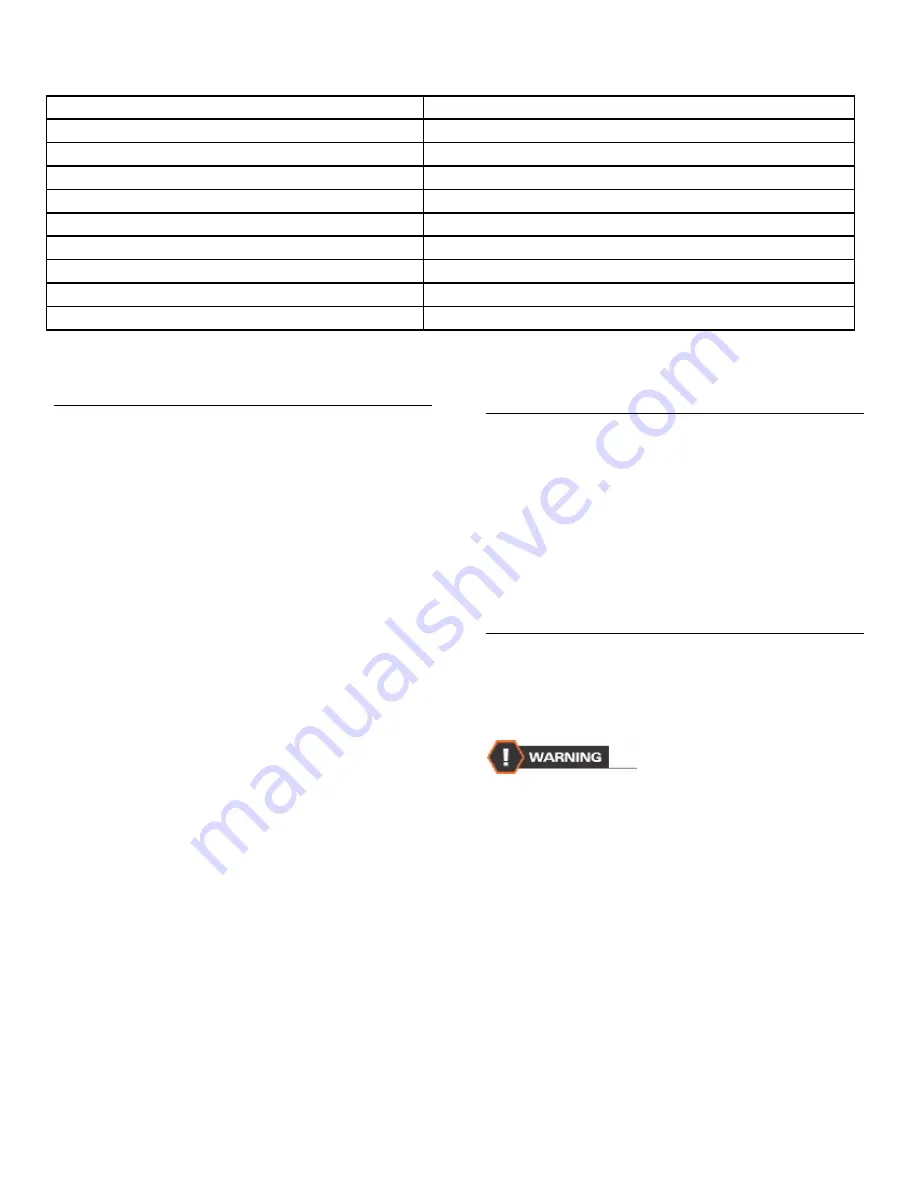
2
1. Contact your chemical or fluid supplier to check for compatibility
with pump prior to installation and operation.
2. Assemble the 2 parts of the Discharge spout together & fasten
the assembly onto the outlet on the main pump body. Use PTFE
tape or equivalent sealant tape. Do not use paste pipe sealant.
3. Insert the handle shaft through the pump handle.Fix the
pump handle onto the crank arm & connect the crank to the
crankshaft on the pump body. Secure the connection using the
hex bolt & hex nut provided. Make sure that the bolt fits onto
the depression in the crankshaft.
4. Assemble the suction tube parts, depending upon the drum
size on which the pump is to be installed. The tail pipe with
the strainer may be connected direct onto the pump inlet or
assembled with one extension or both extensions, depending
upon drum size. All 3 parts must be connected for use with
55 gallon / 205 litre drums. It is good practice to use a sealant
such as PTFE in connecting the suction tube parts for a totally
leak-proof connection.
5. Choose the bung adapter from the two that best fits your
drum. Each pack comes with two adapters, which have slight
difference in the threads to suit different drums. Slide the
selected 2” bung onto the tube from the top end & tighten
the suction tube onto the inlet on the main pump body. It is
good practice to use a sealant such as PTFE in connecting the
suction tube to the pump inlet.
6. Insert the pump assembly into the drum from the 2” bung
opening on the drum.
7. Once the bottom of the pump touches the base of the drum,
securely fasten the bung onto the drum. Now very lightly
tighten the bung onto the suction tube
PUMP ASSEMBLY & INSTALLATION
OPERATION
MAINTENANCE
Do not use the pump with Acetone, Lacquer, Mineral Oils,
Solvents, Turpentine etc..
Take an empty container & place it below the discharge spout. Start
rotating pump handle. Within a maximum of 7 rotations, pump will
be primed & will start dispensing media. In a rare case, where the
pump does not get primed, the same can be done by reversing the
outlet discharge spout on the pump & pouring about 1 oz. of any oil
into the outlet & operating the pump handle for about 7 rotations.
Once you have completed pumping the media, it is a good practice
to invert the discharge spout sideways for a non-drip operation.
Regularly check pump and suction tubes for leaks. Leaks in the
suction line or in pump housing will cause inefficient pumping and
loss of prime.
SPECIFICATION
Pump Type
Rotary
Flow
8 oz. per stroke
Maximum fluid Temperature
104° F / 40° C
Mounting
2” MNPT Bung
Suction Tube Outlet O.D.
1-7/32”
Suction Tube
3 piece / Threaded
Discharge Tube Outlet O.D.
1”
Outlet Type
2 Pc curved discharge spout
Wetted Material of Construction
Stainless Steel, Ryton, Viton and Glass Filled Polypropylene
Maximum Viscosity
2000 SSU