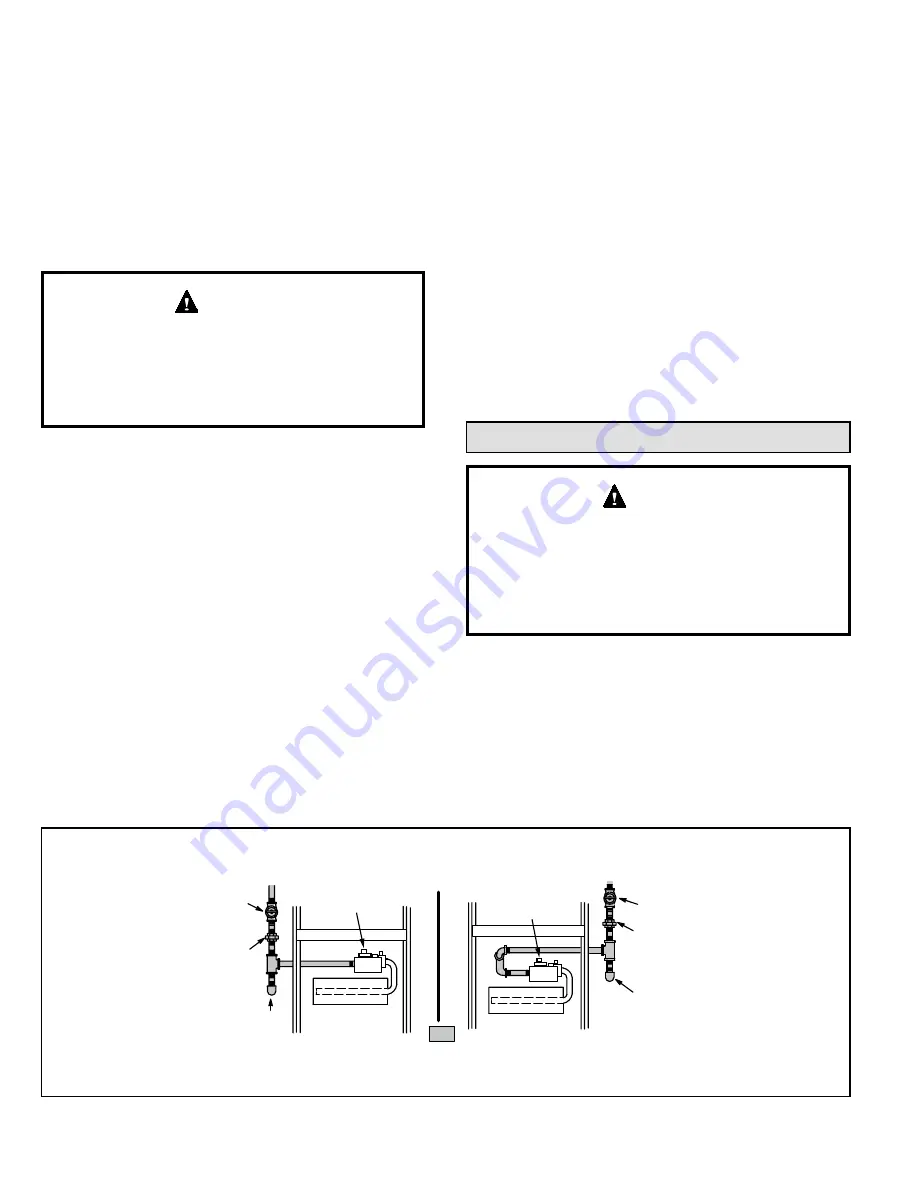
507330-03G / 31-5000662
Page 18 of 36
Issue 2209
Removal of the Furnace from Common Vent
In the event that an existing furnace is removed from
a venting system commonly run with separate gas
appliances, the venting system is likely to be too large to
properly vent the remaining attached appliances.
Conduct the following test while each appliance is operating
and the other appliances (which are not operating) remain
connected to the common venting system. If the venting
system has been installed improperly, you must correct the
system as indicated in the general venting requirements
section.
CARBON MONOXIDE POISONING HAZARD
Failure to follow the steps outlined below for each
appliance connected to the venting system being
placed into operation could result in carbon monoxide
poisoning or death.
WARNING
The following steps shall be followed for each appliance
connected to the venting system being placed into
operation, while all other appliances connected to the
venting system are not in operation:
1. Seal any unused openings in the common venting
system.
2.
Inspect the venting system for proper size and
horizontal pitch. Determine that there is no blockage,
restriction, leakage, corrosion, or other deficiencies
which could cause an unsafe condition.
3. Close all building doors and windows and all doors
between the space in which the appliances remaining
connected to the common venting system are located
and other spaces of the building. Turn on clothes
dryers and any appliances not connected to the
common venting system. Turn on any exhaust fans,
such as range hoods and bathroom exhausts, so they
will operate at maximum speed. Do not operate a
summer exhaust fan. Close fireplace dampers.
4. Follow the lighting instructions. Turn on the appliance
that is being inspected. Adjust the thermostat so that
the appliance operates continuously.
5. After the burners have operated for 5 minutes, test for
leaks of flue gases at the draft hood relief opening.
Use the flame of a match or candle.
6. After determining that each appliance connected to
the common venting system is venting properly, (step
3) return all doors, windows, exhaust fans, fireplace
dampers, and any other gas burning appliances to
their previous mode of operation.
7. If a venting problem is found during any of the
preceding tests, the common venting system must be
modified to correct the problem.
Resize the common venting system to the minimum vent
pipe size determined by using the appropriate tables in
Appendix G. (These are in the current standards of the
National Fuel Gas Code ANSI 2223.1.
Gas Piping
If a flexible gas connector is required or allowed by
the authority that has jurisdiction, black iron pipe shall
be installed at the gas valve and extend outside the
furnace cabinet. The flexible connector can then be
added between the black iron pipe and the gas supply
line.
CAUTION
Gas Supply
1. This unit is shipped standard for left or right side
installation of gas piping (or top entry in horizontal
applications). Connect the gas supply to the piping
assembly.
2. When connecting the gas supply piping, consider
factors such as length of run, number of fittings, and
furnace rating to avoid excessive pressure drop. Table
6 lists recommended pipe sizes for typical applications.
FIELD
PROVIDED
AND INSTALLED
Left Side Piping
(Standard)
Right Side Piping
(Alternate)
GROUND
JOINT
UNION
DRIP LEG
MANUAL
MAIN SHUT-OFF
VALVE
AUTOMATIC
GAS VALVE
(with manual
shut-off valve)
GROUND
JOINT
UNION
DRIP LEG
MANUAL
MAIN SHUT-OFF
VALVE
AUTOMATIC
GAS VALVE
(with manual
shut-off valve)
NOTE:
BLACK IRON PIPE
ONLY
TO BE ROUTED INSIDE OF CABINET
Figure 25.
Possible Gas Piping Configurations - Upflow Applications