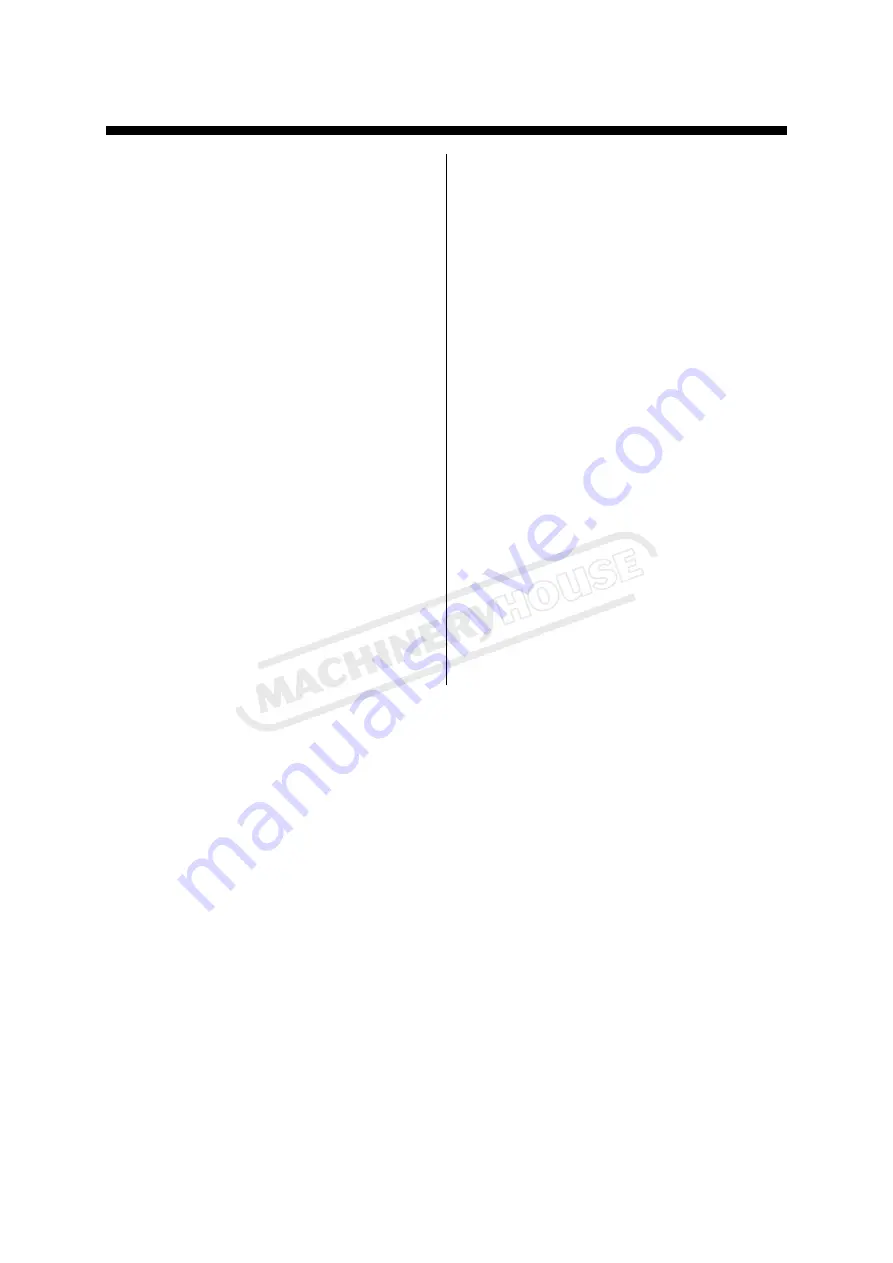
Table of Contents
1 SAFETY REGULATIONS ........................ 2
1.1 General Safety Advice ...................... 2
1.2 Blade Guard Safety ........................... 2
1.3 Emergencies ..................................... 2
2 MACHINE DIMENSIONS ........................ 2
3 TECHNICAL CHARACTERISTICS ......... 3
3.1 General Characteristics..................... 3
4 TRANSPORTING THE MACHINE .......... 3
5 GETTING TO KNOW YOUR MACHINE . 3
5.1 Disk Head Assembly ......................... 3
5.2 Machine Base ................................... 4
5.3 Vice ................................................... 4
5.4 Support Roller ................................... 4
5.5 Stand ................................................. 4
5.6 Coolant Pump ................................... 4
6 GETTING STARTED ............................... 5
6.1 Minimum Requirements for Housing
the Machine ............................................ 5
6.2 Anchoring the Machine ..................... 5
6.3 Assembly and Setup ......................... 5
6.4 Electrical Connection of the Machine 8
7 RECOMMENDATIONS AND ADVICE .... 8
7.1 General Advise Before Using the
Machine .................................................. 8
7.2 Operator Position .............................. 8
7.3 Deactivating the Machine .................. 9
7.4 Dismantling ....................................... 9
8 ADJUSTING THE MACHINE ................ 10
8.1 Disk Head ....................................... 10
8.2 Adjusting the Mitering Lock Lever ... 10
8.3 Changing the Disk ........................... 10
8.4 Cleaning and Accessing the Coolant
System .................................................. 10
8.5 Troubleshooting the inverter ........... 11
8.6 Common Problems and Solutions .. 11
9 THE OPERATION CYCLE .................... 14
9.1 Miter Angle ...................................... 14
9.2 Vise Operation ................................ 14
9.3 Loading the Work-piece .................. 15
9.4 Setting Cutting Length .................... 15
9.5 Operation Cycle .............................. 15
10 ROUTINE AND SPECIAL
MAINTENANCE ....................................... 16
10.1 Daily Maintenance ........................ 16
10.2 Weekly Maintenance ..................... 16
10.3 Monthly Maintenance .................... 17
10.4 Six-Monthly Maintenance .............. 17
10.5 Oils for Lubricating Coolant ........... 17
10.6 Oil Disposal ................................... 17
10.7 Special Maintenance ..................... 17
11 TROUBLESHOOTION ........................ 18
11.1 Blade and cut diagnosis ................ 18
12 WIRING DIARAM AND PARTS LIST . 21
12.1 WIRING DIARAM .......................... 21
12.2 PARTS LIST ................................. 22
Page 2
Instruction Manual for CS-350V (S830)
03/12/2014
Summary of Contents for MetalMaster CS-350V
Page 13: ...Page 13 Instruction Manual for CS 350V S830 03 12 2014 ...
Page 14: ...Page 14 Instruction Manual for CS 350V S830 03 12 2014 ...
Page 22: ...Page 22 Instruction Manual for CS 350V S830 03 12 2014 ...
Page 24: ...12 3 Explosion draw Page 24 Instruction Manual for CS 350V S830 03 12 2014 ...
Page 27: ...12 6 Explosion draw Page 27 Instruction Manual for CS 350V S830 03 12 2014 ...