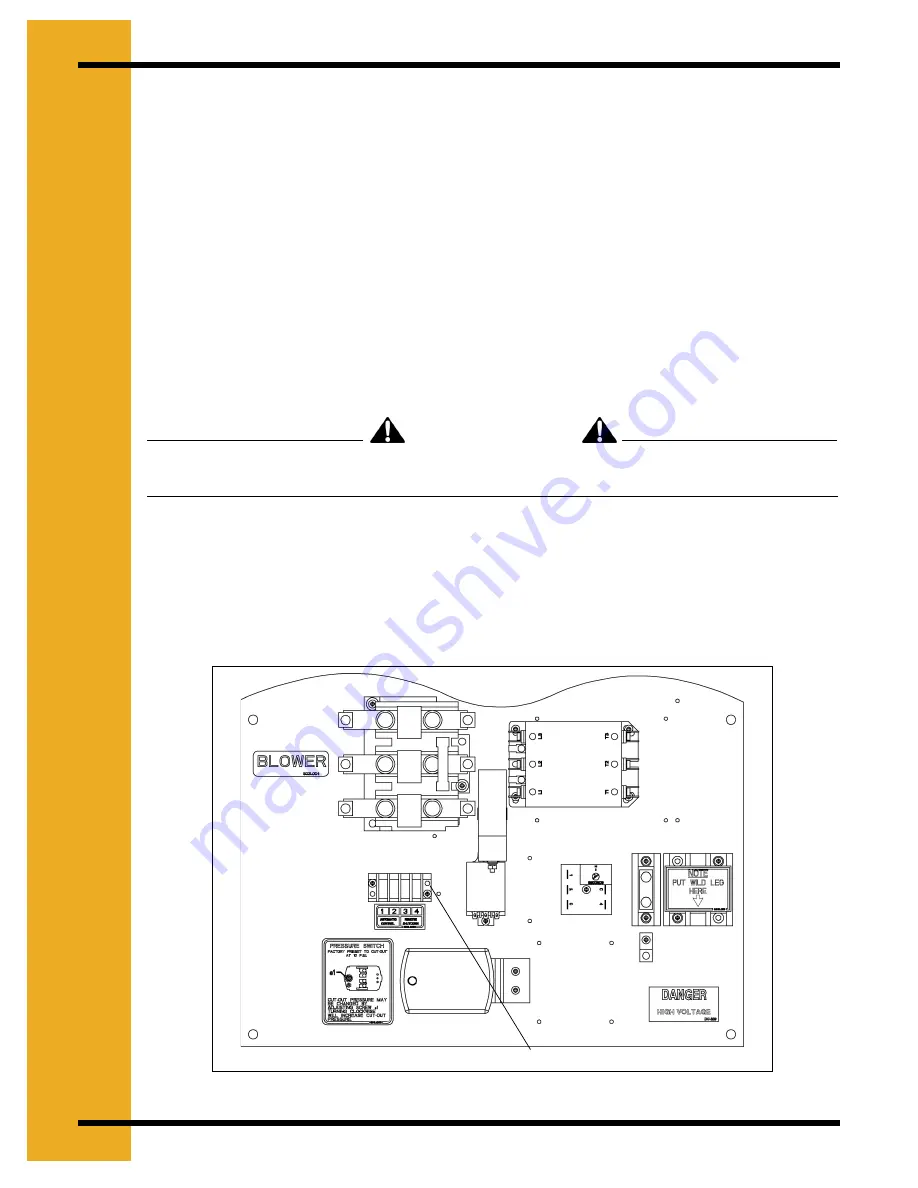
26
PNEG-1355 4" & 5" Air Systems
7. ASSEMBLY
7. Tripped Overload Indicator Light: This lamp will light up when any of the motor thermal
overloads in the control box has tripped. The overloads for all three circuits (Aux, Airlock,
and Blower) must have thermal overloads installed to operate the system. See Thermal
Unit chart Drawing on
8. 5 Amp Fuse: A five (5) Amp fuse protects the electrical components in the control box.
9. Control Switches: The operation of the blower, airlock and auxiliary equipment of the air
system is controlled by placing these switches in the “Auto”, “Manual” or “Off” position.
10. Automatic Control Terminals: When the air system is ready to run (i.e., the control ready
light is on), the system can then be started and run by completing the circuit between
terminals one (1) and two (2). The blower, airlock or auxiliary equipment will not run in the
automatic mode unless terminals one (1) and two (2) are connected. For example, a
closing set of contacts in a dryer control box would complete the circuit between terminals
one (1) and two (2) and automatically start the air system.
No voltage should be supplied to terminals one (1) and two (2). See the diagram
and drawing below.
11. Remote Shut-Down Control: A remote piece of equipment can be caused to shutdown with
the air system by putting terminals three (3) and four (4) in series with the control circuit of
the remote equipment. This circuit has a maximum current rating of 10 Amps. The circuit
between terminals three (3) and four (4) is closed whenever the control circuit ready light
is on, regardless of the position of the control switches. (“AUTO”, “OFF” or “ON”) See the
Diagram on
Figure 7M
WARNING
Steps 10 & 11: Automatic Control and Remote Shut-Down Control
Summary of Contents for 1200 Bu/Hr
Page 2: ...2 PNEG 1355 4 5 Air Systems ...
Page 10: ...10 PNEG 1355 4 5 Air Systems 2 DECALS DC 1386 DC 995 N10080 DC 994 DC 995 ...
Page 15: ...PNEG 1355 4 5 Air Systems 15 NOTES ...
Page 16: ...16 PNEG 1355 4 5 Air Systems 5 INSTALLATION Air System Tubing Dimensions Figure 5B ...
Page 28: ...28 PNEG 1355 4 5 Air Systems 9 WIRING Standard Schematic With Digital Amp Meter ...
Page 31: ...PNEG 1355 4 5 Air Systems 31 9 WIRING Twin Schematic With Digital Amp Meter ...
Page 40: ...40 PNEG 1355 4 5 Air Systems 12 PARTS LIST 4 700 5 1200 Standard Blower Parts ...
Page 42: ...42 PNEG 1355 4 5 Air Systems 12 PARTS LIST 4 5 Twin Blower Parts ...
Page 44: ...44 PNEG 1355 4 5 Air Systems 12 PARTS LIST 5 1700 Hi Capacity Blower Parts ...
Page 46: ...46 PNEG 1355 4 5 Air Systems 12 PARTS LIST 5 1700 Twin Hi Capacity Blower Parts ...
Page 48: ...48 PNEG 1355 4 5 Air Systems 12 PARTS LIST 4 5 Blower Filters ...
Page 50: ...50 PNEG 1355 4 5 Air Systems 12 PARTS LIST 4 5 Airlock Parts ...
Page 52: ...52 PNEG 1355 4 5 Air Systems 12 PARTS LIST Airlock Inlet Transition Assembly ...
Page 58: ...58 PNEG 1355 4 5 Air Systems 12 PARTS LIST Standard Control Panel Assembly 230 V 10 30 HP ...
Page 62: ...62 PNEG 1355 4 5 Air Systems 12 PARTS LIST Standard Control Panel Assembly 230 V 40 HP ...
Page 64: ...64 PNEG 1355 4 5 Air Systems 12 PARTS LIST Twin Control Panel Assembly 230 V 7 15 HP ...
Page 68: ...68 PNEG 1355 4 5 Air Systems 12 PARTS LIST Standard Control Panel Assembly 460 V 10 40 HP ...