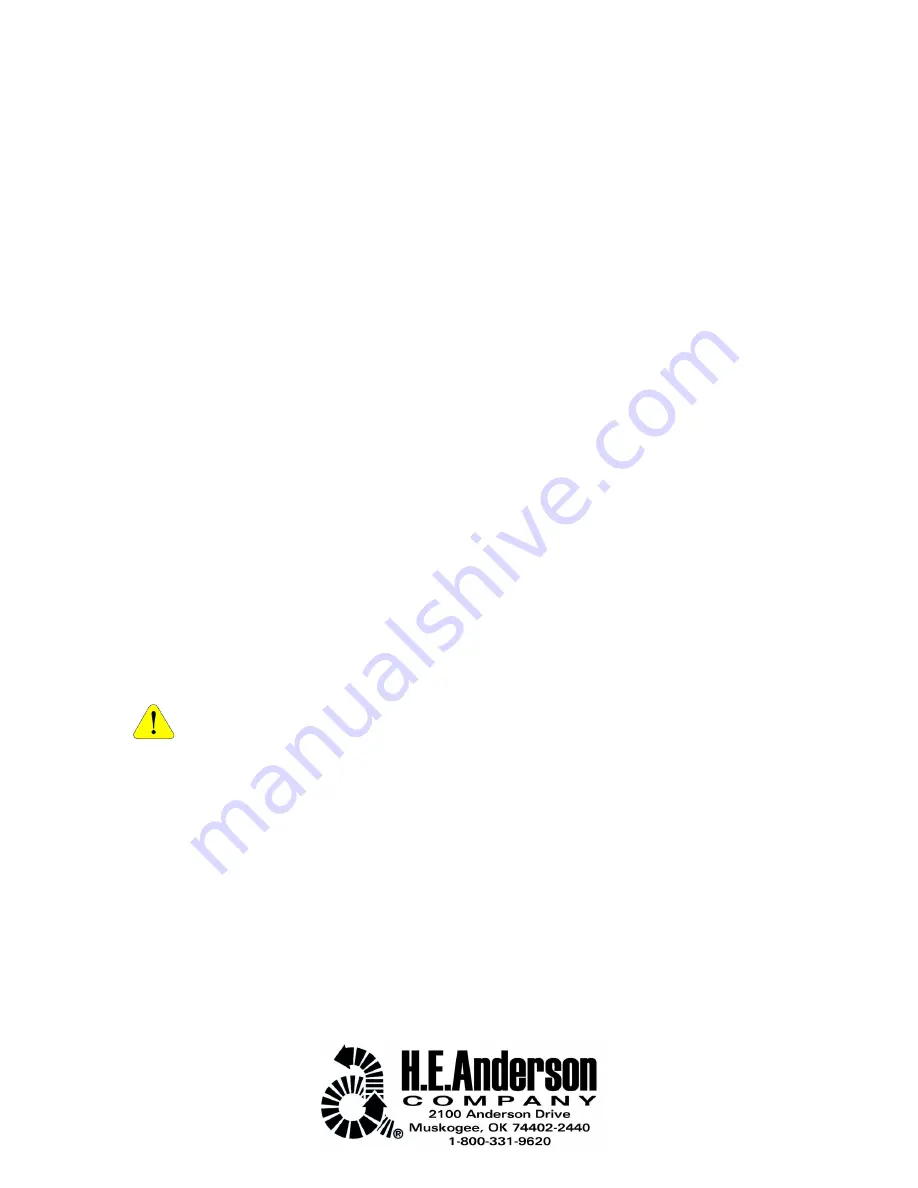
number listed in the front of this manual.
Checking the Meter Sensor
You have probably already observed the red LED indicators mounted on the sensor circuit board which is
housed in the clear housing atop the water meter. Checking these can quickly pinpoint some problems.
•
The power LED will be lit whenever power to the controller is on and properly functioning (it displays and
responds to key presses). If not lit, there is a problem with the sensor board or, more likely, with the
cable between meter and controller.
•
The second LED should light with each pulse from the sensor. It should be blinking whenever water is
flowing. If this is not happening, refer to the instructions for your meter for more information.
Pumper and Diaphragm Problems
See your pumper manual(s) for information on servicing your pumpers.
Requirements for Proper Operation
•
Minimum line pressure of 30 psig, measured on the downstream side of the injector. If you do not have a
pressure reading of 30 pounds at the pressure gauge on top of the unit, then you do not have enough
pressure. If the water is flowing out to an open tank or onto the ground, there will probably not be
sufficient back pressure to meet the 30 psig requirement even if there is much greater pressure (e.g. 50
psig) on the inlet. This is the most common cause of erratic operation. In this situation you should install
a valve and pressure gauge downstream from the unit. Close the valve until the gauge reads 30 psi or
greater.
•
The flow rate should be within the range of your flow meter. (See Table 1 in your meter manual for flow
range information).
•
The pumpers should not exceed 35 strokes per minute. Running the injector system faster than 35
strokes per minute can result in premature failure of pumpers. Pumpers also might not have enough
time to completely fill with solution between strokes causing incorrect injection rates.
•
The manifold discharge line and any tubing attached must open to “daylight” and go directly to a drain.
Do not obstruct or elevate the line at any point. If a long line is needed, it should be expanded to a larger
size. Put an air vent or gap between the primary and the extended line.
•
Too much chemical feed is usually not caused by a malfunction. It is usually due to siphoning or gravity
flow of chemical through the feeder during periods of zero pressure on the system. The system shutoff
valve should be downstream of the system to maintain pressure at all times and the chemical level in
storage tanks should not be above the injection point fitting.
•
Do not store chemicals in tanks where the level will be more than just a few feet above the
discharge point of the pumpers. If you have very large solution storage tanks you should use
them to fill smaller “day tanks”. This will eliminate the chance of large quantities of chemicals
draining into your watering system.
8