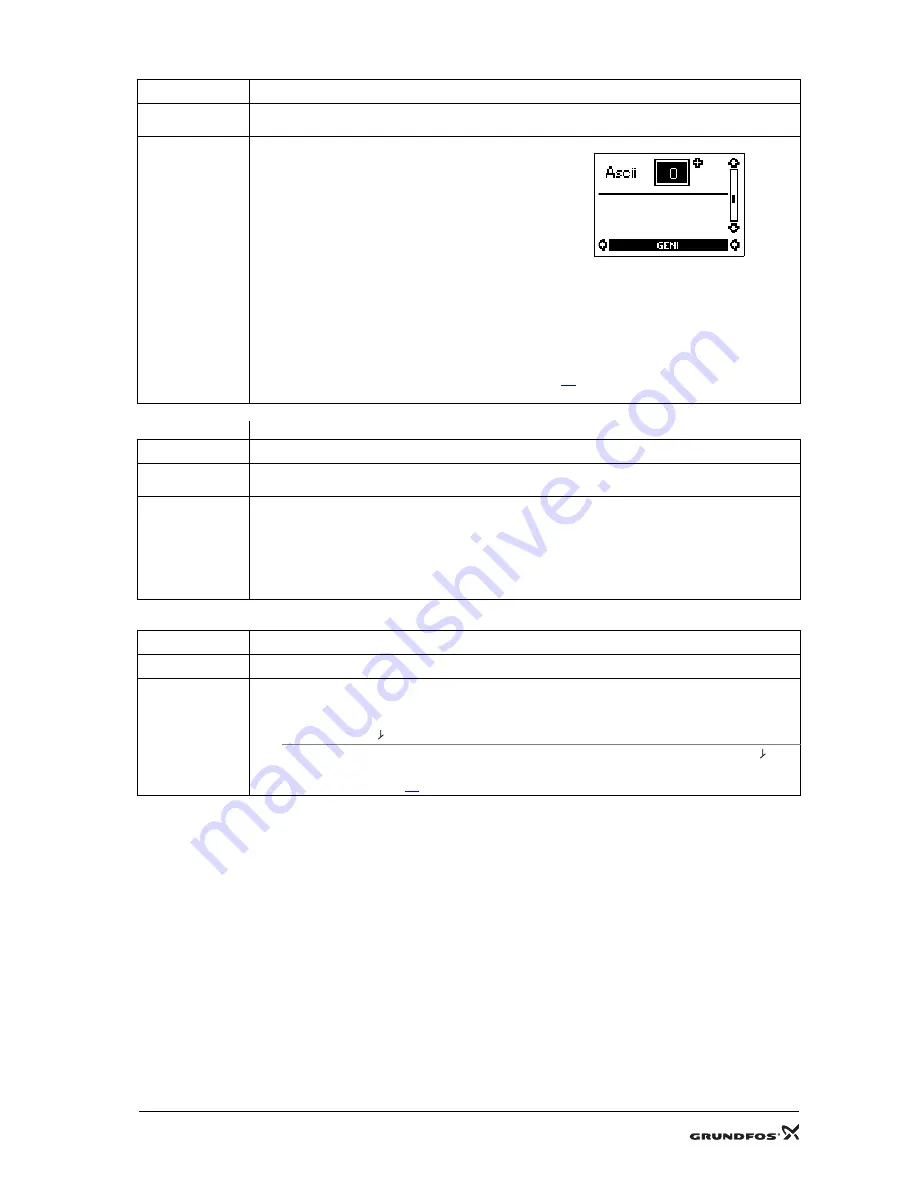
10 / 15
A1
A2
Description
Pump is running but not as the expected pump type.
Explanation
Configuration error
In case the terminal box cannot identify the stator type, the pump will run default as a 40-120 or a 65-120.
Check/remedy
Check by means of R100 which pump type the terminal
box has registered:
1. Switch R100 to service mode.
2. Go into the GENI menu in the display on the right.
3. Enter code 13.
R100 will now show which pump type the terminal box has registered. Check that the indication corresponds to
the actual pump type.
In case of error in the stator coding, the indication will be "ERR".
Is the pump type correct?
YES:
NO:
Fault is not due to a configuration error, but
possibly to a setting error or a system fault.
Check the stator coding according to the
drawing.
See
C2
.
In new R100 software updates the pump type can be read in the start-up display.
Description
The twin-head pump does not control its performance optimally.
Explanation
Configuration error
The terminal box uses a wrong set of parameters.
Check/remedy
As the right and the left pump head do not have the same hydraulic performance, there are a right and left set of
parameters.
Correct configuration is carried out by means of the GENI modules where the Master module must always be fit-
ted on the right pump head. (Terminals X and Q are short-circuited.) The modules must be product number
605945VO1 or higher.
If no GENI modules are used on the twin-head pumps, the configuration can be carried out by means of R100
Turbo.
Description
Pump is running at too low or high pressure.
Explanation
Setpoint setting is incorrect.
Check/remedy
1.
Is an external setpoint signal connected?
NO:
YES:
Set setpoint according to system specifications.
Check the connection to the GENI module and the external setpoint signal. Note that the termi-
nals MIN - must be closed for the setpoint setting to work.
2.
Does the pump speed vary (listen to the pump) according to the input signals on terminals 10 V - ?
YES:
NO:
Pump is OK.
Proceed to point
B1
.