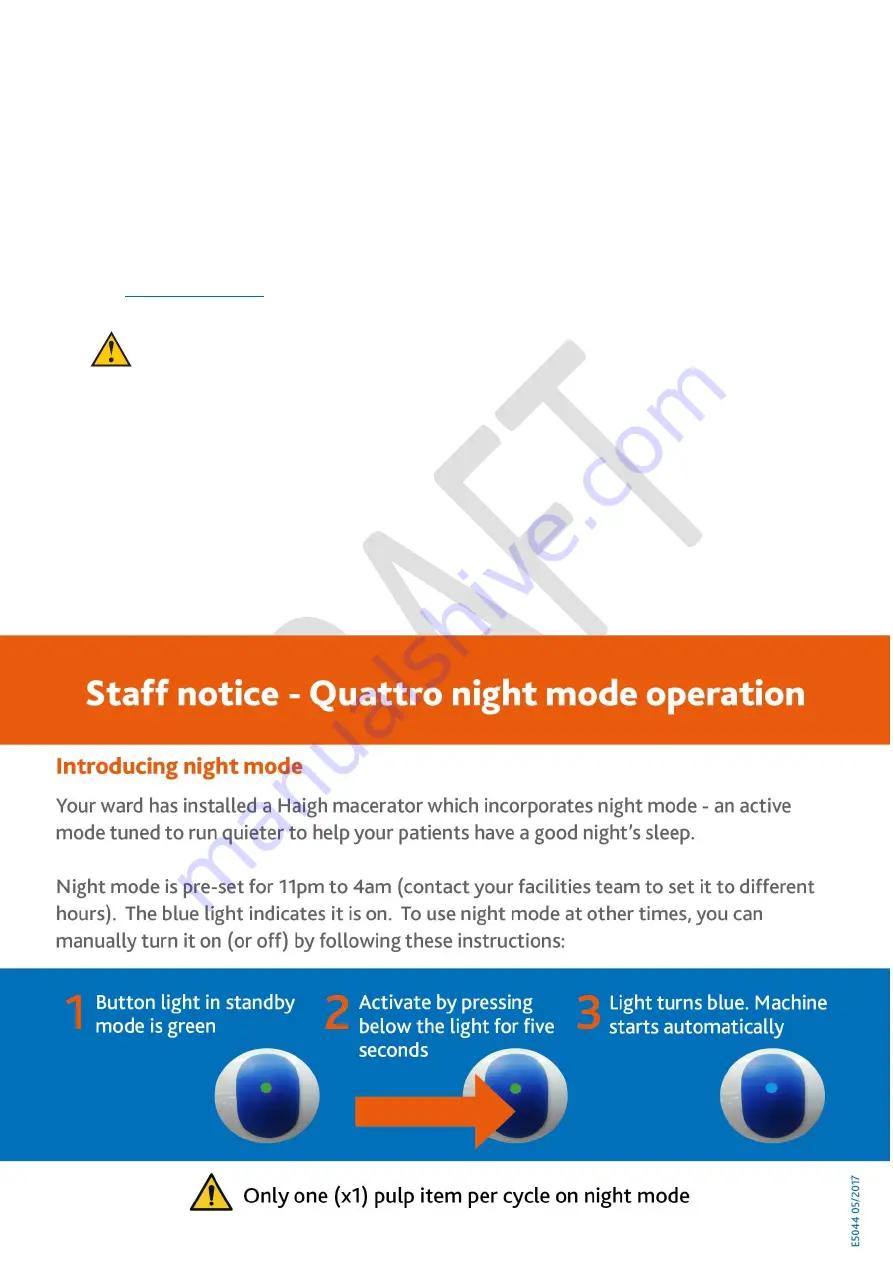
Page 19
How to use night mode
Night mode is an option available as standard on the Quattro Vanguard Solo dB.
A typical pulp macerator operates at 60
– 64dBA whereas when night mode is activated, it operates at just
52dBA Leq. This means you can continue to use macerators located in wards immediately as required.
The machine automatically switches to night mode during the hours of 11pm to 4am however the setting could
be changed to suit whatever times you think are suitable for you. Speak to your facilities/estates team if you
require this. If any further advice is required, contact one of Haigh’s technical specialists on 01989 760 230 or
email
Only 1 x pulp item can be placed in the hopper during each cycle when in night mode.
Please see cycle times for more information.
A poster for advising users how to set night mode manually will be made available in your welcome pack
(publication number E5044) or can be printed from below:
Summary of Contents for Quattro Vanguard Enhanced
Page 1: ...Page 1...
Page 2: ...Page 2...
Page 3: ...Page 3...
Page 12: ...Page 12 Technical diagram...
Page 17: ...Page 17 1...
Page 32: ...Page 32 General assembly...
Page 37: ...Page 37 Main pump removal diagram 3...
Page 38: ...Page 38 Mechanical assembly removal diagram 3 4 5 6...
Page 40: ...Page 40 Plumbing diagram...
Page 43: ...Page 43 Wiring diagram single phase 1 PHASE MOTOR 120 VOLTS 1 PHASE PUMP MOTOR 120 VOLTS...
Page 49: ...Page 49...