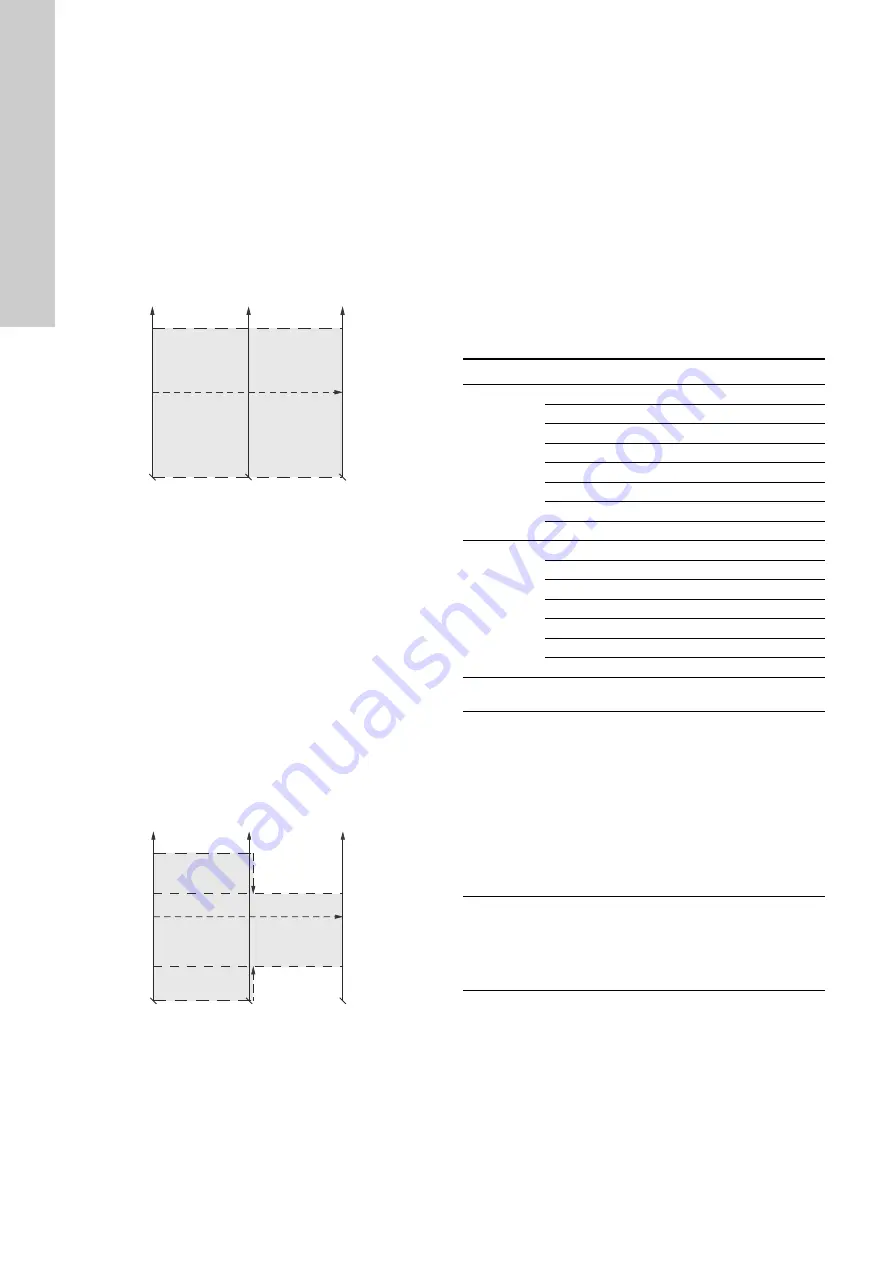
English (GB)
14
7.2.6 Setpoint in open-loop control
Hydro MPC and Multi-E
The setpoint is written to module 2 bytes 4 and 5 Setpoint as a
percentage value scaled in 0.01 % of the maximum performance.
The selected setpoint is reflected in module 41 UserSetpoint with
the same scaling.
The actual setpoint, whether it has been set via Grundfos GO
Remote, the pump or controller display or buttons, or the fieldbus,
can be read from module 20 ActualSetpoint, and it reflects
whatever limitations, for example power or frequency limits, that
might be active in the system. It equals the value that the booster
system actually uses.
* Percentage of system performance.
Fig. 19
Setpoint in open-loop control for Hydro MPC and Multi-
E
TPED and MAGNA3-D
The setpoint is written to module 2 bytes 4 and 5 Setpoint as a
percentage value scaled in 0.01 % of the nominal pump
frequency f
nom
. The selected setpoint is reflected in module 41
UserSetpoint with the same scaling. From the fieldbus, it will get
whatever value written to Setpoint but from the display and
Grundfos GO Remote, it is truncated to the internal pump
frequency limits [f
min
; f
max
].
The actual setpoint, whether it has been set via Grundfos GO
Remote, the pump display, the pump buttons or the fieldbus, can
be read from module 20 ActualSetpoint, and it always reflects the
frequency limitations. It equals the value that the pump actually
uses. Values of f
min
, f
max
and f
nom
can be read via Grundfos GO
Remote.
* Percentage of
fnom
.
Fig. 20
Setpoint in open-loop control for TPED and MAGNA3-
D
7.2.7 Multi-E model H and twin-head pump TPED model H
control
• For Multi-E with a CIM module in the master pump only, set
CopyToLocal (Module 2, byte 1, bit 4) to value "1" in the
master pump.
• For Multi-E with a CIM module in two pumps, always set
CopyToLocal (Module 2, byte 1, bit 4) to value ‘1’ in both
pumps. Any writings to the control module (module 2) must be
written to each pump.
• A TPED model H is essentially a Multi-E model H with two
pumps. Mount a CIM module in each pump head. Always set
CopyToLocal (Module 2, byte 1, bit 4) to value ‘1’ in both pump
heads. Any writings to the control module (Module 2) must be
written to each pump head.
7.3 Status module (StatusModule, module 1)
The status module is a PROFIBUS/PROFINET input module
used for reading status from booster systems. Its data type is 10,
non-standard.
* Not supported by Hydro Multi-E.
TM
0
7
0
149
4
317
TM
07
01
50
43
17
X
set
0 %
100 %
X
act
Setpoint*
(ControlModule
byte 4 and 5)
UserSetpoint*
(module 41)
ActualSetpoint*
(module 20)
X
set
0 %
f
nom
100 %
X
act
Setpoint*
(ControlModule
byte 4 and 5)
UserSetpoint*
(module 41)
ActualSetpoint*
(module 20)
f
min
f
max
Byte
Bit
Name
Byte 1
(data type 5)
0
AccessMode
1
OnOff
2
Fault
3
Warning
4
-
5
AtMaxSpeed
6
-
7
AtMinSpeed
Byte 2
(data type 5)
0-1
-
2
CopyToLocal
3
ResetFaultAck
4
SetPointInfluence
5
-
6
Rotation
7
-
Bytes 3 and 4
(data type 6)
ProcessFeedback [0.01 %]
Byte 5
(data type 5)
ControlMode
[enumeration]
0: ConstSpeed*
1: ConstFreq*
2: -
3: ConstHead
4: ConstPressure
5: ConstDiffPress
6: VarDiffPress
7: ConstFlow
8: ConstTemp
9: ConstTempDiff
10: ConstLevel
Byte 6
(data type 5)
OperatingMode
[enumeration]
0: AutoControl
1-3: -
4: OpenLoopMin*
5: -
6: OpenLoopMax
Pumpland.ru
Summary of Contents for CIM 150 PROFIBUS DP
Page 34: ...34 Pumpland ru...