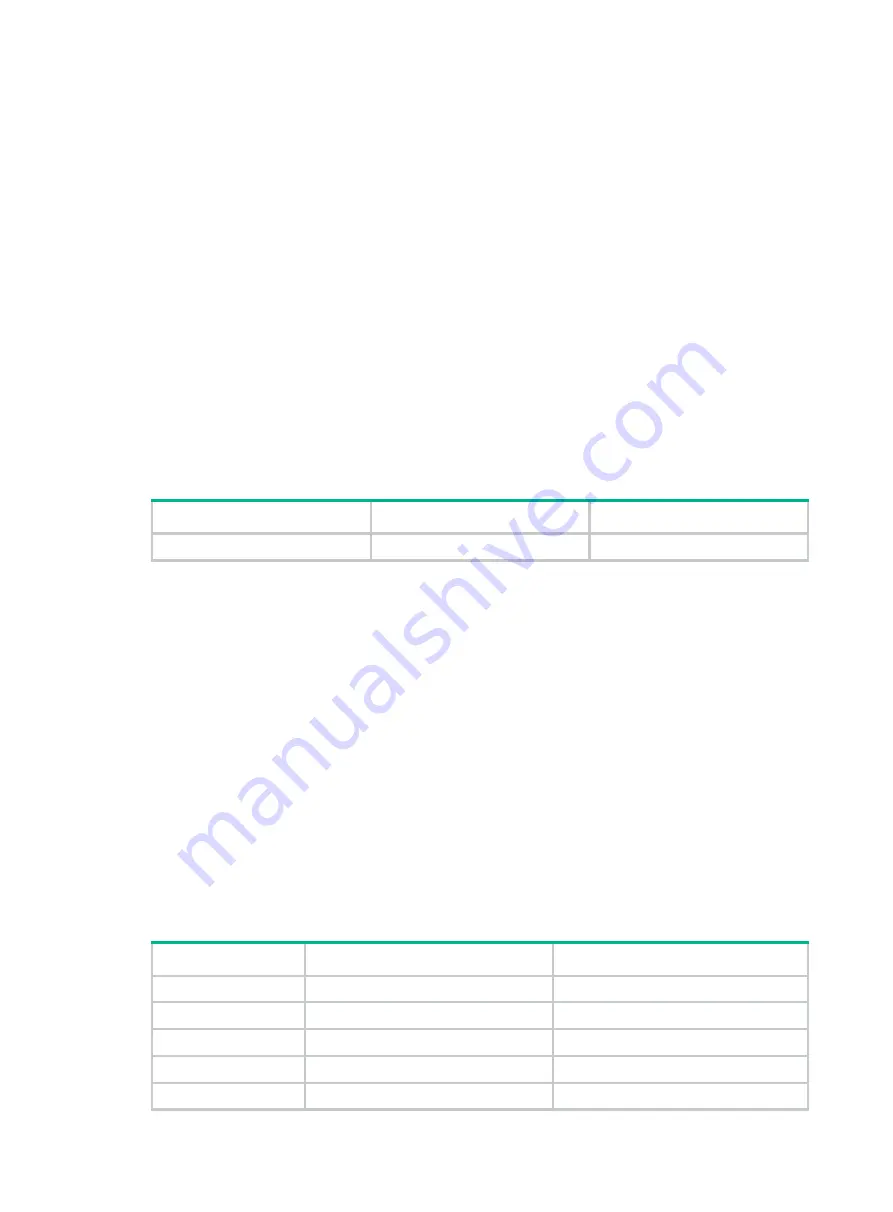
1-2
Temperature/humidity
Maintain appropriate temperature and humidity in the equipment room.
•
Lasting high relative humidity can cause poor insulation, electricity leakage, mechanical
property change of materials, and metal corrosion.
•
Lasting low relative humidity can cause washer contraction and ESD and cause problems
including loose screws and circuit failure.
•
High temperature can accelerate the aging of insulation materials and significantly lower the
reliability and lifespan of the switch.
For the temperature and humidity requirements of different switch models, see
H3C S6116
Ultra-Low Latency Switch Series Hardware Information and Specifications
.
Cleanliness
Dust buildup on the chassis might cause electrostatic adsorption and dust corrosion, resulting in
poor contact of metal connectors and contact points. This might shorten the device's lifetime and
even cause device failure in the worst case.
describes the switch requirement for
cleanliness.
Table1-2 Switch requirement for cleanliness
Substance
Particle diameter
Concentration limit
Dust particles
≥ 0.5 µm
≤ 1.8 × 10
7
particles/m
3
To maintain cleanliness in the equipment room, follow these guidelines:
•
Keep the equipment room away from pollution sources. Do not smoke, eat, or drink in the
equipment room.
•
Use double-layer glass in windows and seal doors and windows with dust-proof rubber strips.
Use screen doors and window screens for doors and windows open to the outside and make
sure the external windows are air tight.
•
Use dustproof materials for floors, walls, and ceilings and use wallpaper or matt paint that does
not produce powders.
•
Clean the equipment room regularly and clean the air filters of the rack each month.
•
Wear ESD clothing and shoe covers before entering the equipment room, keep the ESD
clothing and shoe covers clean, and change them frequently.
Corrosive gas limit
Corrosive gases can accelerate corrosion and aging of metal components. Make sure the corrosive
gases do not exceed the concentration limits as shown in
Table1-3 Corrosive gas concentration limits
Gas
Average concentration (mg/m
3
)
Maximum concentration (mg/m
3
)
SO
2
0.3
1.0
H
2
S
0.1
0.5
Cl
2
0.1
0.3
HCI
0.1
0.5
HF
0.01
0.03