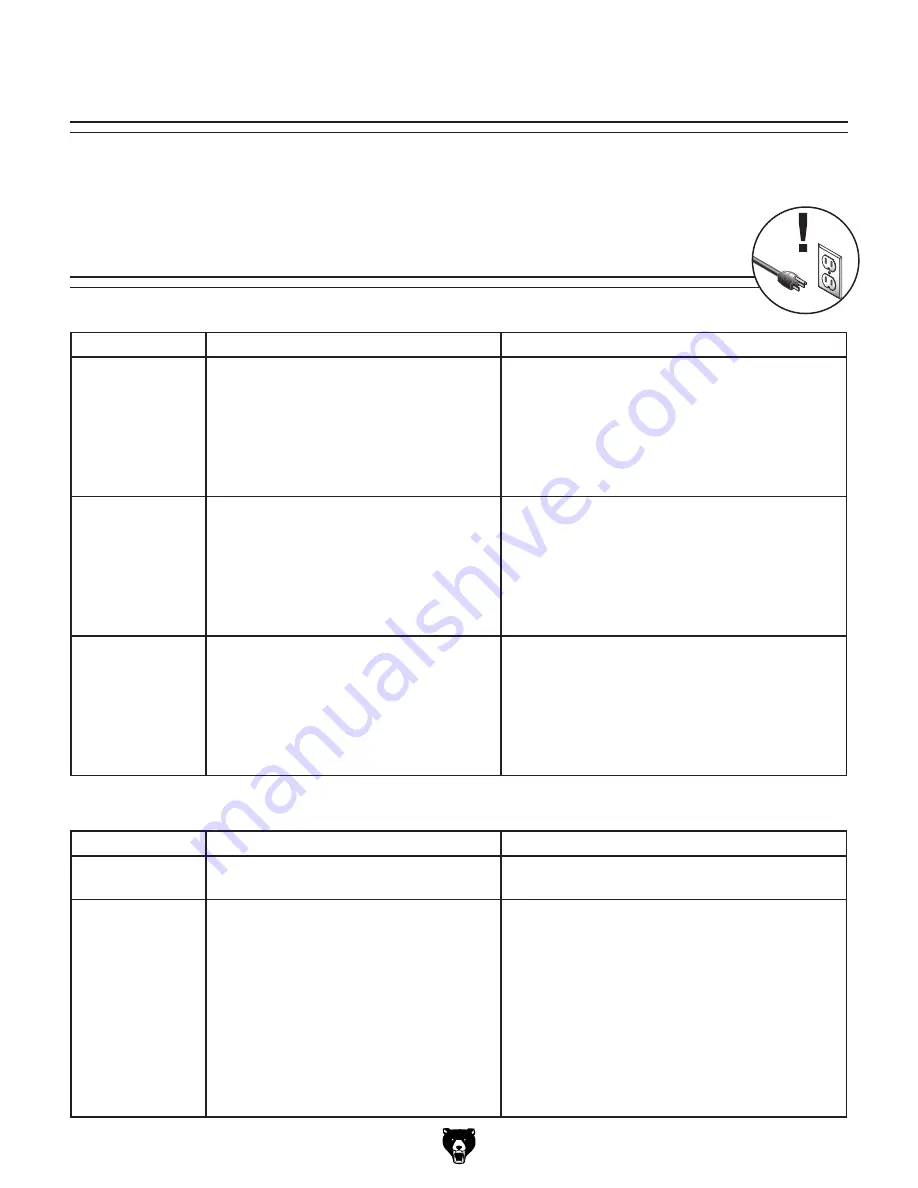
Model T32004 (Mfd. Since 02/20)
-23-
Review the troubleshooting procedures in this section if a problem develops with your machine. If you need
replacement parts or additional help with a procedure, call our Technical Support.
Note: Please gather the
serial number and manufacture date of your machine before calling.
SECTION 7: SERVICE
Troubleshooting
Motor & Electrical
Symptom
Possible Cause
Possible Solution
Machine does not
start, or power-
supply fuse/breaker
trips after startup.
1. Power supply circuit breaker tripped or fuse
blown.
2. Wiring broken, disconnected, or corroded.
3. Motor brushes at fault.
4. ON/OFF switch at fault.
5. Circuit board at fault.
6. Motor at fault.
1. Ensure circuit is sized correctly and free of shorts.
Reset circuit breaker or replace fuse.
2. Fix broken or disconnected wires (
Page 26).
3. Remove/replace brushes (
Page 24).
4. Replace.
5. Replace.
6. Test/repair/replace.
Machine stalls or is
underpowered.
1. Machine undersized for task.
2. Buffing wheel too large/wide.
3. Motor brushes at fault.
4. Motor overheated.
5. Circuit board at fault.
6. Motor or motor bearings at fault.
1. Use new buffing wheel; reduce feed rate.
2. Only use wheels rated for capabilities of machine.
3. Remove/replace brushes (
Page 24).
4. Clean motor, let cool, and reduce workload.
5. Inspect and replace if at fault.
6. Test by rotating shaft; rotational grinding/loose shaft
requires bearing replacement.
Machine has
vibration or noisy
operation.
1. Buffing wheel loose or worn.
2. Tapered spindle sleeves dislodged.
3. Machine incorrectly mounted to workbench.
4. Motor or component loose.
5. Motor shaft bent.
6. Motor or motor bearings at fault.
1. Replace buffing wheel (
Page 20).
2. Reattach spindle sleeves (
Page 14).
3. Adjust feet, shim, or tighten mounting hardware.
4. Replace damaged bolts/nuts or tighten if loose.
5. Test with dial indicator and replace motor.
6. Test by rotating shaft; rotational grinding/loose shaft
requires bearing replacement.
Operation
Symptom
Possible Cause
Possible Solution
M
achine slows when
operating.
1. Operator using too much pressure.
2. RPM too low.
1. Use less pressure when buffing.
2. Increase buffing wheel RPM.
Poor results from
buffing/polishing
operation.
1. Workpiece contains residue or
contaminants.
2. Contaminated buffing compounds on
wheel.
3. Wrong buffing compound for material.
4. Workpiece not held firmly.
5. Incorrect stroke for buffing compound/
wheel/material.
6. Incorrect type of buffing wheel for material.
1. Dirt, oil, rust, paint, or other film must be removed
chemically or with water. Dry parts before buffing.
2. DO NOT mix different compounds on same wheel.
Use separate wheel for each compound. Remove
dried compound with buffing wheel rake (
Page 22).
3. Use correct buffing compound (
Page 19).
4. Use a holding device to firmly retain workpiece.
5. Use upward stroke with heavy pressure for cutting;
use downward stroke with light pressure for
polishing.
6. Use correct buffing wheel for material (
Page 18).
Summary of Contents for T32004
Page 32: ......