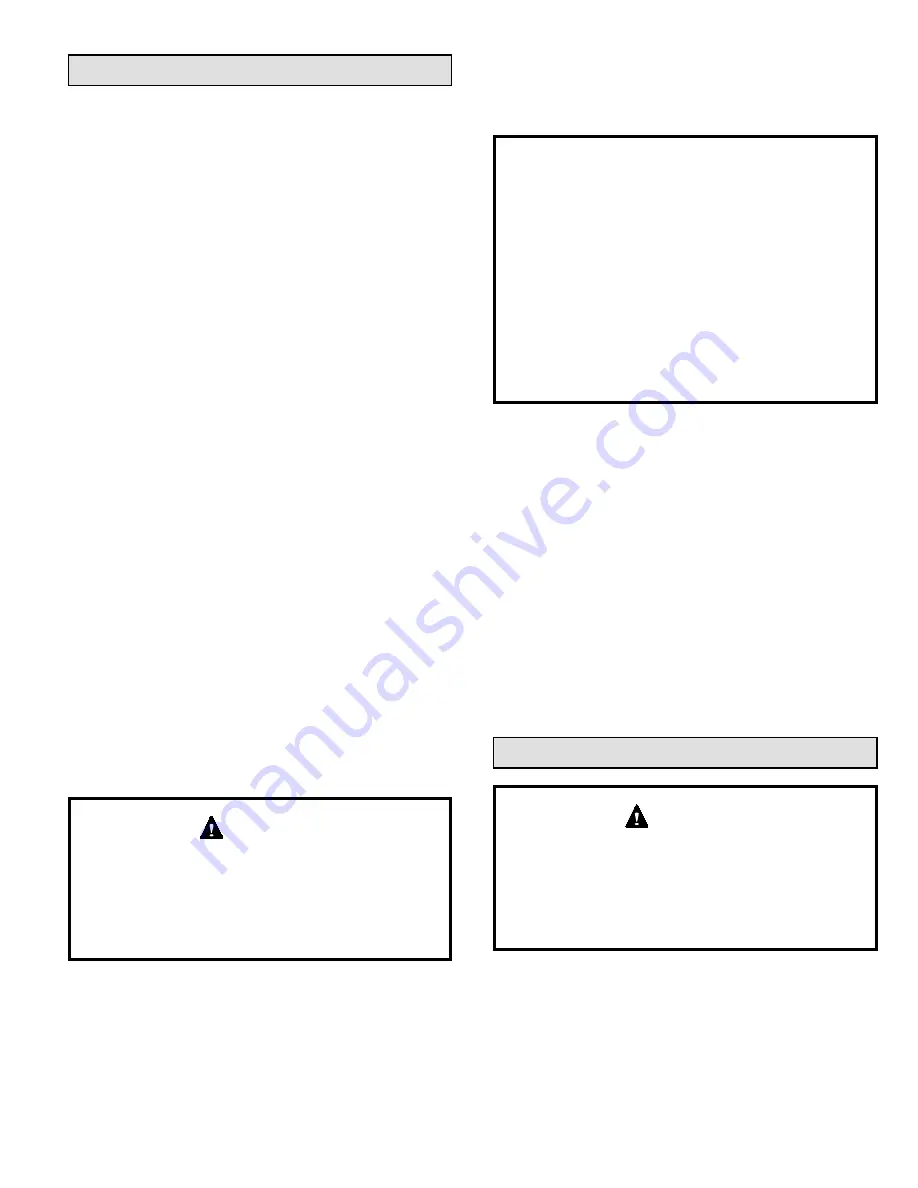
508311G01 / 31-5000754
Page 23 of 26
Issue 2250
Homeowner Information
ELECTRICAL SHOCK HAZARD!
Turn OFF electric power to unit before performing any
maintenance or removing panels or doors.
FAILURE TO DO SO COULD RESULT IN BODILY
INJURY OR DEATH.
WARNING
Heat Pump Operation
Your new heat pump has several characteristics that you
should be aware of:
• Heat pumps satisfy heating demand by delivering large
amounts of warm air into the living space. This is quite
different from gas-or oil-fired furnaces or an electric
furnace which deliver lower volumes of considerably
hotter air to heat the space.
Maintenance
Regular Maintenance Requirements
Your system should be regularly inspected by a qualified
service technician. These regular visits may include
(among other things) checks for:
• Motor operation
• Ductwork air leaks
• Coil & drain pan cleanliness (indoor & outdoor)
• Electrical component operation & wiring check
• Proper refrigerant level & refrigerant leaks
•
Proper airflow
• Drainage of condensate
•
Air filter(s) performance
• Blower wheel alignment, balance & cleaning
• Primary & secondary drain line cleanliness
• Proper defrost operation (heat pumps)
Air Filter
Inspect air filters at least monthly and replace or clean as
required. Disposable filters should be replaced. Washable
filters may be cleaned by soaking in mild detergent and
rinsing with cold water. Allow filter to dry before reinstalling.
Replace filters with the arrows pointing in the direction of
airflow. Dirty filters are the most common cause of poor
heating / cooling performance and compressor failures.
Indoor Coil
If the system has been operated with a clean filter in place,
it should require minimal cleaning. If cleaning is needed,
call your dealer for service.
Condensate Drain
During cooling season check at least monthly for free flow
of drainage and clean if necessary.
SHARP OBJECT HAZARD!
Condenser coils have sharp edges. Wear adequate
body protection on body extremities (e.g. gloves).
FAILURE TO FOLLOW THIS WARNING COULD
RESULT IN BODILY INJURY.
WARNING
Condenser Coils
Grass cuttings, leaves, dirt, dust, lint from clothes dryers,
and foliage from trees can be drawn into coils by movement
of the air. Clogged condenser coils will lower the efficiency
of your unit and could cause damage to the condenser.
Periodically, debris should be brushed from the condenser
coils. Use a soft bristle brush with light pressure only. DO
NOT damage or bend condenser coil fins. Damaged or
bent fins may affect unit operation.
This unit is equipped with an aluminum coil. Aluminum
coils may be damaged by exposure to solutions with
a pH below 5 or above 9. The aluminum coil should
be cleaned using potable water at a moderate pressure
(less than 50psi). If the coil cannot be cleaned using
water alone, it is recommended to use a coil cleaner
with a pH in the range of 5 to 9. The coil must be rinsed
thoroughly after cleaning.
In coastal areas, the coil should be cleaned with potable
water several times per year to avoid corrosive buildup
(salt).
NOTICE
Painted Surfaces
For maximum protection of the unit’s finish, a good grade
of automobile wax should be applied every year. In
geographical areas where water has a high concentration
of minerals (calcium, iron, sulfur, etc.), it is recommended
that lawn sprinklers not be allowed to spray the unit. In
such applications, the sprinklers should be directed away
from the unit. Failure to follow this precaution may result
in premature deterioration of the unit finish and metal
components.
In sea coast areas, special maintenance is required due
to the corrosive atmosphere provided by the high salt
concentration in ocean mists and the air. Periodic washing
of all exposed surfaces and coil will add life to your unit.
Please consult your installing dealer for proper procedures
in your geographic area.