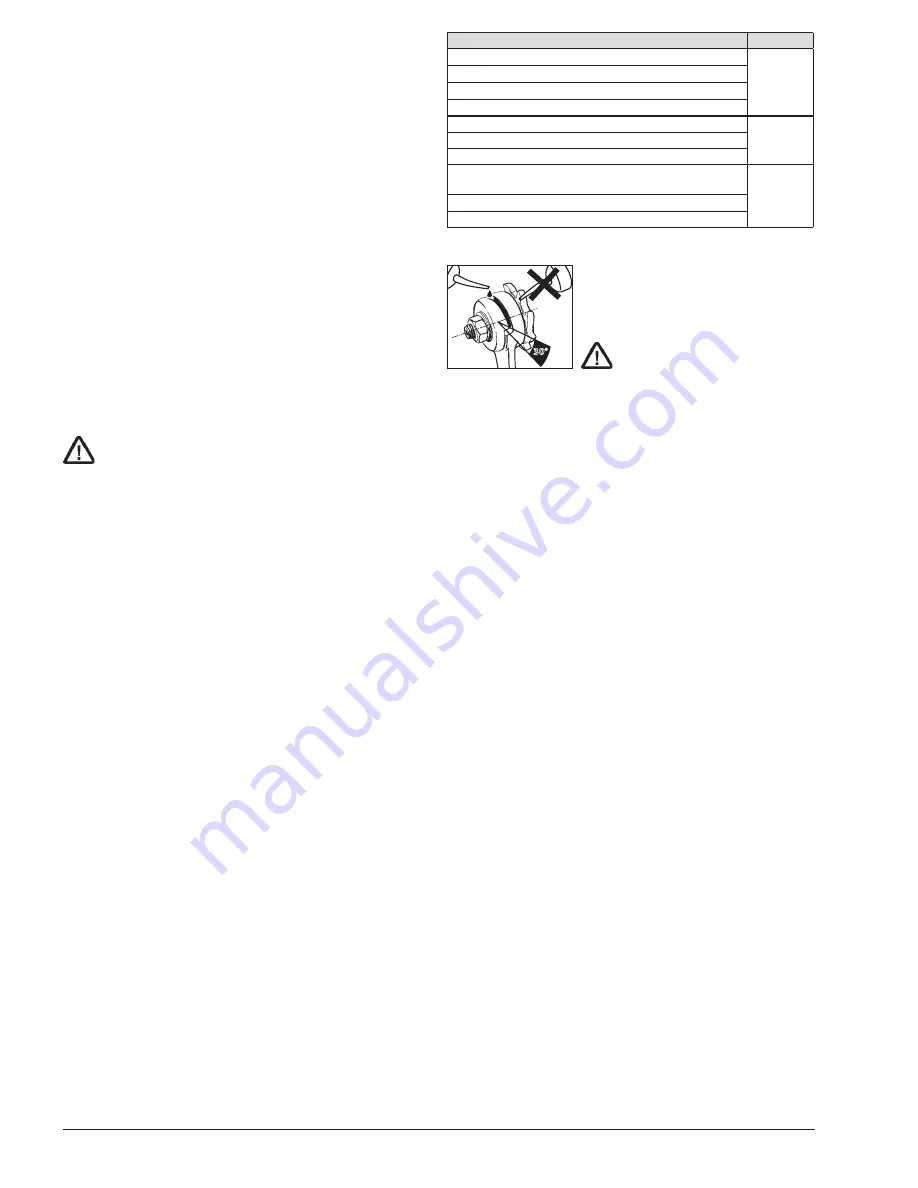
2
8. INSPECTION
The equipment must be inspected in accordance with the conditions of
use and the operating conditions at least once per year by an authorised
person 2 per TRBS 1203 (Technical expert) (testing per BetrSichV, §10,
sect.2 represents implementation of EC Directives 89/391/EEC and
95/63/EC and the annual occupational safety inspection per BGV D8,
§23, sect. 2 and BGG956). These inspections must be documented:
– Before commissioning.
– After significant alterations before recommissioning.
– At least once per year.
– In the event of unusual occurrences arising that could have detrimen-
tal effects on the safety of the winch (extraordinary tests, e.g. after a
long period of inactivity, accidents, natural events).
– After repair works that could have an influence on the safety of the
winch.
Technical experts (AP2) are persons, who have sufficient knowledge
based on their specialist training and experience, in the areas of
winches, lift and pull systems and the relevant official occupational
health and safety rules, accident prevention regulations, guidelines and
generally accepted engineering rules (e.g. EN standards), to evaluate
the operational safety of winches, and lift and pull systems. Technical
experts (AP2) are to be nominated by the operator of the equipment.
Performance of the annual occupational safety inspection as well as the
training required to obtain the aforementioned knowledge and skills can
be provided by haacon hebetechnik.
9. MAINTENANCE RECOMMENDATION
The operator determines the intervals themselves based on frequency
of use and the operating conditions.
– Regular cleaning, no steam jets!
– Carry out visual check on inaccessible brakes / locks every 5 years at
the latest, replace brake pads as required.
– General overhaul by the manufacturer after 10 years at the latest.
CAUTION!
Only perform inspection, maintenance and repair work on an
unloaded hoist. Only allow work on brakes and locks to be per-
formed by qualified specialist personnel.
Maintenance and inspection work
Intervals
Visual check of the rope hooks (load carrier)
Before
every use
Function of the winch
Condition of the rope and lifting equipment
Brake function under load
Grease bearing of drive pinion
Quarterly
Annually
Check rope for wear acc. to DIN ISO 4309 and service
Check fastening bolts for secure seating
Check all parts of the winch and crank for wear, if ap-
plicable, replace defective parts and lubricate.
Annually
Check type plate for legibility
Have an inspection performed by an expert
Lubricant recommendations:
Multi-purpose grease per DIN 51502 K3K-20
Safety crank
1- 3
30°
max
If sluggishness occurs during lowering, pour
a few drops of oil into the gap in the crank
cam.
Safety cranks with a gap aperture >30°
should be replaced. Repair must be carried
out by only by the manufacturer.
CAUTION!
Only disassemble the crank, ratchet
brace and locking pawl when the
equipment is not under load!
Do not oil or grease the brake pads!
10. SPARE PARTS
When ordering spare parts it is essential to quote:
– The type and serial number of the equipment / item and part number
11. DISASSEMBLY, DISPOSAL
– Make sure to observe the safety instructions.
– Dispose of the equipment and the substances within it in an environ-
mentally responsible manner.
Louis Reyners BV
|
Symon Spiersweg 13a, 1506 RZ Zaandam
|
+
31 (0) 75 650 47 50
|
|
www.LR.nl