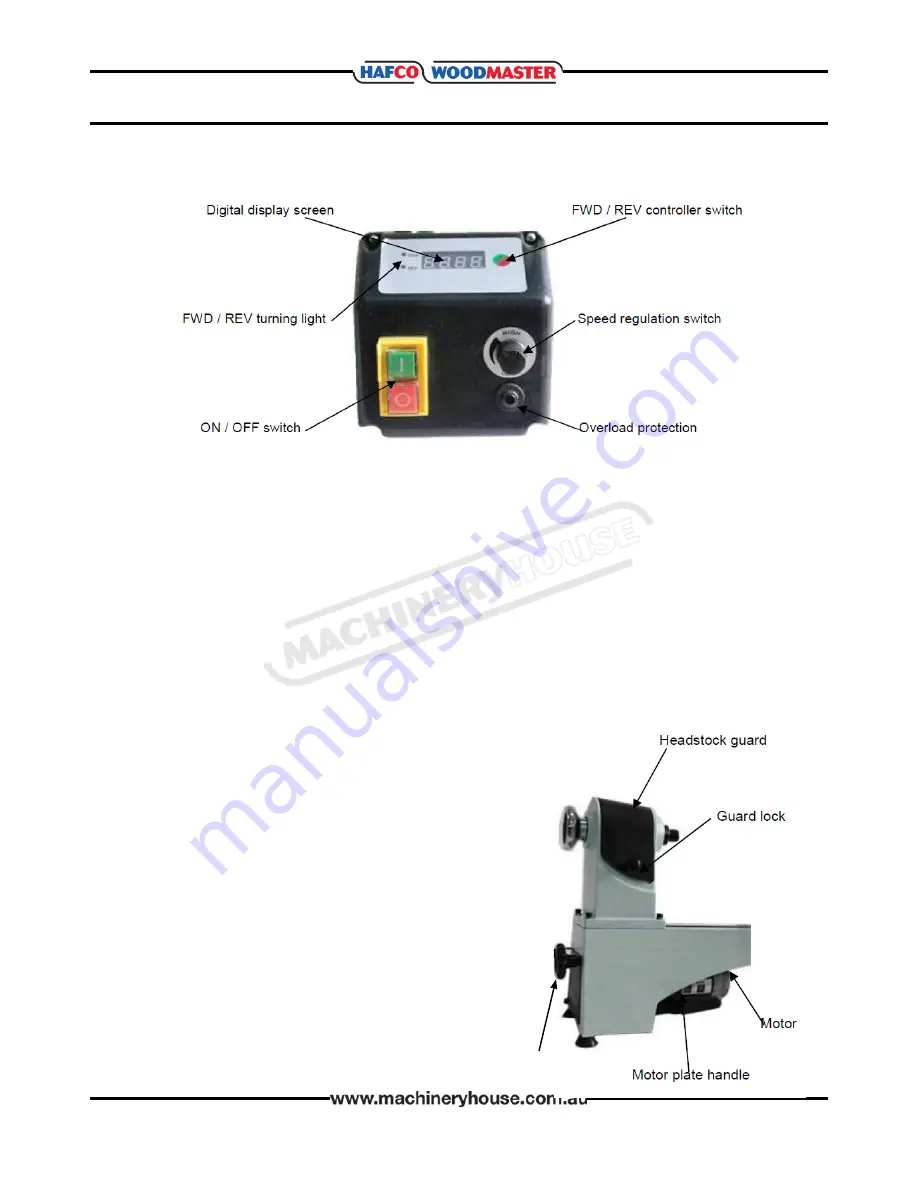
11
OPERATION MANUAL
The speed range is achieved with a Variable Speed Controller. A micro-processor chip, in
conjunction with other electronic components, allows the input power to be manipulated. In
return, smooth Variable DC power can be delivered from the controller to the motor.
Changing Speeds:
1. When starting, set the Variable Speed Knob to about ¼ of the speed range and slowly
increase the speed to the desired RPM.
2. Starting the motor at the lowest possible setting may cause it to fail due to loading.
However, the lowest setting can be achieved by reducing the RPM once the motor is in
motion.
3. Rapid RPM changes from low up to high speed are not recommended.
Changing Belt Positions:
1. To change the belt position, ensure the machine is
switched “Off” and unplugged.
2. Unlock the headstock guard by the guard lock. Then
lift the front of the guard upward.
3. Free the motor by loosening the motor lock handle.
4. Lift the motor plate handle slightly to get the belt off
of the pulley. The motor adjustment range is 20mm.
5. Install the belt on the desired step, top and bottom.
6. Tension the belt by pressing down on the motor
mount handle. Slightly higher pressure may be
required for larger work.
Caution:
Too much pressure on the motor pulley could
damage the motor bearings, or break the belt.
7. When the correct tension has been made and while
holding the motor at the correct tension, tighten the
motor lock handle.
OPERATING INSTRUCTIONS Cont.
Motor lock
handle
Page 12
Instructions Manual for WL-14V (W385)
11/08/2017