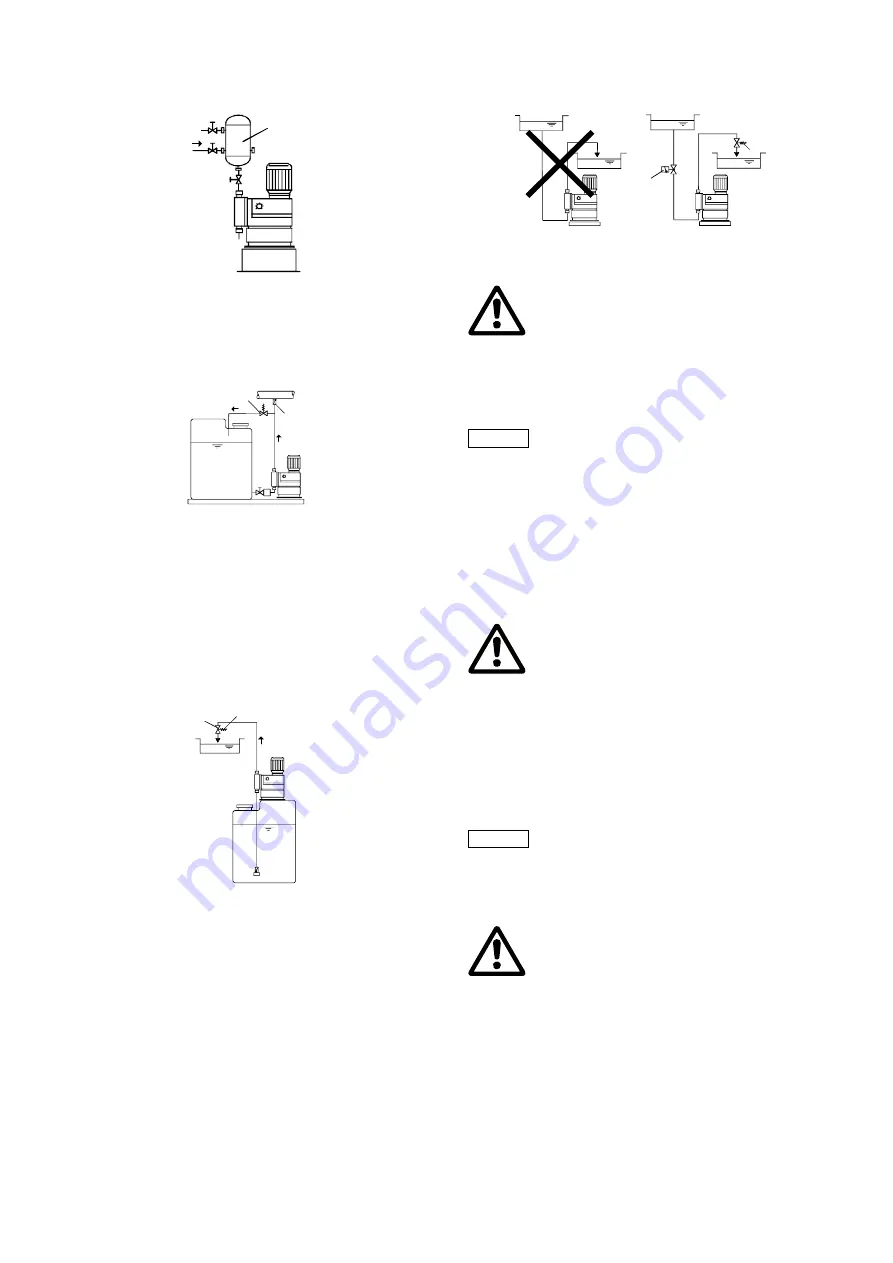
15
• Note for discharge-side installation: To protect the piping, use
a pulsation damper (8i) for rigid piping longer than 3 metres
and tubing longer than 5 metres.
Fig. 8
Installation with discharge-side pulsation damper
• For degassing and viscous media: flooded suction.
• To protect the dosing pump and the discharge line against
excessive pressure build-up, install a relief valve (6i) in the
discharge line.
Fig. 9
Installation with relief valve
With open outflow of the dosing medium or a counter-
pressure below 1 bar
• Install a pressure-loading valve (7i) immediately before the
outlet or the injection unit.
A positive pressure difference of at least 1 bar must be ensured
between the counter-pressure at the injection point and the
pressure of the dosing medium at the pump suction valve.
• If this cannot be ensured, install a pressure-loading valve (7i)
in the discharge line.
Fig. 10
Installation with pressure-loading valve
• To avoid the siphon effect, install a pressure-loading valve (7i)
in the discharge line and, if necessary, a solenoid valve (14i) in
the suction line.
Fig. 11
Installation to avoid the siphon effect
8.3 Mounting
• Mount the pump horizontally on the tank or on a console using
four M8 screws.
8.4 Tube / pipe lines
8.4.1 General
8.5 Connecting the suction and discharge lines
• Connect the suction line to the suction valve.
– Install the suction line in the tank so that the foot valve
remains 5 to 10 mm above the bottom of the tank or the
possible level of sedimentation.
• Connect the discharge line to the discharge valve.
T
M
03
6
3
01
45
06
T
M
03
63
02
45
06
TM
03
63
03
45
06
8i
6i
10i
p
7i
p
1 bar
p
≥
1 bar
TM
03
63
04
45
06
Warning
Risk of hot surfaces!
Pumps with AC motors may become hot.
Allow a minimum space of 100 mm to the fan
cover!
Caution
Gently tighten the screws in order not to damage
the plastic enclosure!
Warning
To protect the dosing pump against excessive
pressure build-up, install a relief valve in the
discharge line.
Only use the prescribed line types!
All lines must be free from strain!
Avoid loops and buckles in the tubes!
Keep the suction line as short as possible to
avoid cavitation!
If necessary, use swept bends instead of elbows.
Observe the chemical manufacturer's safety
instructions when handling chemicals!
Make sure that the pump is suitable for the actual
dosing medium!
The flow must run in the opposite direction to
gravity!
Caution
The resistance of the parts that come into contact
with the media depends on the media, media
temperature and operating pressure. Ensure that
parts in contact with the media are chemically
resistant to the dosing medium under operating
conditions!
Warning
All lines must be free from strain!
Only use the prescribed line types!
14i
p
1
p
2
2
p - p
1
1 bar
>
_
p
2
-p
1
≥
1 bar
Summary of Contents for DMX 115-3
Page 1: ...DMX 221 GRUNDFOS ALLDOS INSTRUCTIONS Installation and operating instructions ...
Page 29: ...29 ...
Page 30: ...30 ...