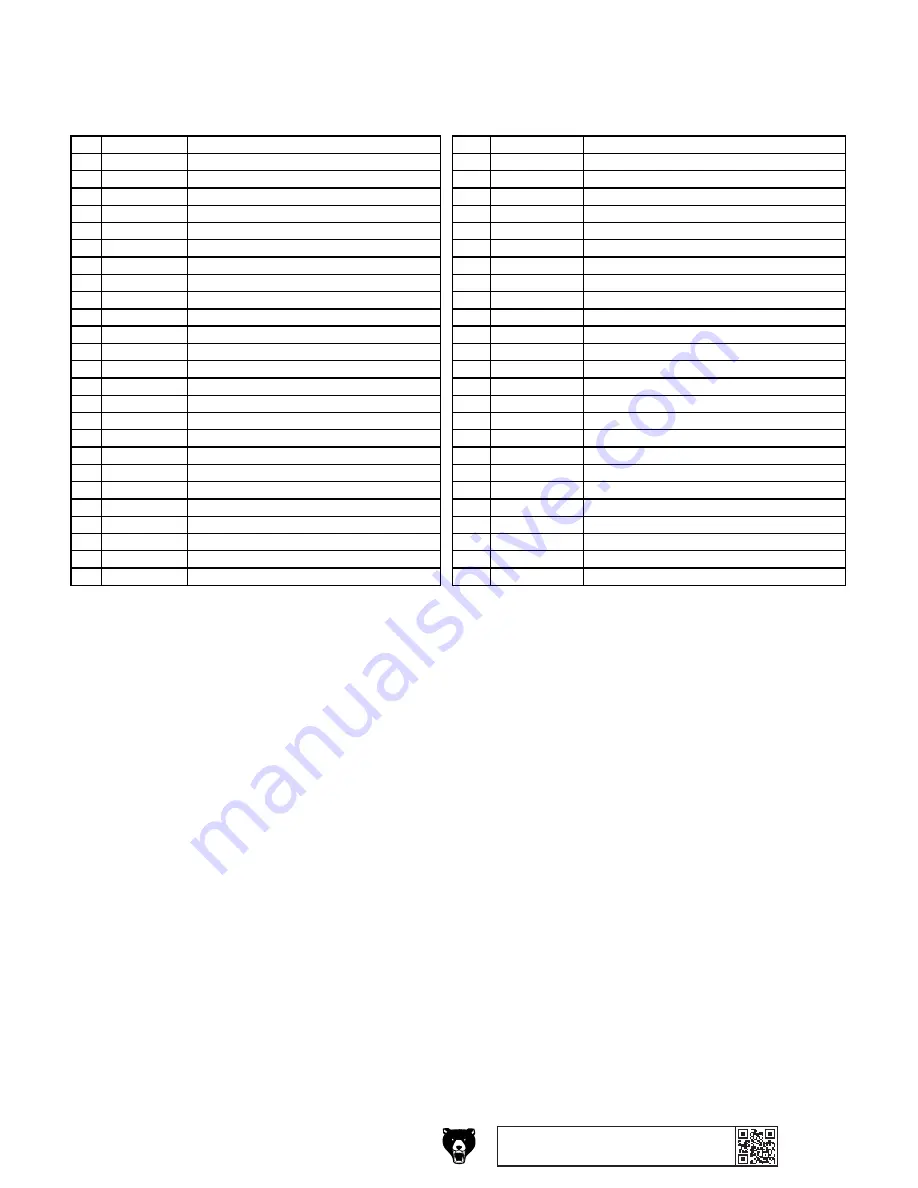
Model T32720 (Mfd. Since 06/21)
-35-
BUY PARTS ONLINE AT GRIZZLY.COM!
Scan QR code to visit our Parts Store.
REF PART #
DESCRIPTION
REF PART #
DESCRIPTION
1
PT32720001
HEX NUT M12-1.75
27
PT32720027
ADJUSTMENT NUT M12-1.75 KN
2
PT32720002
FLAT WASHER 12MM
28
PT32720028
TOOL REST
3
PT32720003
GRINDING WHEEL TYPE-5 10 X 2-1/2 X 1/2
29
PT32720029
MOTOR TENSION NUT M8-1.25
4
PT32720004
ARBOR BUSHING
30
PT32720030
ROLL PIN 5 X 25
5
PT32720005
MACHINE HOUSING
31
PT32720031
MOTOR TENSION CAP
6
PT32720006
GRINDING WHEEL SPINDLE
32
PT32720032
CIRCUIT BOARD CR431V7
7
PT32720007
DRIVE WHEEL
33
PT32720033
KNOB BOLT M6-1 X 22, 6-LOBE, D30
8
PT32720008
DRIVE WHEEL TIRE
34
PT32720034
STRAIN RELIEF TYPE-1 1/2"
9
PT32720009
STROPPING WHEEL
35
PT32720035
STRAIGHT EDGE SHARPENING JIG
10
PT32720010
FLAT WASHER 8MM
35-1
PT32720035-1
RUBBER BUSHING
11
PT32720011
KNOB M8-1.25, 9-LOBE, D50
35-2
PT32720035-2
CONICAL COMP SPRING 0.8 X 8 X 13, 13OD
12
PT32720012
SWITCH BOX
35-3
PT32720035-3
CLAMP PLATE
13
PT32720013
ON/OFF SWITCH KEDU HY18
35-4
PT32720035-4
FLAT WASHER 6MM
14
PT32720014
CONTROL PANEL
35-5
PT32720035-5
KNOB BOLT M6-1 X 20, 6-LOBE, D30
15
PT32720015
TAP SCREW M4.2 X 16
35-6
PT32720035-6
BASE PLATE
16
PT32720016
STRAIN RELIEF TYPE-3 PG9
36
PT32720036
HEX NUT M8-1.25 THIN
17
PT32720017
RUBBER FOOT
37
PT32720037
FLAT WASHER 12MM
18
PT32720018
POWER CORD 18G 3W 78" 5-15P
38
PT32720038
ANGLE GUIDE
19
PT32720019
MOTOR 80W 120V 1-PH
39
PT32720039
CRIMP CONNECTOR 7.6 X 17.5MM
20
PT32720020
MOTOR PIVOT SHAFT
40
PT32720040
TAP SCREW M4.2 X 8
21
PT32720021
E-CLIP 10MM
41
PT32720041
DRIVE WHEEL COVER
22
PT32720022
COMPRESSION SPRING 1.2 X 13.4 X 75
42
PT32720042
TAP SCREW M4 X 14
23
PT32720023
EXT RETAINING RING 10MM
43
PT32720043
VARIABLE-SPEED DIAL
24
PT32720024
WATER RESERVOIR
44
PT32720044
CARBON BRUSHES (PAIR)
25
PT32720025
KNOB BOLT M8-1.25 X 45, 9-LOBE, D35
45
PT32720045
BRUSH CAP
26
PT32720026
LOCK COLLAR
46
PT32720046
ABRASIVE STROPPING PASTE
Main Parts List
Summary of Contents for T32720
Page 40: ......