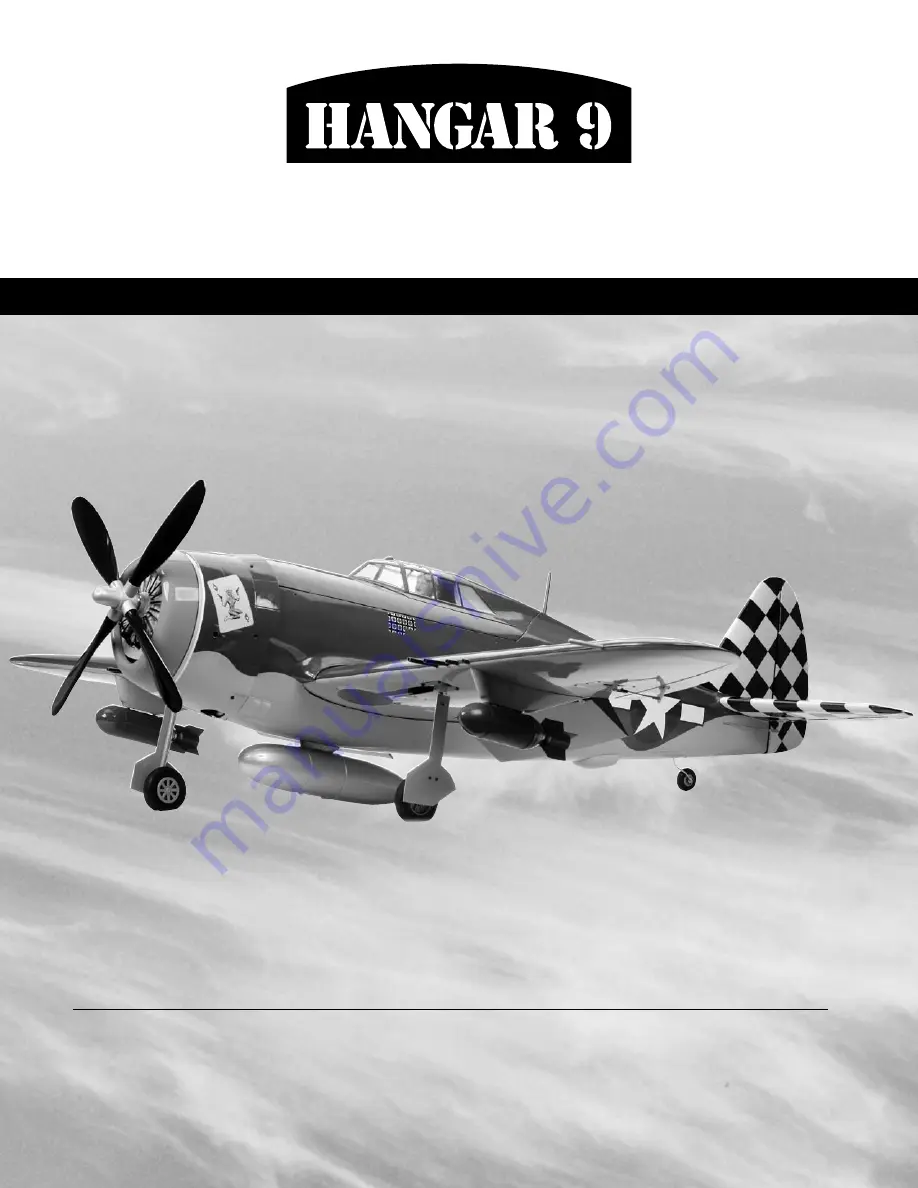
Wingspan: ................................81.25 in (206.4 cm)
Wing Area: ......................1164 sq in (75.09 sq dm)
Length: ..........................................71 in (180.3 cm)
ASSEMBLY MANUAL
P-47 Thunderbolt
Weight: ............................. 15.5–17 lb (7.1–7.7 kg)
Radio: ................................. 6-channel w/10 servos
Recommended Engines: ...........1.20-2.20 4-stroke
...........1.20-2.10 2-stroke
................. 23cc-26cc gas
Specifications
��
�