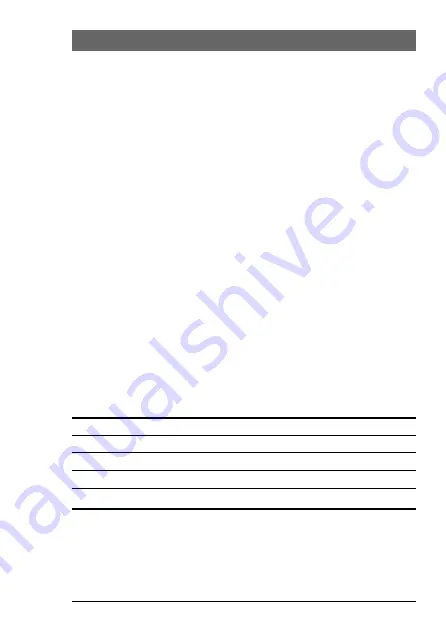
19
2.2 Mounting
Xgard
should be installed at the designated location with the sensor
pointing down. This ensures that dust or water will not collect on the
sensor and stop gas entering the cell. The mounting detail is shown in
Diagram 2. Care should be taken when installing the detector to avoid
damaging the painted surface of the junction box and sensor retainer.
2.3 Cabling requirement
Cabling to
Xgard
must be in accordance with the recognised standards
of the appropriate authority in the country concerned and meet the
electrical requirements of the detector.
Crowcon recommend the use of steel wire armoured (SWA) cable and
suitable explosion proof glands must be used. Alternative cabling
techniques, such as steel conduit, may be acceptable provided
appropriate standards are met.
Xgard
requires a dc supply of 830 V and is loop powered. Ensure there
is a minimum of 8 V at the detector, taking into account the voltage drop
due to cable resistance and the sense resistance of the control panel to
which it is connected.
For example, a nominal dc supply at the control panel of 24 V has a
guaranteed minimum supply of 19.5 V. The circuit may demand up to
20 mA. Given a sense resistor in the control panel of 232 Ohms the
maximum voltage drop allowed due to cable resistance is 6.8 V. The
maximum loop resistance allowed is 340 Ohms (approx.).
A 1.5 mm
2
cable will typically allow cable runs up to 14 km. Table 2 below
shows the maximum cable distances given typical cable parameters.
C.S.A.
Resistance (Ohms per km)
Max. Distance (km)
mm
2
Awg
Cable
Loop
1.0
17
18.1
36.2
9.4
1.5
15
12.1
24.2
14
2.5
13
7.4
14.8
23
Table 2: Maximum cable distances for typical cables
The acceptable cross sectional area of cable used is 0.5 to 2.5 mm
2
(20 to 13awg).
The table is provided for guidance only, actual cable
parameters for each application should be used to calculate
maximum cable distances.
2. Installation
Xgard Type 2