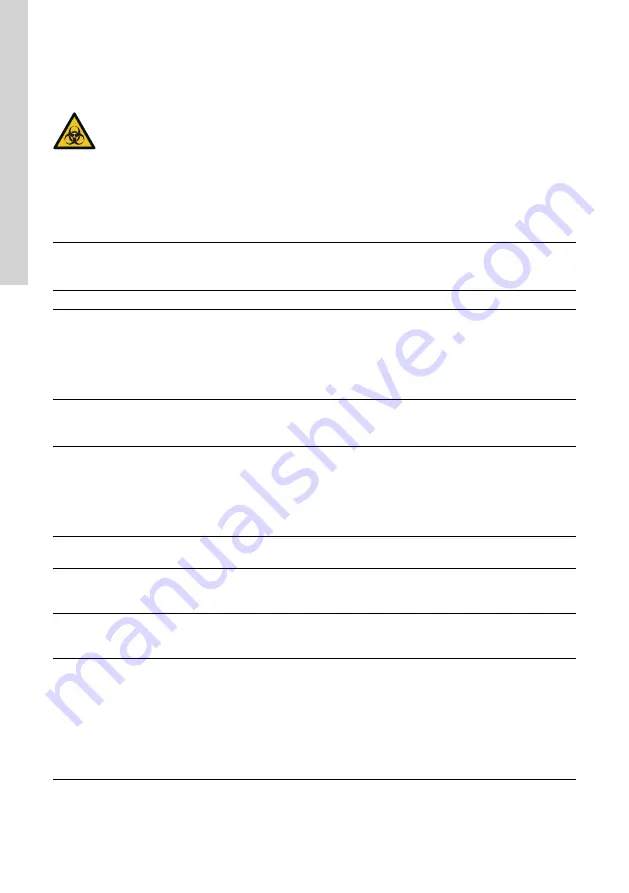
12. Fault finding the product
WARNING
Biological hazard
Death or serious personal injury
‐
Wear protective gloves, close the
isolating valves and drain the tank
before you start any work on the tank.
For faults indicated by alarms and related to the
controller, see the installation and operating
instructions of the controller.
For faults related to the pumps, see the installation
and operating instructions of the pumps.
12.1 The pump does not start.
Cause
Remedy
The float switch is blocked in low position.
1. Make sure that the float switch can move freely.
2. It may be necessary to adjust the cable length. See
section Setting the start levels.
The pump cable is defective.
Repair or replace the cable.
Related information
12.2 The pump does not stop.
Cause
Remedy
The float switch is blocked in high position.
1. Make sure that the float switch can move freely.
2. It may be necessary to adjust the cable length. See
section Setting the start levels.
Related information
12.3 The pump starts and stops randomly.
Cause
Remedy
The float switch is not set properly.
Adjust the cable length of the float switch. See section
Setting the start levels.
The level sensor tube is not fixed properly in the tank
and is moving up as the liquid rises. The sensor
receives wrong signals.
Fix the tube to the tank. See fig. 13.
The float switch cannot move freely because the
pump has moved.
Position the pump according to fig. Correct position of
UNILIFT CC and KP pumps or Correct position of
UNILIFT APB pumps.
Related information
3.12 Installing the pump
3.13.2 Assembling the pump connecting pipes
7.1 Setting the start levels
12.4 The tank is not emptying although the pump is running.
Cause
Remedy
There is an airlock in the pump impeller. The pump
cannot build up pressure.
Drill a hole of maximum 6 mm in the connecting pipes in
the tank. The air is pushed out when the pump starts,
and the pump builds up pressure. The pressure loss
due to the hole is negligible.
34
English (GB)
Summary of Contents for UNOLIFT
Page 1: ...UNOLIFT DUOLIFT Installation and operating instructions GRUNDFOS INSTRUCTIONS ...
Page 2: ......
Page 18: ...TM059633 UNILIFT AP35B AP50B TM059630 UNILIFT CC KP 18 English GB ...
Page 19: ...x4 TM082793 UNILIFT APG x4 TM059632 SEG 19 English GB ...
Page 20: ...x4 TM078303 DUOLIFT SEG 20 English GB ...
Page 21: ...x4 TM082794 DUOLIFT UNILIFT APG 21 English GB ...
Page 36: ...Appendix A A 1 Appendix TM061067 Unolift 270 Duolift 270 678 Appendix A ...