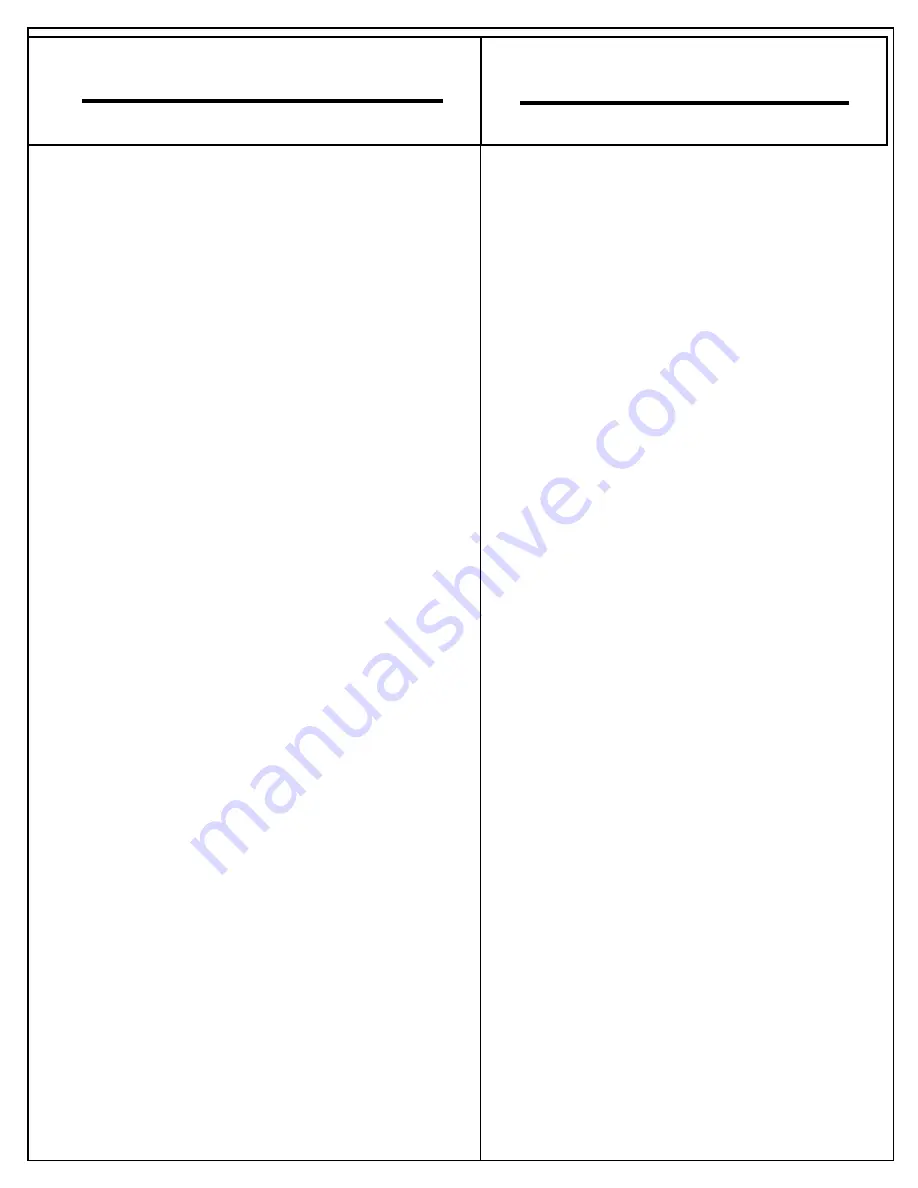
3. For upgrade heater and connector
information see " Service Information".
Compressor Discharge Line
General
While minimum diameters are specified, larger
line diameters generally improve performance
and life and reduce temperatures, particularly
in severe applications.
1. The compressor discharge line material
should be wire braided "Teflon" hose,
copper tubing or a combination of both.
2. Compressor discharge line lengths and
inside diameter requirements are
dependent on the vehicle application.
3. The dryer inlet temperature must be less
than 175°F. This can normally be
accomplished with 12' to 15' of air
compressor discharge line length.
4. Excessive line length should also be
avoided to prevent freeze-up. The dryer
inlet temperature must be greater than 40°F.
If the discharge line exceeds 15', the line
can be insulated as needed to prevent
freeze-up.
Air Connections
1. Connect a suitable line from the compressor
to the ½" NPT Inlet Port #1.
2. From the ½" NPT dryer outlet, Port #21,
use a suitable line and connect to the
supply tank.
3. Connect a ¼" nylon line or equivalent for
control line(s).
Exhaust Line
1. If it is necessary to direct PUR
est
Air Dryer
discharge contaminates away from vehicle
components, a hose can be attached to the
purge exhaust cover using the existing one
inch hose fitting.
Before placing the vehicle in service, perform
the following tests.
1. Close all reservoir drain cocks.
2. Build up system air pressure to governor
cut-out and note that the air dryer purges
with an audible exhaust of air.
3. Actuate the service brakes to reduce
system air pressure to governor cut-in.
Note that the system once again builds
to full pressure and is followed by a purge.
4. It is recommended that the vehicle be
tested for leakage using the following
procedure to assure that the air dryer will
not cycle excessively:
A. Apply the parking brakes, build system
pressure to governor cut-out and allow
pressure to stabilize for at least 1 min.
B. Observe the dash gauge pressures for
2 min. and note any pressure drop.
Pressure drop should not exceed 4 psi
with brake released and 6 psi with
brakes applied. Any noticeable
leakage must be repaired to avoid
excessive cycling.
5. Charge Cycle Time: During normal, daily
operation the compressor should recover
from governor cut-in to governor cut-out in
90 seconds or less at engine RPM's
depending on vehicle vocation.
6. Purge Cycle Time: During normal vehicle
operation, the air compressor must remain
unloaded for a minimum of 30 seconds
between charge cycles. This minimum
purge time is required to insure complete
regeneration of the desiccant.
Installing the PURest
Testing the PURest