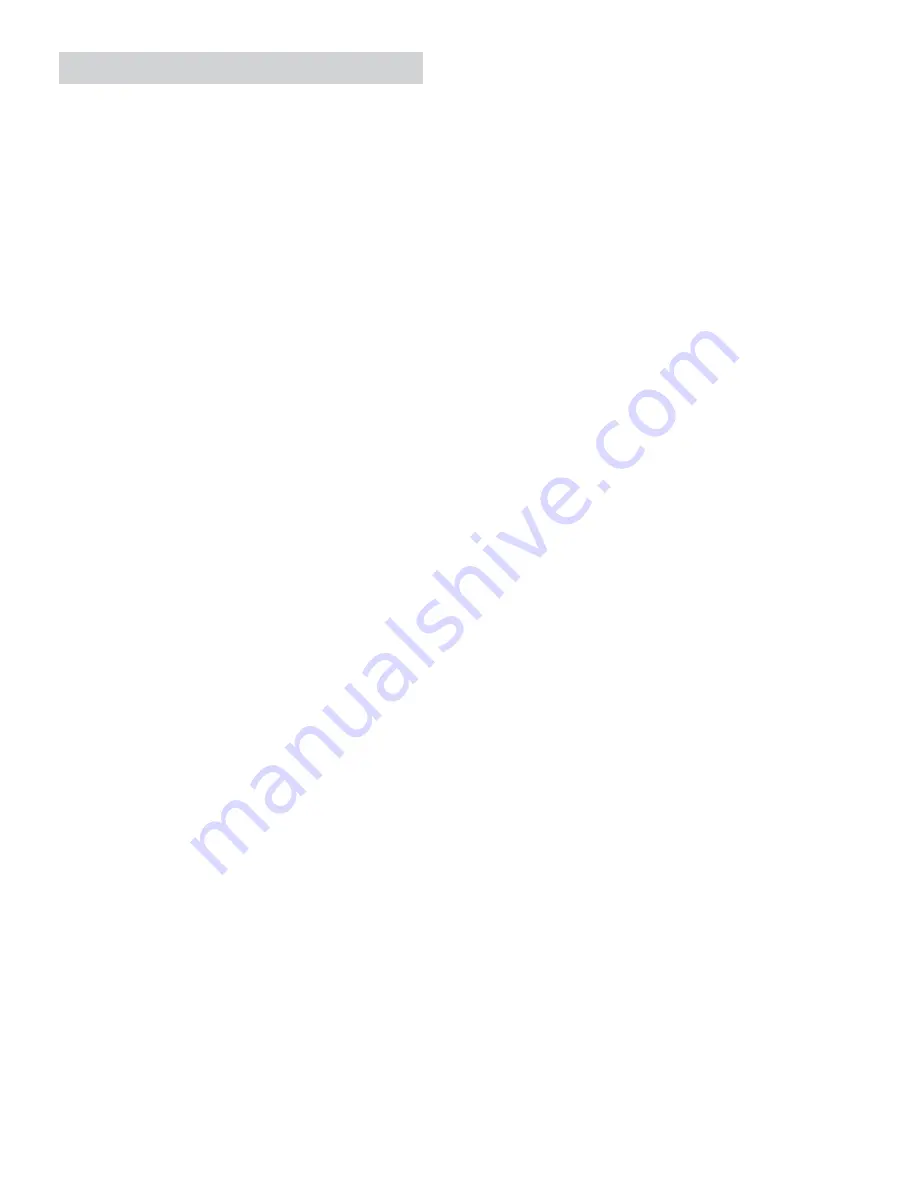
– 56 –
Clear
Door Diagnostic Tool
The Clear Door (
Part #
: WX05X20002) provides
technicians with a tool to accurately diagnose
2012 and newer dishwashers. Viewing the
wash zones not only allows more accuracy, it
will reduce diagnostic time, reduce repeat calls
and will increase technician confidence. There
may also be situations where the clear door can
be used to show a consumer the dishwasher is
operating properly.
Poor wash results can be due to many different
things. The clear door allows operation and
visibility of spray arms including rotation, slow or
non-rotation, leaks between wash components,
restrictions and spray jet pattern.
Proper spray arm speeds have a tolerance of
+/- 5 RPM. The lower spray arm turns clockwise
(CW) at approximately 50 RPM. The mid spray
arm turns approximately 30 RPM counter-
clockwise (CCW). The upper sprayer cannot be
counted but can be viewed for proper operation.
To Use WX05X20002 Clear Door
1.
Place the dishwasher in service mode to fill,
circulate and drain. Details on Consumer
Error Mode and Service Mode can be found
in dishwasher mini manuals and this service
guide. All models have the same entry
directions. Different controls have different
ways to communicate results and progress.
2. Remove the bottom rack for an unobstructed
view of the lower spray arm.
3. Enter Consumer Error Mode.
4. Enter Service Mode.
5. Open the dishwasher door all the way to 90
degrees.
6. Place the WX05X20002 Clear Door into the
tub opening starting at the bottom.
WARNING
: To prevent any damage, do not close
the dishwasher door when the clear door is in
use.
7. The clear door has a latch strike. When
pushed into the latched position, it will
activate the door switch assembly. The
dishwasher may not start if the clear door is
installed to low.
8.
Initiate Fill; the dishwasher will fill for 60
seconds.
9. Initiate the circulate test to view the circulation
system in action.
10. Service mode will initiate a 2-minute circulate
test 30 seconds lower clockwise (CW), 2 to 3
seconds lower counter-clockwise (CCW) (will
not reach full speed unless dishwasher is in
a main wash cycle) and 30 seconds upper
spray system. This pattern will repeat.
11.
Use a flashlight for better visibility. Look
for leaks in all areas including between the
conduits and wash components.
12. Determine potential areas for further
inspection and diagnoses.
13. Initiate drain; the dishwasher will drain for
approximately 70 seconds.
14. Remove the WX05X20002 Clear Door.
15. Proceed with any inspections, diagnoses and
repairs as detailed in the
No Circulation and
Drain
flow chart. Some components may
cause different symptoms depending on the
severity of part failure.
Diagnostics