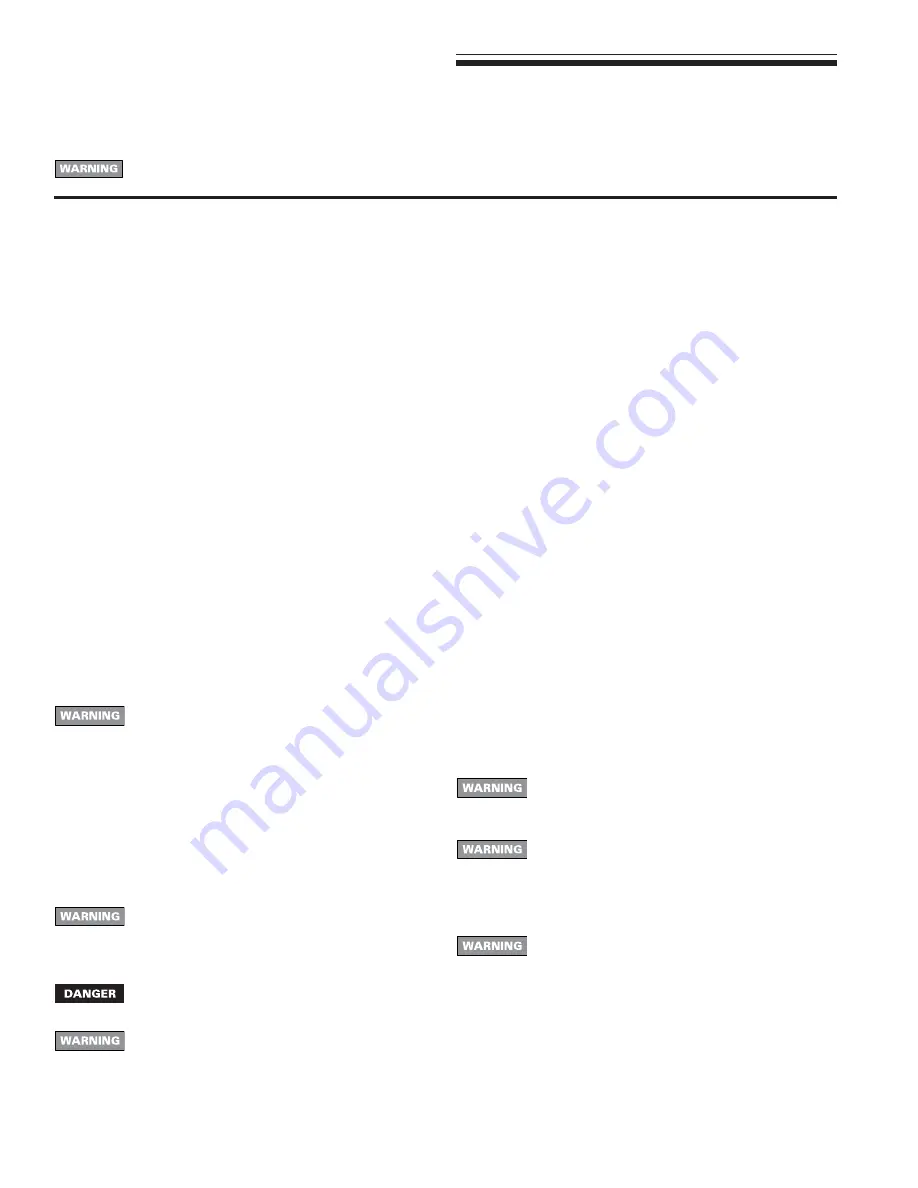
GWS
Gas-Fired Water Boilers –
Boiler Manual
22
Part Number 550-110-732/0703
11 Service and maintenance
continued
❏
❏
❏
❏
❏
Inspect . . . . . . . . . .
Reported problems
Inspect any problems reported by owner and correct before
proceeding.
Boiler area
1. Verify that boiler area is free of any combustible materials,
gasoline and other flammable vapors and liquids.
2. Verify that boiler area (and air intake) is free of any of the
contaminants listed in Table 3 on page 5 of this manual. If any of
these are present in the boiler intake air vicinity, they must be
removed. If they cannot be removed, install combustion air piping
to the boiler in accordance with national, provincial or local
codes.
Air openings
1. Verify that combustion and ventilation air openings to the boiler
room and/or building are open and unobstructed. Check
operation and wiring of automatic combustion air dampers, if
used.
2. Verify that boiler vent discharge and air intake are clean and
free of obstructions.
Flue gas vent system
1. Visually inspect entire flue gas venting system for blockage,
deterioration or leakage. Repair any joints that show signs of
leakage in accordance with vent manufacturer’s instructions.
2. Verify that masonry chimneys are lined, lining is in good
condition, and there are not openings into the chimney.
Failure to inspect for the above conditions and have
them repaired can result in severe personal injury or
death.
Pilot and main burner flames
1. Visually inspect pilot burner and main burner flames as directed
under Section 7, page 15 of this manual.
Water piping
1. Check the boiler interior piping and all system piping for signs
of leaks.
2. Repair any leaks before proceeding.
Electrical shock hazard — Turn off power to the boiler
before any service operation on the boiler except as
noted otherwise in this instruction manual. Failure to
turn off electrical power could result in electrical
shock, causing severe personal injury or death.
Do not use petroleum-based cleaning or sealing
compounds in boiler system. Severe damage to boiler
will occur, resulting in substantial property damage.
Eliminate all system or boiler leaks. Continual fresh
makeup water will reduce boiler life. Minerals can
build up in sections, reducing heat transfer,
overheating cast iron, and causing section failure.
Leaking water may also cause severe property
damage.
Boiler heating surfaces
1. Disconnect the vent pipe at the boiler inducer outlet connection
after turning off power to the boiler.
2. Use a bright light to inspect the flue pipe interior and inducer
interior.
3. Inspect the boiler vent outlet area and heating surfaces by
looking through the opening.
4. If the vent pipe or inducer interior show evidence of soot, follow
Cleaning boiler heating surfaces in this manual section to remove
the flue collector and clean the boiler if necessary after close
inspection of boiler heating surfaces. If there is evidence of rusty
scale deposits, check the water piping and control system to
make sure the boiler return water temperature is properly
maintained (per this manual).
5. Reconnect vent to inducer outlet and replace all boiler
components before returning to service.
6. Check inside and around boiler for evidence of any leaks from
the boiler. If found, locate source of leaks and repair.
Burners and base
1. After turning off power to the boiler, remove the inlet air box top
panel (Figure 16, item 13, page 34).
2. Inspect gasket (Figure 16, item 14, page 34).
2. Inspect burners and all other components in the inlet air box
and boiler base.
3. If burners must be cleaned, access the burner assembly by
first removing the burner baffle (Figure 16, item 4, page 34).
Then remove the screws securing the burner tray to the
manifold. Slide the burner tray out. Then brush and vacuum the
burners thoroughly, making sure all ports are free of debris.
4. Inspect the base insulation. Verify that the insulation is intact
and secure against all four sides of the base.
The boiler contains ceramic fiber and fiberglass
materials. Use care when handling these materials
per instructions on page 21 of this manual. Failure
to comply could result in severe personal injury.
If insulation is damaged or displaced, do not
operate the boiler. Replace or reposition insulation
as necessary. Failure to replace damaged insulation
can result in a fire hazard, causing severe personal
injury, death or substantial property damage.
5. Replace inlet air box top panel.
Do not operate boiler without inlet air box top panel
secured in place. Failure to comply could result in
severe personal injury, death or substantial property
damage.
Condensate drain system
1. If vent system is equipped with a condensate drain, check the
hose and connections for tightness.
2. Verify the hose is unobstructed and in good condition and that
condensate can flow freely. Replace hose if necessary.
The boiler contains ceramic fiber and fiberglass materials. Use care when handling these materials per instructions on
page 21 of this manual. Failure to comply could result in severe personal injury.