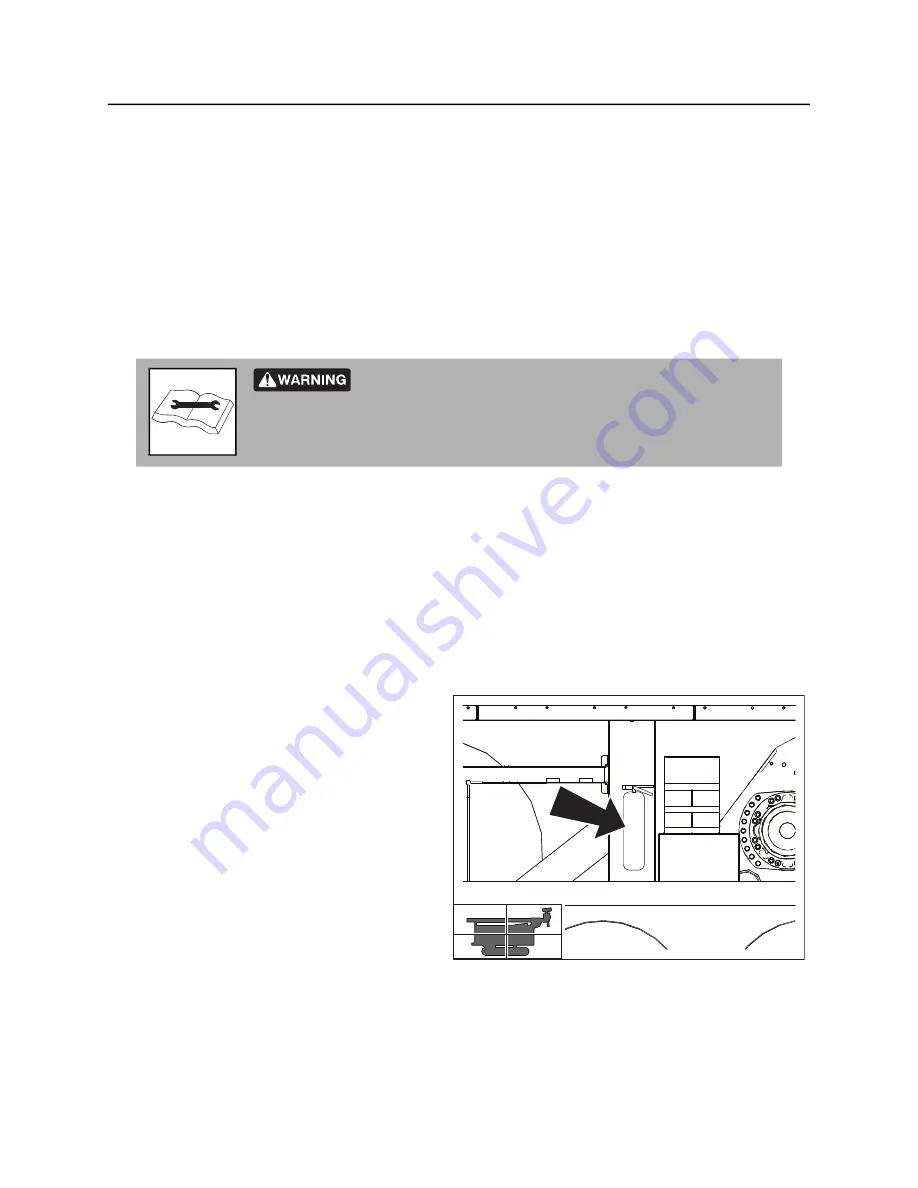
HG2200/HG2200AT Operator’s Manual
Check Supplies and Prepare Equipment
62 - Prepare
Fluid Levels
•
fuel
•
hydraulic fluid
•
engine coolant
•
engine oil
Condition and Function
•
all controls
•
filters
•
couplers
•
tracks or tires
•
hoses and valves
Assemble Accessories
Fire Extinguisher
If required, mount a fire extinguisher near the
power unit but away from possible points of
ignition where shown. The fire extinguisher should
always be classified for both oil and electric fires.
It should meet legal and regulatory requirements.
Improper control function could cause death or serious injury. If
control does not work as described in instructions, stop machine and have it
serviced.
j64om067w.eps
Summary of Contents for HG2200
Page 51: ...HG2200 HG2200AT Operator s Manual Battery Disconnect 50 Controls ...
Page 75: ...HG2200 HG2200AT Operator s Manual Retrieve Tracked Unit 74 Transport ...
Page 87: ...HG2200 HG2200AT Operator s Manual Finish Installation 86 Burst Pipe ...
Page 129: ...HG2200 HG2200AT Operator s Manual As Needed 128 Service ...
Page 133: ...HG2200 HG2200AT Operator s Manual Declaration of Conformity Information 132 Specifications ...
Page 137: ...HG2200 HG2200AT Operator s Manual 136 Service Record Service Performed Date Hours ...
Page 146: ......