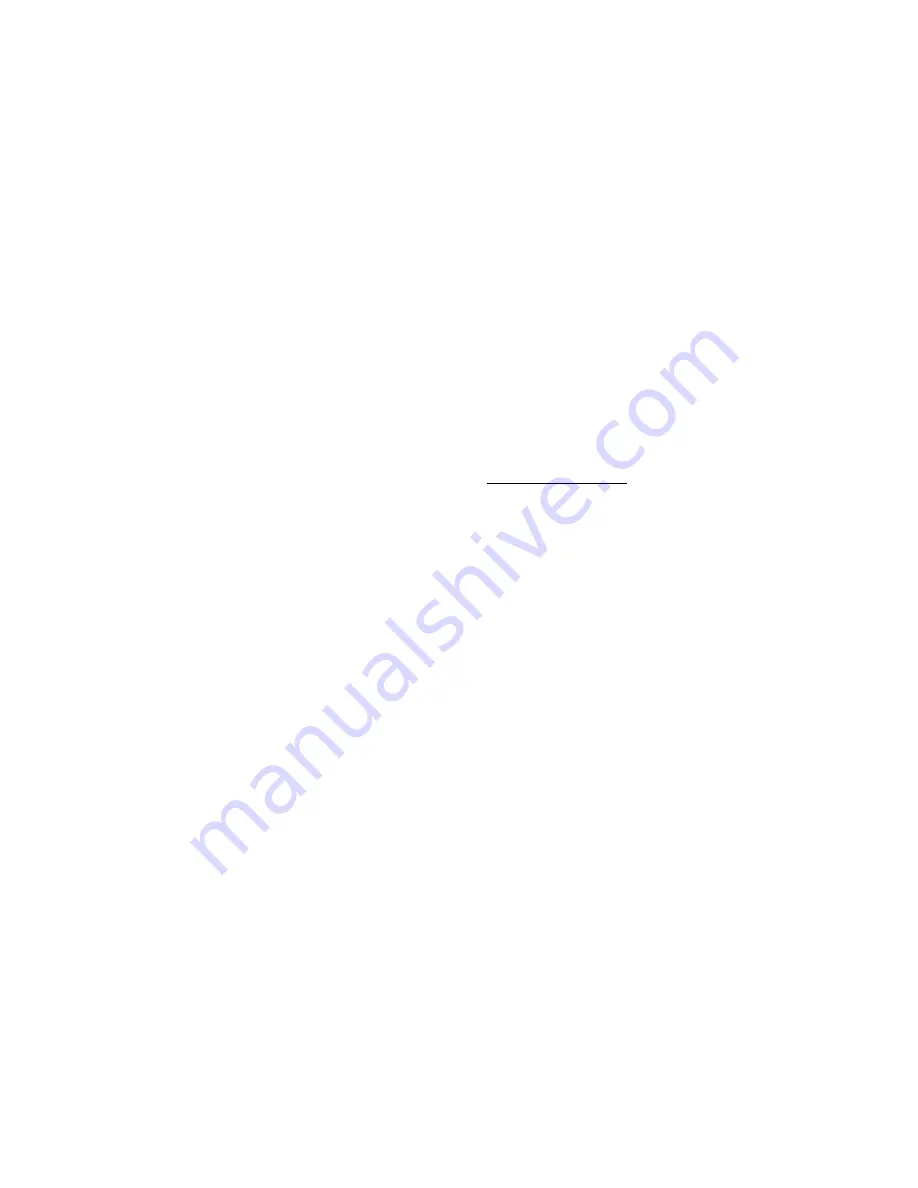
HAMWORTHY HEATING LTD
WARMWELL
500001091/F
connection CN21 from the main PCB), the boiler
should lockout after approximately one second.
Check that the flame has been extinguished.
Remove multi-meter and replace wire link to the
plug CN21. If a sequencing interface module is fitted
set the hand/auto switch ‘SW1’ on the boiler main
PCB (refer to Figure 11.1 p26) to the ‘auto’ position.
Wait at least 15 seconds before pressing re-set
button on fascia to re-set controller. After a waiting
period the boiler will light and run normally.
11.10 User’s Instructions
When the above is complete, the boiler owner or
their representative should be made aware of the
lighting and operating instructions fitted to the inside
of the boiler door. A practical demonstration should
be given describing each functional step. In
particular, care should be taken to ensure that the
discharge from the condensate trap, at the rear of
the appliance, is free from blockage. This Installer's
Guide and User’s Instructions should then be
handed over and be kept in a safe place for easy
reference.
12.0 FAULT FINDING
12.1 Safety Features Summary
The main PCB is fitted with neons to indicate correct
operation of the boiler functions – refer to Figure
12.1 (p32).
Should the control thermostat fail, causing an
overheat condition, the temperature limiter will trip
thus creating an immediate shutdown regardless of
firing mode. An overheat neon on the
controls
fascia
will indicate that this condition has occurred.
The door will have to be removed to permit access
to the temperature limiter re-set pin. If, after
pushing the pin in, the light on the fascia does not
go out and the boiler does not light up, it could be
that the boiler is still too hot, i.e. the control
thermostat has not re-set. An investigation should
be carried out to ascertain the reason for the
overheating. An obvious reason would be too low a
water flow rate through the boiler.
The flame is under constant supervision by the
burner logic controller. This is accomplished by
measuring the flame's ability to rectify an AC
current. If the flame diminishes for whatever reason
and the rectified current drops below the controllers
minimum (0.7
µ
A DC), the controller will induce a
non-volatile lockout which will require a manual re-
set (situated on the controls fascia) to re-start the
control sequence. See Figure 12.2 (p34/35) for
possible corrective scenarios.
Pressure switches are fitted to monitor the correct
operation of the induced draught fan fitted to the
Warmwell. It ensures sufficient air is pulled through
the boiler to facilitate correct combustion. The
For Natural Gas the gas pressure governor control
system is configured for a nominal gas inlet
pressure of 20mbar with a maximum inlet pressure
of 25mbar. The Warmwell 120 and 140 boiler is
fitted with a unique flow share gas valve
arrangement. Refer to Figure 11.7b (p30) to
establish method of adjustment of the by-pass
throttle arrangement.
NOTE!
The by-pass valve
throttle
MUST
only be used as a coarse adjuster,
the main control
MUST
always be accomplished by
the high/low control valve.
For Propane firing boilers, the nominal gas inlet
pressure is 37mbar, with a maximum inlet pressure
of 47mbar. All Propane firing boilers are fitted with a
low gas pressure switch (set at 20mbar). Should
the gas supply pressure fall below this level, the
boiler
will not
operate. All Propane firing boilers are
fitted with a single gas valve providing high and low
control. Refer to Figure 11.7a (p29).
Remove manometer and close pressure test point.
Record all readings for future reference on relevant
commissioning sheet. Allow system to warm up
sufficiently to check operation of control thermostat.
A combustion check must be taken when first
commissioning the boiler. A plugged sample hole is
provided in the top of the stainless steel collector
hood.
NOTE!
Care should be exercised if the boiler
is firing as the flue can achieve temperatures which
can produce injury if touched.
Combustion figures for Natural Gas should be as
follows: -
CO
2
= 7-8% condensing or 8-9% non-condensing
(Dry flue gas).
CO = 0-50 ppm: however figure should not exceed
200 ppm under normal operating conditions.
Details of the flue gas composition relating to
propane firing can be found in Appendix ‘A’ (p41).
11.8 Temperature Limiter (Limit Thermostat)
Reset and test the operation of the temperature
limiter by firmly pressing the button (in the controls
fascia), removing the clip and bulb from the pocket
and carefully applying a heat source to the bulb. The
reset button should operate. If satisfactory, refit the
bulb in the pocket and secure with the clip.
Check temperature limiter setting. Removing plastic
cover (unscrewing) can achieve this if fitted. Undo
holding nut and withdraw into the controls housing.
Adjust if required and replace in reverse order to
above.
11.9 Safety Checks
To check for correct operation of the controller,
break the multi-meter
µ
A circuit (remove plug
31
Summary of Contents for Warmwell 120
Page 50: ...HAMWORTHY HEATING LTD WARMWELL 500001091 F NOTES 44...
Page 51: ...Notes...