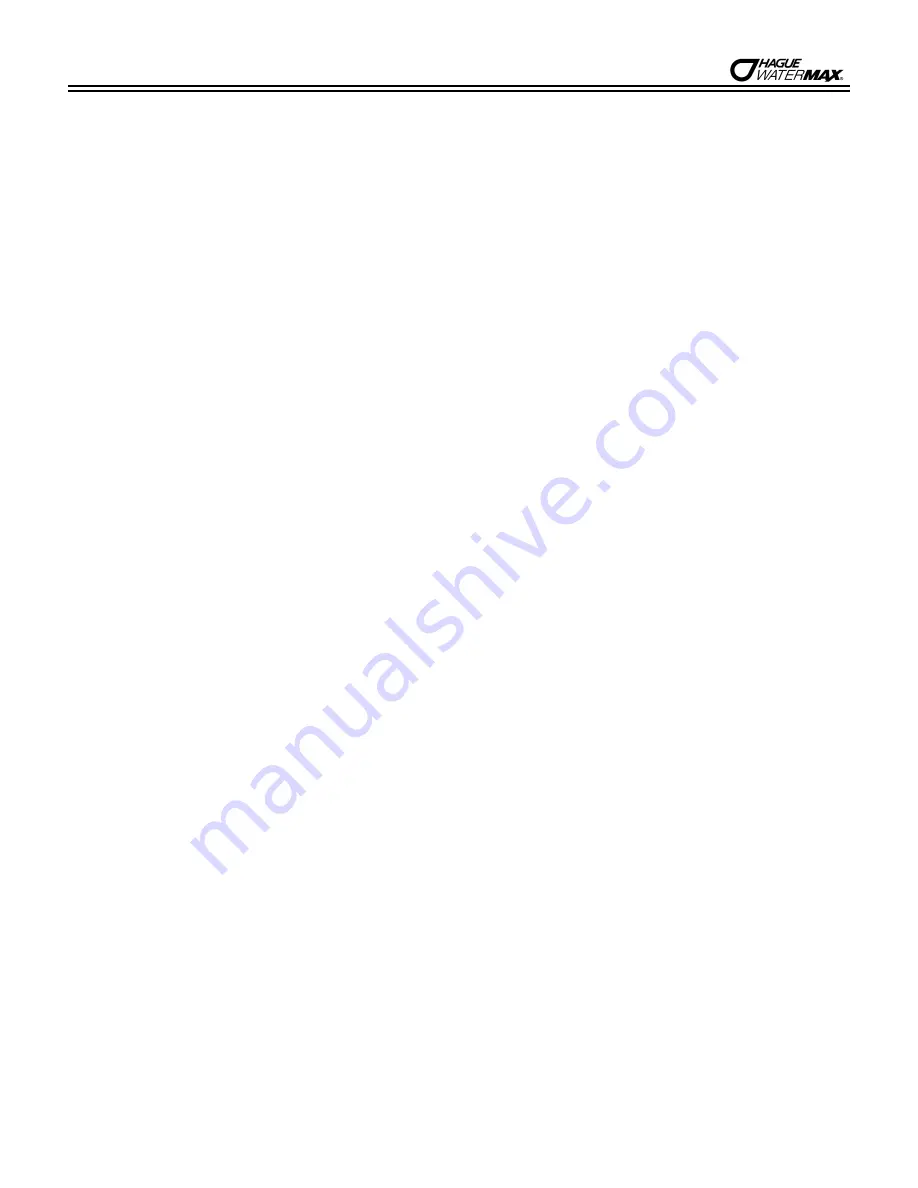
10 Series Owner’s Manual
90246 Bypass Housing
: Makes the connection between
the plumbing and Main Valve Body. Also, contains the
“Hard Water” Blending Valve and Bypass Piston. The
recommended seal for the 1 ¼" male inlet-outlet threads
is the plastic Hook-up Nut (90251), Gasket (90837), and
Copper Adapter (90254). Make sure the Gasket is
between the Housing and Copper Adapter. The O-ring
seal areas at the Main Valve Body inlet and outlet must
be smooth and free of defects and debris, and lubricated
with silicone grease before assembling. When attaching
to the Main Valve Body, put the O-rings on the male
bosses on the Valve Body and push the Bypass into
place; if not, the O-rings may be “pinched”. If the O-
rings are pinched, replace with new ones. The Bypass is
pre-assembled with the Sensor housing and turbine axle.
These are not field serviceable and if damaged, must be
replaced with a new assembly. The Bypass Piston bore
is to be smooth and, at the recessed areas, have a smooth
transition (no sharp corners) to the seat areas.
90262 Bypass End Cap – Left
: Seals the left Piston
opening on the Housing (90246). The opening is sealed
with an O-ring used as an axial or “face” seal. The O-
ring sits in a groove in the End Cap. This groove must
be free of defects such as pits or scratches and also free
of debris. When assembling the End Cap to the
Housing, care should be taken to make sure that the O-
ring stays in the groove in the End Cap. If misaligned,
the O-ring can become pinched and leak. Also, on the
End Cap is the Piston Axle, a ¼" square shaft that acts as
a guide / slide and anti-turning mechanism for the
Bypass Piston.
90263 Bypass End Cap – Right
: Seals the right Piston
opening on the Housing (90246). The opening is sealed
with an O-ring used as an axial or “face” seal. The O-
ring sits in a groove in the End Cap. This groove must
be free of defects such as pits or scratches and also free
of debris. When assembling the End Cap to the
Housing, care should be taken to make sure that the O-
ring stays in the groove in the End Cap. If misaligned,
the O-ring can become pinched and leak. Also, on the
End Cap is the guide / bushing for the Bypass Piston
Drive Shaft. There is an O-ring seal at the opening for
the Drive Shaft. This seal area must be free of defects
such as pits or scratches and also free of debris.
90218 Bypass Piston Drive Shaft
: The Drive Shaft has
an acme thread which is used to move the Piston from
“bypass” to “service” position. When operating the
Bypass, to achieve either “service” or “bypass”, it is only
necessary to turn the Handle (90221) until the Piston
(90616) stops. Additional pressure (torque) will not
improve the seal. As a matter-of-fact, once the Piston
reaches the stop at either position, it can be backed off
up to one half turn of the handle and still achieve a seal.
90616 Bypass Piston Assembly
: The white Teflon
Hydro-slide o-ring covers should be free of defects such
as indentations and cuts. The Piston should move freely
into and out of the Bypass Housing without damaging
the Hydro-slides. If the Hydro-slides catch, tear or
crimp, the Housing should be replaced. Note: Some
compression will occur when the Hydro-slides pass
through the seal areas.
93858 Turbine Sensor Assembly
: Picks up the
magnetic field from the Turbine and relays it to the
Controller. The three wire assembly connecting the
“black wafer” Hall Effect Sensor to the Controller board
must not be severely bent (folded over,) cut, or broken.
Care should be taken when putting the Sensor into the
Sensor Housing. The “spring” flap below the Sensor
must be gently bent over (on top of) the Sensor, and then
the Sensor slides all the way into the Sensor Housing.
The round hole of the Sensor mounting tab is then
placed down over the mounting screw boss. The cap is
then put in place and the mounting screw is installed. A
slot is provided in the cap for the wire way to exit. The
three-wire socket connector must be properly installed in
the controller. Stops on the connector prevent improper
(upside down) assembly. Do not force the connector
past the stops.
90522 Turbine Assembly
: The turbine must have a
1/8" diameter Rare Earth magnet pressed into place
adjacent to the axle opening. When assembled to the
axle, the Turbine should spin freely. Do not use any
lubricants. If the Turbine should become “jammed”,
clean and flush the Turbine and Bypass Valve.
90252 Blending Dial Cap
: The Cap should be held in
place by the three ½" screws and be in the proper
orientation.
90222 Blending Valve
: The dial permits the addition of
“hard water” into the soft water outlet. It is closed when
pointing toward the Main Valve Body and open when
pointing toward the inlet side.
90226 Test Port Valve
: The Test Port Valve is used to
draw water samples for testing of treated water. Note:
The Bypass must be in the “service” position to get an
accurate sample. There are two types of seals on the
Test Port. One seal is an O-ring which seals off the
threaded area when the Valve is opened. The other seal
is a compression seal between the Test Port Valve
material and the Right End Cap material. If this seal is
“overtightened”, it can damage the sealing area on the
End Cap causing a permanent leak.
Summary of Contents for Watermax 10 Series
Page 1: ...10 Series Owner s Manual...
Page 37: ...10 Series Owner s Manual 35 NOTES...
Page 38: ...NOTES...