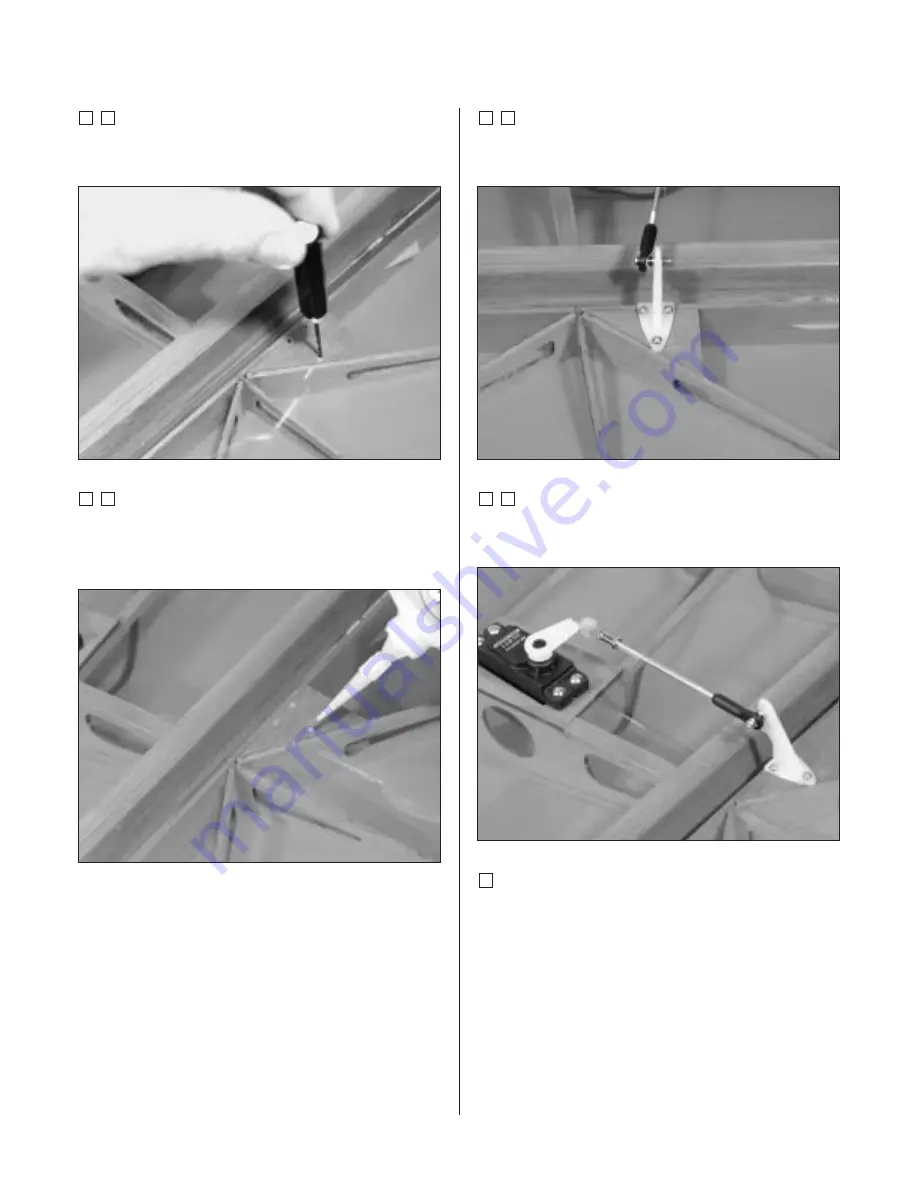
10
Section 3 – Aileron Control Horn Installation
Step 5
Using a 1/16" drill bit, carefully drill the holes for
mounting the control horn.
Step 6
Apply 2-3 drops of Thin CA into each of the three holes.
This will harden the wood and prevent the screws from
pulling out during flight.
Step 7
Attach the control horn to the aileron using three 2mm x
20mm self-tapping screws.
Step 8
Adjust the aileron linkage so the aileron is centered
when the linkage is connected to the servo.
Step 9
Repeat Steps 1 through 8 for the remaining aileron.