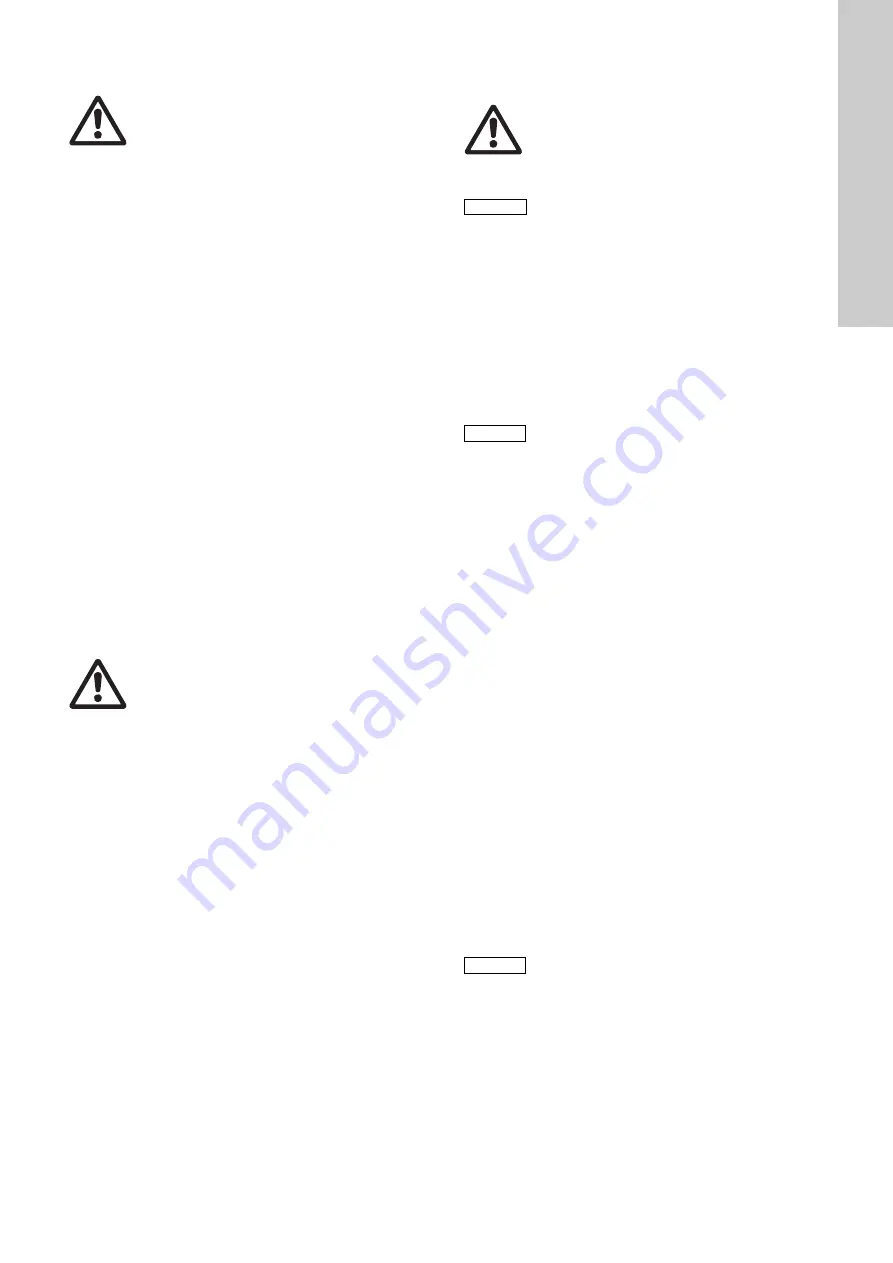
English (GB)
49
10.4 Resetting the diaphragm
If nothing indicates that dosing liquid has entered the pump
housing, the diaphragm must be reset to the back dead point
(end of suction stroke). As the stroke usually ends at the front
dead point, reset the diaphragm as follows:
• Stop the pump (LED lights up red),
• Press the "Up" and "Down" buttons simultaneously.
– The diaphragm is reset.
10.5 Diaphragm breakage
If the diaphragm leaks or is broken, dosing liquid escapes from
the drain opening (fig.
, pos. H) on the dosing head flange.
In case of diaphragm breakage, the safety diaphragm (pos. S)
and the O-rings (pos. Y) protect the pump housing against
ingress of dosing liquid.
When dosing crystallising liquids the drain opening can be
blocked by crystallisation. If the pump is not taken out of
operation immediately, pressure can build up between the
diaphragm (pos. Q) and the safety diaphragm in the flange (pos.
S) and the O-rings (pos. Y). The pressure can press dosing liquid
through the safety diaphragm or the screw holes into the pump
housing.
Most dosing liquids don’t cause any danger when entering the
pump housing. However a view liquids can cause a chemical
reaction with inner parts of the pump. In the worst case, this
reaction can produce explosive gases in the pump housing.
To avoid any danger resulting from diaphragm breakage, observe
the following:
• Perform regular maintenance.
See section
.
• Never operate the pump with blocked or soiled drain opening.
– If the drain opening is blocked or soiled, proceed as
described in section
• Never attach a hose to the drain opening. If a hose is attached
to the drain opening, it is impossible to recognise escaping
dosing liquid.
• Take suitable precautions to prevent harm to health and
damage to property from escaping dosing liquid.
• Never operate the pump with damaged or loose dosing head
screws.
10.6 Replacing the diaphragm
10.6.1 Resetting the diaphragm
If nothing indicates that dosing liquid has entered the pump
housing when replacing the diaphragm, reset the diaphragm as
described in section
10.6.2 Switching off the pump
1. Switch off the pump and disconnect it from the power supply.
2. Depressurise the system.
3. Take suitable steps to ensure that the returning dosing
medium is safely collected.
10.6.3 Replacing the diaphragm
See fig.
or
.
1. Loosen the screws (1q) on the dosing head (2).
2. Remove the dosing head (2) with dosing head disk (2q).
3. Unscrew the diaphragm (Q) counter-clockwise.
4. Make sure that the drain opening (H) is not blocked or soiled.
Clean if necessary.
5. Only for DDI 150-4: loosen the screws (X) on the intermediate
flange (5q) and remove the intermediate flange.
6. Check the safety diaphragm (S) for wear and damage.
Additional check the screws (X) and o-rings (Y) for signs of
contact with medium.
– If dosing liquid has possibly entered the pump housing
proceed as described in section
.
– If nothing indicates that dosing liquid has entered the pump
housing, go on with the next step.
7. Replace the O-rings (Y) by new ones.
8. Only for DDI 150-4: replace the intermediate flange (5q) and
cross-tighten the screws (X).
Torque: 7 Nm (+ 1 Nm).
9. Screw in the new diaphragm (Q).
– For pumps with diaphragm leakage detection: Screw in the
complete diaphragm package.
10. Replace the dosing head (2) with dosing head disk (2q) and
cross-tighten the screws (1q).
Torque: 7 Nm (+ 1 Nm).
11. Restart the dosing pump.
Warning
Danger of explosion, if dosing liquid has entered the
pump housing!
If the diaphragm is possibly damaged, don’t connect
the pump to the power supply!
Warning
Danger of explosion, if dosing liquid has entered the
pump housing!
When operating the pump with a damaged
diaphragm, dosing liquid can enter the pump
housing.
In case of diaphragm breakage, immediately
separate the pump from the power supply!
Make sure that the pump cannot be put back into
operation by accident!
Dismantle the dosing head without connecting the
pump to the power supply. Make sure that no dosing
liquid has entered the pump housing. Proceed as
described in section
.
Warning
Risk of chemical burns!
Wear protective clothing (gloves and goggles) when
working on the dosing head, connections or lines!
Do not allow any chemicals to leak from the pump.
Collect and dispose of all chemicals correctly!
Note
If possible, rinse the dosing head, e.g. by flushing it
with water.
Caution
The O-rings must be correctly placed in the specified
groove.
Caution
After initial start-up and after each time the
diaphragm is changed, tighten the dosing head
screws.
After approximately 6-10 operating hours or two
days, cross-tighten the dosing head screws using a
torque wrench.
Torque: 7 Nm (+ 1 Nm).
Summary of Contents for DDI 150-4
Page 2: ...2 ...
Page 630: ...630 ...