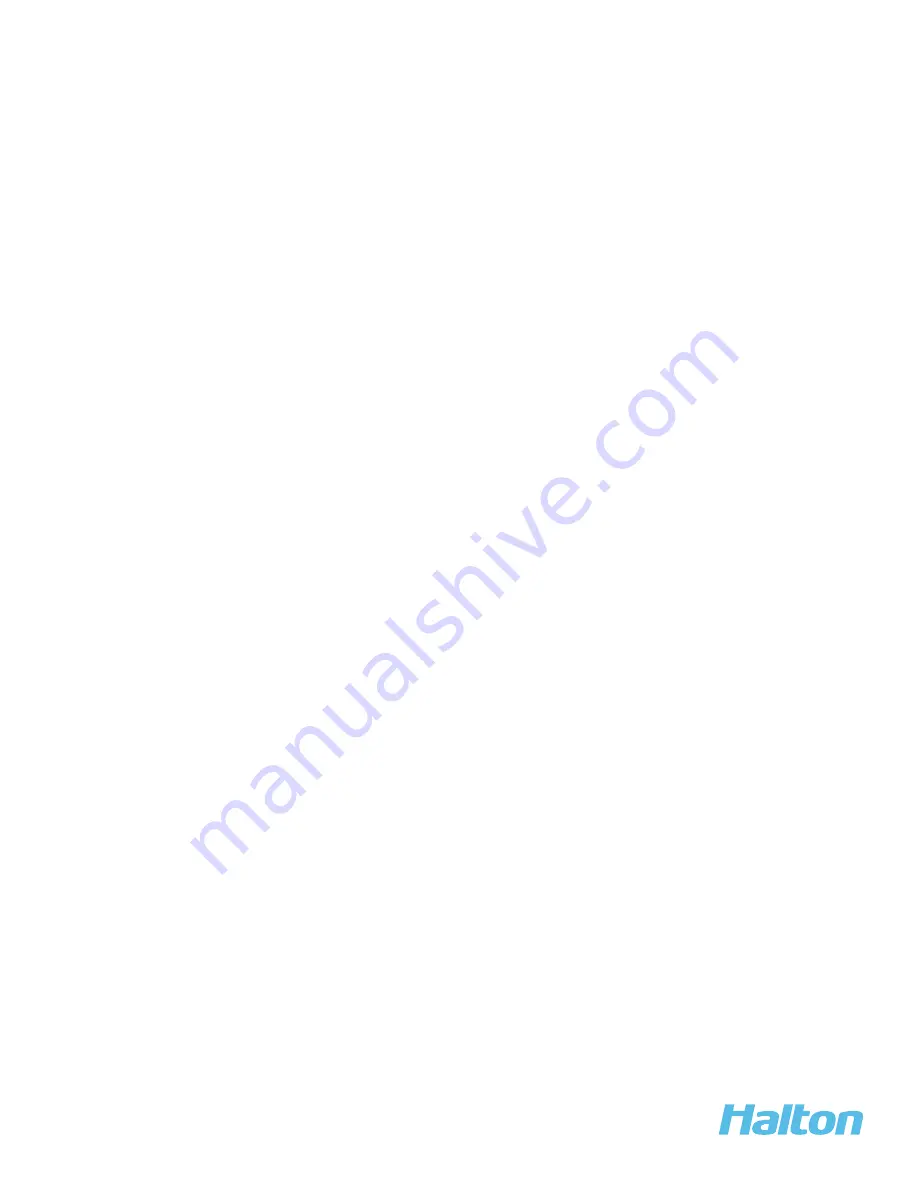
18
EcoloAir Operation, Maintenance & Service Manual
EA
OMSI/0
1
2
0
09/re
v1/EN
ROUTINE MAINTENANCE
1. A preventive maintenance program is an important aspect of an effective safety program. Consult
the manufacturing or other qualified service agents with question concerning changes observed
during periodic inspections and routine maintenance.
2. The fan manufacturer’s operating and maintenance recommendations, as well as the components
manufacturer’s instructions (such as motor, bearing, drives, etc.) should be strictly followed.
3.
Maintenance should always be performed by experienced and trained personnel who are
aware of the hazards associated with rotating equipment.
Do not attempt any maintenance
on a fan unless the fan power supply has been locked out and tagged out and the impeller has
been secured.
4. When performing maintenance functions which include disassembly of the fan, careful
consideration should be given to the size, weight center of gravity, and lifting means of the fan
components. It should also be noted that the outboard bearing on some fans such as
arrangements 1,8,9 and 10 is often cap-loaded. Removal of the securing means may result in a
sudden change in impeller position.
5. Historical data is often the best indicator for determining the operational condition of the fan.
Maintenance logs which include lubrication, vibration levels, temperature levels, power
requirements, inspection, and other pertinent records should be maintained and consulted as
necessary when assessing the condition of the fan.
6. Under normal circumstances, handling clean air, the system should require cleaning only once a
year. However, the fan and system should be checked at regular intervals to detect any unusual
accumulation.
7. The fan impeller should be specially checked for build-up of material or dirt which may cause an
imbalance with resulting undue wear on bearings and belt drives. A regular maintenance
program should be established as needed to prevent material build-up.
8. Periodic inspection of the rotating assembly should be made to detect any indication of weakening
of the rotor because of corrosion, erosion, or metal fatigue. Where signs of deterioration are
found, lock out and tag out the impeller until the unit had been inspected and approved by a
qualified consultant.