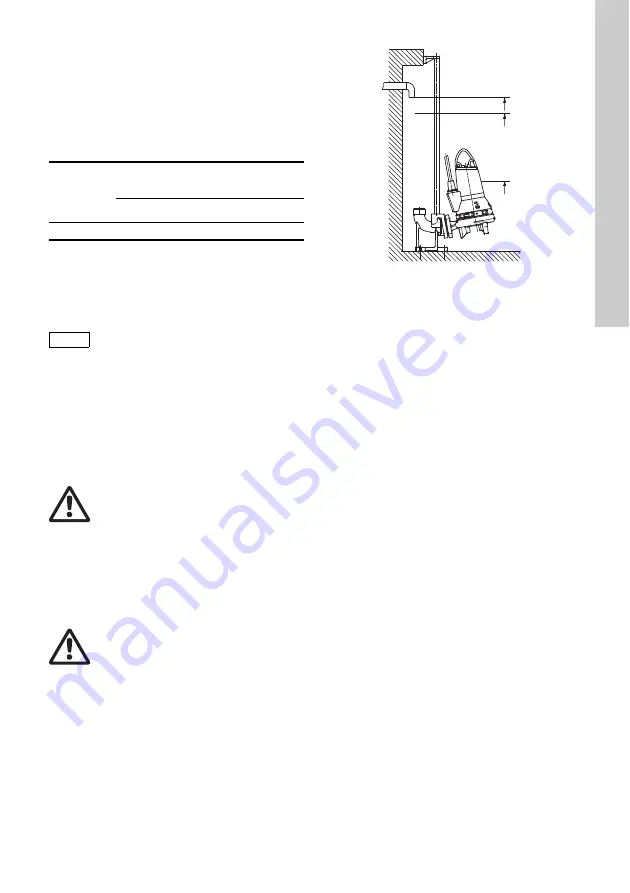
English (GB)
11
8.2 CU 100 control box
The CU 100 control box incorporates a motor-
protective circuit breaker and is available with level
switch and cable.
Single-phase pumps
A run capacitor must be connected to the control
box.
For capacitor sizes, see the table below.
Start and stop levels
The difference in level between start and stop can be
adjusted by changing the free cable length.
Long free cable = large difference in level
Short free cable = small difference in level.
•
To prevent air intake and vibrations, install the
stop level switch in such a way that the pump is
stopped before the liquid level is lowered below
the upper edge of the clamp on the pump.
•
Install the start level switch in such a way that the
pump is started at the required level; however,
the pump must always be started before the
liquid level reaches the bottom inlet pipe to the
tank.
Fig. 6
Start and stop levels
8.3 Pump controllers
The following LC and LCD pump controllers are
available:
LC controllers are for one-pump-installations and
LCD controllers are for two-pump-installations.
•
LC 107 and LCD 107 with air bells.
•
LC 108 and LCD 108 with float switches.
•
LC 110 and LCD 110 with electrodes.
In the following description, "level switches" can be
air bells, float switches or electrodes, depending on
the pump controller selected.
Controllers for single-phase pumps incorporate
capacitors.
LC:
The controller is fitted with two or three level
switches: One for start and the other for stop of
pump. The third level switch, which is optional, is for
high-level alarm.
LCD:
The controller is fitted with three or four level
switches: One for common stop and two for start of
the pumps. The fourth level switch, which is optional,
is for high-level alarm.
Pump type
Cs, starting
capacitor
Cd, run
capacitor
[
μ
F]
[V]
[
μ
F]
[V]
SEG 150
230
30
450
Note
Both the two following points must be
observed.
Warning
The CU 100 control box must not be
used for explosion-proof applications.
See section 8.3 Pump controllers.
Warning
The pump must not run dry.
An additional level switch must be
installed to ensure that the pump is
stopped in case the stop level switch is
not operating. See fig. 6.
The pump must be stopped when the
liquid level reaches the upper edge of
the clamp on the pump.
Float switches used in potentially
explosive environments must be
approved for this application.
They must be connected to the
Grundfos DC, DCD and LC, LCD 108
pump controller via an intrinsically
safe barrier to ensure a safe circuit.
TM
02
53
89
28
02
Alarm
Start
Stop