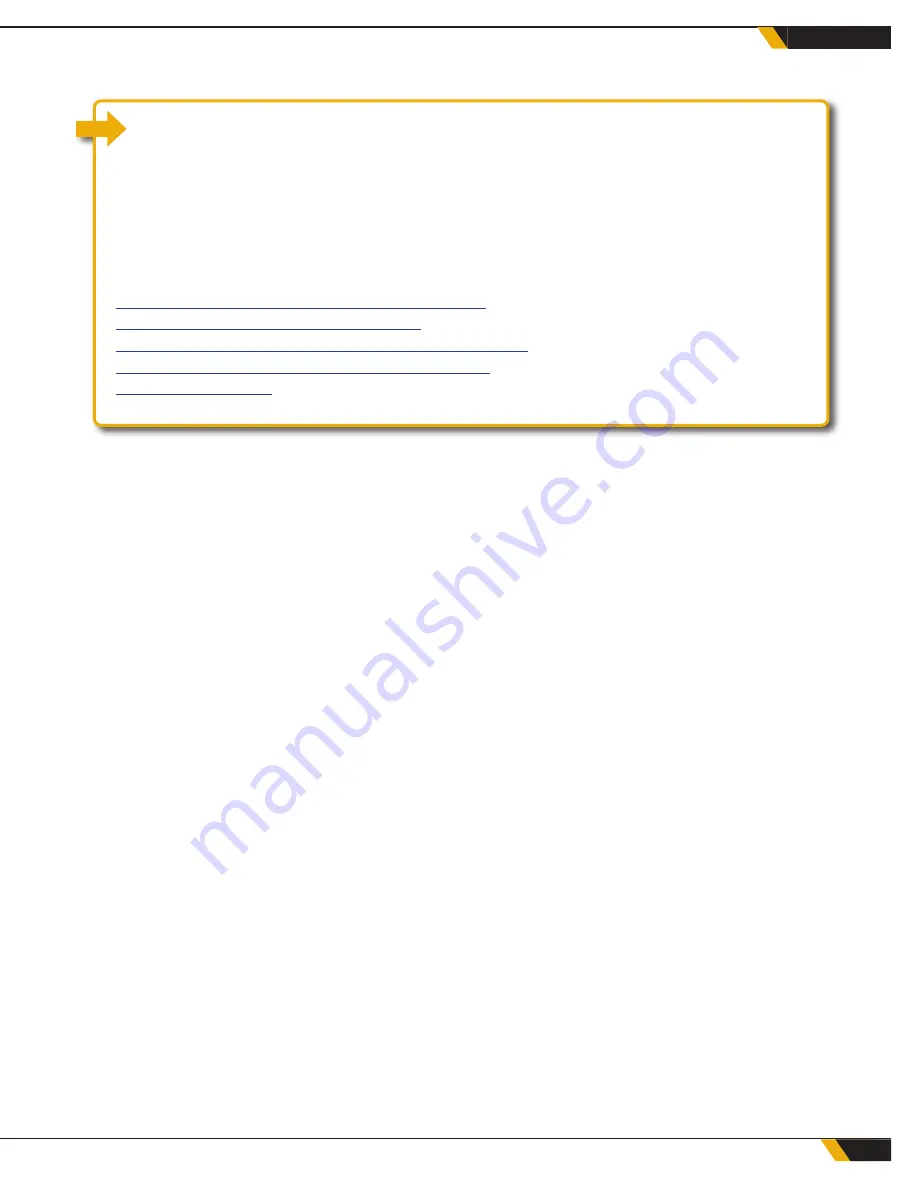
WWW.GFWORLDWIDE.COM | +1 (208) 664-9291
GUIDELINES
Equipment and vehicles must be maintained to be safe and reliable. Due to Ground Force Worldwide’s global
presence and distribution, and the myriad of local, state, and federal regulations, it is impractical to provide
specific details of these regulations. The following are basic guide lines, which do NOT supersede on-site
requirements and regulations, which MUST be followed.
• Ensure that ALL operators have been trained on the
equipment they use and operate.
•
Check vehicles at the beginning of each shift to
ensure that parts, equipment and accessories are
in safe operating condition. Repair or replace any
defective parts or equipment prior to use.
•
Ensure the service, emergency and park brake sys
-
tems are operational. Verify audible backup alarm
system is operational and working. Headlights, tail
lights, and brake lights MUST be operational. Verify
the windshield is clear and the windshield wipers
are operational.
•
DO NOT operate the vehicle in reverse with an
obstructed rear view, unless it has a signal alarm
capable of being heard above ambient noise levels
or a signal observer indicates that it is safe to move
vehicle. Some operational areas require a spotter at
all times.
• Equipment should have roll-over protection, and
protection from falling debris as required by law.
• Ensure that vehicles used to transport workers have
seat belts, firmly secured and adequate for the
number of workers to be carried or transported.
•
DO NOT modify the equipment’s capacity or safety
features without written approval from the Ground
Force Mfg. Engineering Department.
•
Prior to permitting equipment or vehicles onto an
access roadway or grade, verify that the roadway
or grade is constructed and maintained to safely
accommodate the equipment, vehicles and loads
involved.
•
Vehicles and equipment loaded from the top must
have cab shields or canopies to protect the operator
while loading.
•
Verify the Pre-Shift Inspection has been completed
and signed off.
•
Based on site conditions, you may choose to have
the chassis supplier lock out the top gears to pre
-
vent excessive speed.
This safety guide is provided by Ground Force Worldwide to assist you in making
a safer workplace. Specific regulations at the site of operations supersede all basic
recommendations provided in following sections.
For more information contact your national, state, or local authority. The following
links are provided to assist you in compliance:
Occupational Safety and Health Administration
Mine Safety and Health Administration
Canadian Centre for Occupational Health and Safety
European Agency for Safety and Health at Work
9
SAFETY
Summary of Contents for 717H01
Page 8: ...WWW GFWORLDWIDE COM 1 208 664 9291 OPERATION MAINTENANCE MANUAL SAFETY 8...
Page 15: ...WWW GFWORLDWIDE COM 1 208 664 9291 OPERATION MAINTENANCE MANUAL PRE COMMISSIONING 15...
Page 28: ...WWW GFWORLDWIDE COM 1 208 664 9291 OPERATION MAINTENANCE MANUAL WATER CONTROL SYSTEM 28...
Page 38: ...WWW GFWORLDWIDE COM 1 208 664 9291 OPERATION MAINTENANCE MANUAL MAINTENANCE SCHEDULES 38...
Page 41: ...WWW GFWORLDWIDE COM 1 208 664 9291 OPERATION MAINTENANCE MANUAL TROUBLESHOOTING 41...
Page 52: ...WWW GFWORLDWIDE COM 1 208 664 9291 OPERATION MAINTENANCE MANUAL WARRANTY 52...