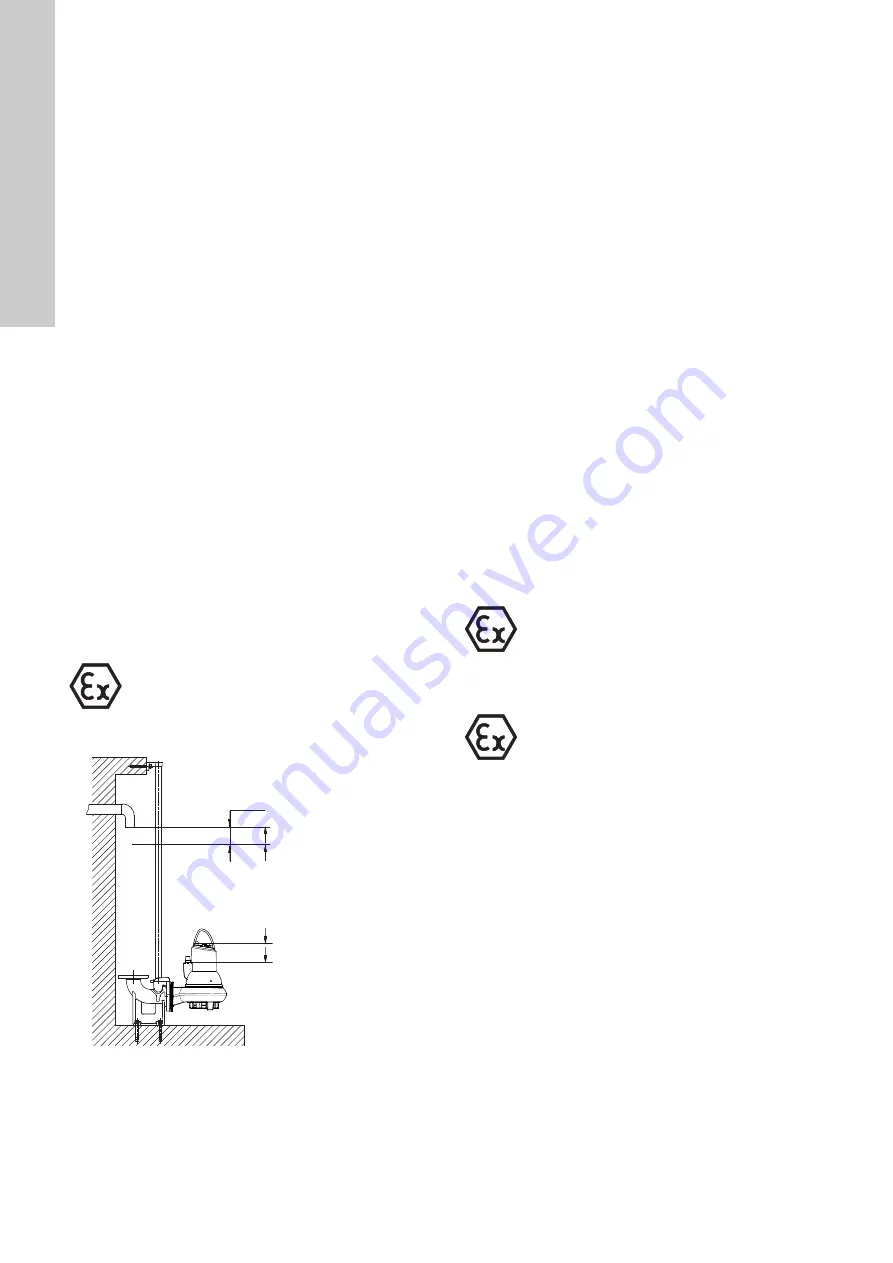
English (GB)
20
8.2 Pump controllers
The following LC and LCD pump controllers are available for level
control:
LC controllers are for one-pump-installations and LCD controllers
are for two-pump installations.
• LC 107 and LCD 107 with air bells
• LC 108 and LCD 108 with float switches
• LC 110 and LCD 110 with electrodes.
In the following description, "level switches" can be air bells, float
switches or electrodes, depending on the pump controller
selected.
The
LC
controller is fitted with two or three level switches:
One for start and the other for stop of pump. The third level
switch, which is optional, is for high-level alarm.
The
LCD
controller is fitted with three or four level switches:
One for common stop and two for start of the pumps. The fourth
level switch, which is optional, is for high-level alarm.
When installing the level switches, observe the following points:
• To prevent air intake and vibrations install the
stop level
switch
in such a way that the pump is stopped before the
liquid level is lowered below the top of the cable entry.
• In tanks with one pump, install the
start level switch
in such a
way that the pump is started at the required level; however,
the pump must always be started before the liquid level
reaches the bottom inlet pipe to the tank.
• In tanks with two pumps, the
start level switch
for pump 2
must start the pump before the liquid level reaches the bottom
inlet pipe to the tank, and the start level switch for pump 1
must start this pump correspondingly earlier.
• If installed, always install the
high-level alarm switch
about
10 cm above the start level switch; however, the alarm must
always be given before the liquid level reaches the bottom
inlet pipe to the tank.
For further information, see the installation and operating
instructions for the pump controller selected.
Fig. 10
Start and stop levels
Make sure that the effective volume of the tank does not become
so low that the number of starts per hour exceeds the maximum
permissible number. See section
8.3 Thermal switch, Pt1000 and PTC thermistor
All SL1 and SLV pumps have thermal protection incorporated in
the stator windings.
Pumps without sensor
Pumps without sensor have a thermal switch or a PTC thermistor.
Via the pump controller safety circuit, the thermal switch will stop
the pump by breaking the circuit in case of overtemperature
(approx. 150 °C). The thermal switch will reclose the circuit after
cooling. For pumps equipped with a PTC thermistor, connect the
thermistor to either the PTC relay or the I/O module to break the
circuit at 150 °C.
The maximum operating current of the thermal switch is 0.5 A at
500 VAC and cos
φ
0.6. The switch must be able to break a coil in
the supply circuit.
Pumps with sensor
Pumps with sensor have either a thermal switch and a Pt1000
sensor or a PTC thermistor in the windings, depending on the
installation site.
Via the pump controller safety circuit, the thermal switch or the
thermistor will stop the pump by breaking the circuit in case of
overtemperature (approx. 150 °C). The thermal switch or the
thermistor will reclose the circuit after cooling.
The maximum operating current of both the Pt1000 and the
thermistor is 1 mA at 24 VDC.
Non-explosion-proof pumps
When closing the circuit after cooling, the thermal protection can
restart the pump automatically via the controller. Pumps from
4 kW and up sold in Australia/New Zealand are fitted with a PTC
thermistor.
Explosion-proof pumps
Warning
Float switches used in potentially explosive
environments must be approved for this
application. They must be connected to the
Grundfos LC, LCD 108 pump controller via the
intrinsically safe LC-Ex4 barrier to ensure a safe
circuit.
TM
04 265
4 280
8
Start
Stop S1 operation
Alarm
Min. 10 cm
Stop S3 operation
Warning
The thermal protection of explosion-proof pumps
must not restart the pump automatically.
This ensures protection against overtemperature
in potentially explosive environments. In pumps
with sensor this is done by removing the short-
circuit between terminals R1 and R2 in the IO 111.
See Electrical data in the IO 111 installation and
operating instructions.
Warning
The separate motor-protective circuit breaker/
control box must not be installed in potentially
explosive environments.
Summary of Contents for SL1.100.100.40.4
Page 39: ...Appendix 39 15 Exploded drawings SLV TM04 2777 2605...
Page 40: ...Appendix 40 SL1 TM04 2778 0904...
Page 41: ...41...