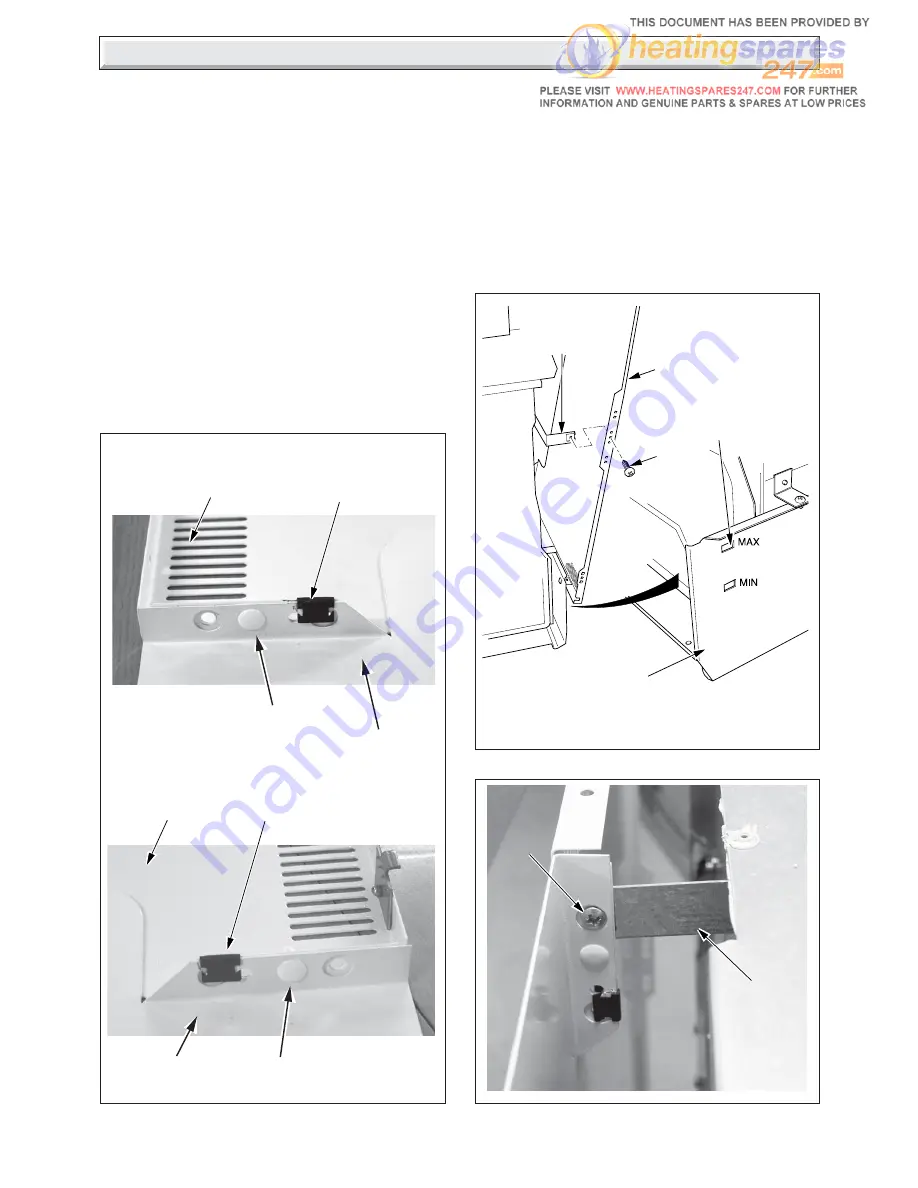
14
2000225095B
4.10 Side In-fill Panel (If required)
A side in-fill panel is supplied with the boiler, which can be fitted
at the rear of the left or right hand side casing but can be
discarded if the water connections are made on both sides of
the boiler or if the boiler is screened by fixtures. The in-fill panel
will usually be fitted on the side where there are no pipework
connections.
Insert the push fit plastic location peg, supplied, through the in-
fill panel and side casing holes and secure with the spring clips,
see diagram 4.14.
NOTE
The boiler is assembled at the factory with the control box and
heat shield fitted in the lower casing height position.
Diagram 4.14
Diagram 4.16
SCREW
SIDE CASING
(R.H. SHOWN)
9863
SIDE CASINGS FITTING
Diagram 4.15
MAX.
SIDE
CASING
(R.H.)
MIN.
BOILER
PLINTH
FRONT
CASING
BRACKET
No. 8
SCREW
(4)
LOCATING
SLOTS
4 Installation
UPPER
CASING
BRACKET
4.11 Side Casings
Fit the side casings by locating their lugs into the appropriate
slot in the boiler plinth, see diagram 4.15, depending on the
required height, there are two options, see section 1.7.
Secure the casing sides to the front and rear upper casing
brackets with self-tapping screws supplied, see diagrams 4.15
and 4.16.
PLASTIC
PEG
PLASTIC
PEG
SPRING
CLIP
SIDE
CASING
(R.H.SHOWN)
UPPER VIEW
LOWER VIEW
SPRING
CLIP
SIDE
CASING
(R.H. SHOWN)
IN-FILL
PANEL
IN-FILL
PANEL