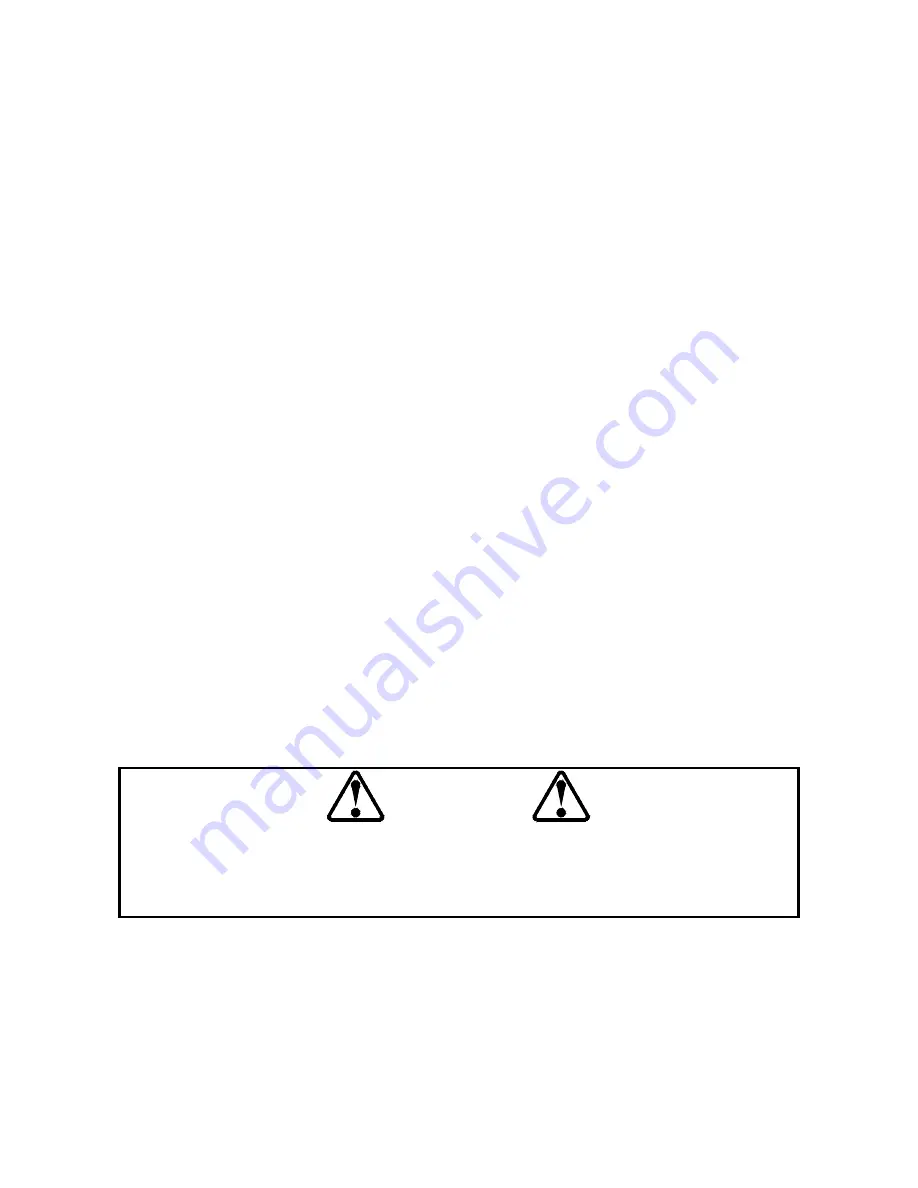
8
F. Plan the location of the Sample Collection Cabinet. Most often the desired site is at the beginning of the
sample grading process in the grain inspection area. If the material other than grain is being sampled, other
criteria may apply.
G. Plan the location of the concrete base for the hydraulic power unit. Preferably, it should be located within
four feet of the concrete probe base. If the Probe is separated from the power unit by more than four feet, the
user or installer may have to purchase additional hydraulic hose. Maximum separation between the Probe
and power unit should be held to ten feet or less.
H. Excessively long hydraulic hoses can result in pressure loss, which in turn results in slow, erratic probe
operation. Excessive vacuum hose length can produce low vacuum at the probe tip. The Sample Collection
System may not function properly.
I. It is recommended that guard posts and/or rails be placed around the Probe and hydraulic power unit for
protection from vehicular traffic.
J. Review all installation plans once more. Double-check to be sure that the probe will not interfere with any
power and communications lines, and that no conveyors or spouting are routed through the area where the
Probe is to operate.
3.3 Location
The Truck Probe is typically installed near the receiving truck scale and sample lab, as in Figure 2-1. Locate the
Truck Probe and associated equipment for ease of access and maintenance. The Truck Probe operator should have
an unobstructed view of the entire area of boom movement.
The Truck Probe is to be installed only as shown on the certified drawing(s). If an alternate mounting arrangement is
desired, contact InterSystems, prior to installation for proper guidance. The Truck Probe is of a general design with
modifications specifically for your application. It may be necessary to rework the Truck Probe in order for it to
function properly if you alter the application.
3.4 General Installation Guidelines
The Truck Probe assembly is designed to support ONLY its own weight. As shown on the certified drawing, the
Truck Probe must be installed on a special concrete foundation. The main stand base has eight clearance holes for
securing to the foundation. Refer to the certified drawing(s) of the Truck Probe for the dimensioned locations of
these holes.
DANGER
TRUCK PROBE CANNOT SUPPORT ANY OTHER EQUIPMENT! COLLAPSE OF THE WHOLE
SYSTEM CAN CAUSE DEATH, SERIOUS INJURY, AND EXTENSIVE DAMAGE TO EQUIPMENT.
PROPERLY SUPPORT ALL ELECTRICAL CONDUITS, AND CONVEYING LINES.
A. Verify that the concrete probe and power unit bases have cured to develop adequate strength.
B. Position the main stand assembly on the concrete foundation as shown on the certified drawing(s). Install a
washer and two (2) nuts on each of the anchor bolts. Verify that the main stand is plumb and tighten the
anchor nuts.
Summary of Contents for InterSystems STP
Page 5: ...4 FIGURE 1 1 TRUCK PROBE SAFETY LABEL LOCATIONS ...
Page 32: ...31 FIGURE 7 1 MAIN STAND ASSEMBLY ...
Page 33: ...32 FIGURE 7 2 TELESCOPING BOOM ASSEMBLY FIGURE 7 3 COMPARTMENTIZED CORE PROBES ...
Page 34: ...33 FIGURE 7 4 SAMPLE CABINETS ...
Page 35: ...34 FIGURE 7 5 VACUUM MOTOR UNITS ...
Page 36: ...FIGURE 7 7 6 HYDRAU ULIC POWER R UNIT ASSEMBLY 35 ...
Page 37: ...36 FIGURE 7 7 HYDRAULIC POWER UNIT FITTINGS HOSES ...