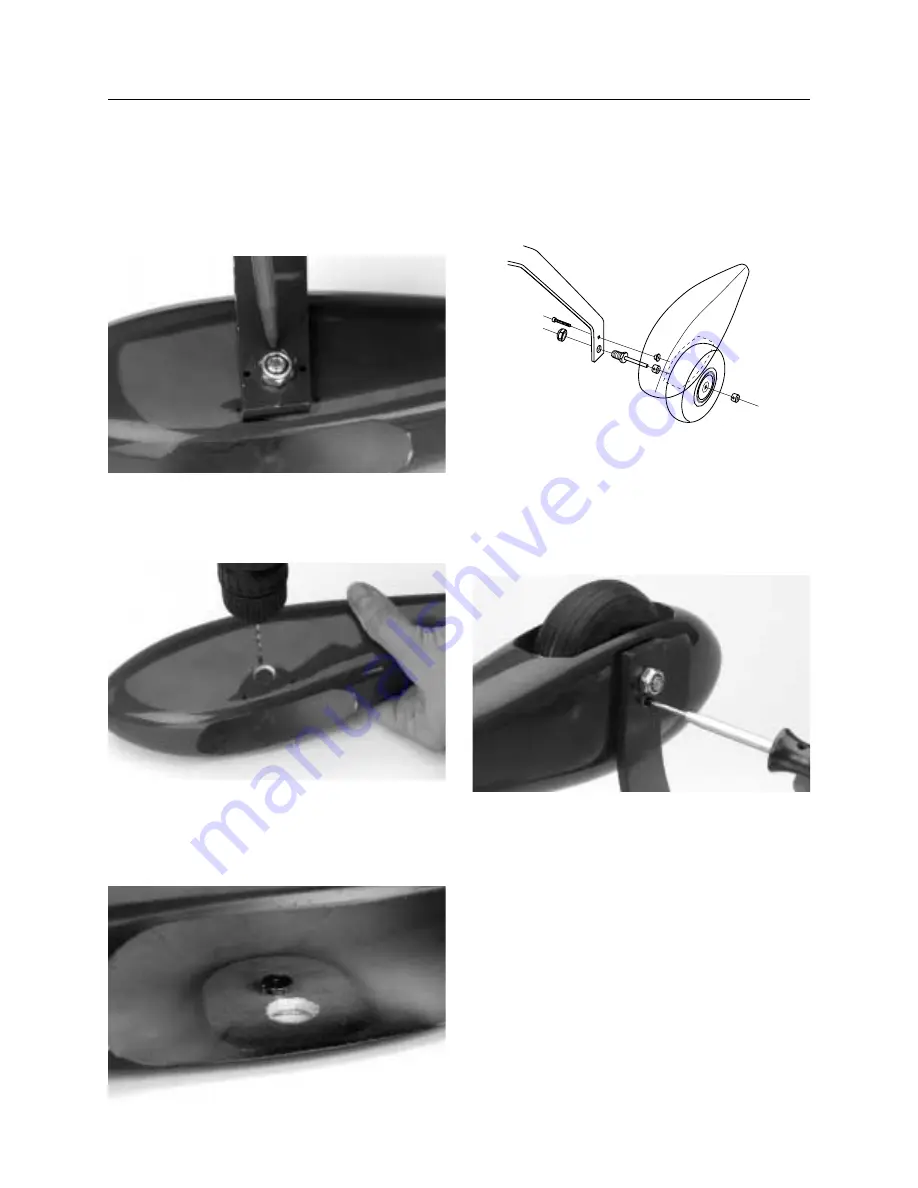
22
Step 4.
Fit the wheel pants over the axle and align with the
landing gear as shown. With the wheel pants properly aligned,
mark the mounting hole position through the landing gear on the
wheel pants using a pen.
Step 5.
Remove the wheel pants and carefully drill a
1
/
8
" hole
through the pants at the marked hole.
Step 6.
Install the 4-40 blind nut from inside the wheel pants as
shown. Later we will fully seat the blind nut into the plywood
when installing the pants on the landing gear.
Step 7.
Install onto the axle in the following order: wheel pant,
3
/
16
" collar, wheel, then another
3
/
16
" collar. It will be necessary
to fit the parts inside the wheel pant and slide them onto the axle.
Step 8.
Fasten the wheel pants in place using 4-40 x
5
/
8
"
screws with washer and split washer through the landing gear
and into the blind nut in the wheel pants. Use Blue Locktite
®
and
securely tighten the screws to properly seat the blind nuts.
Section 8: Installing the Landing Gear
CONTINUED