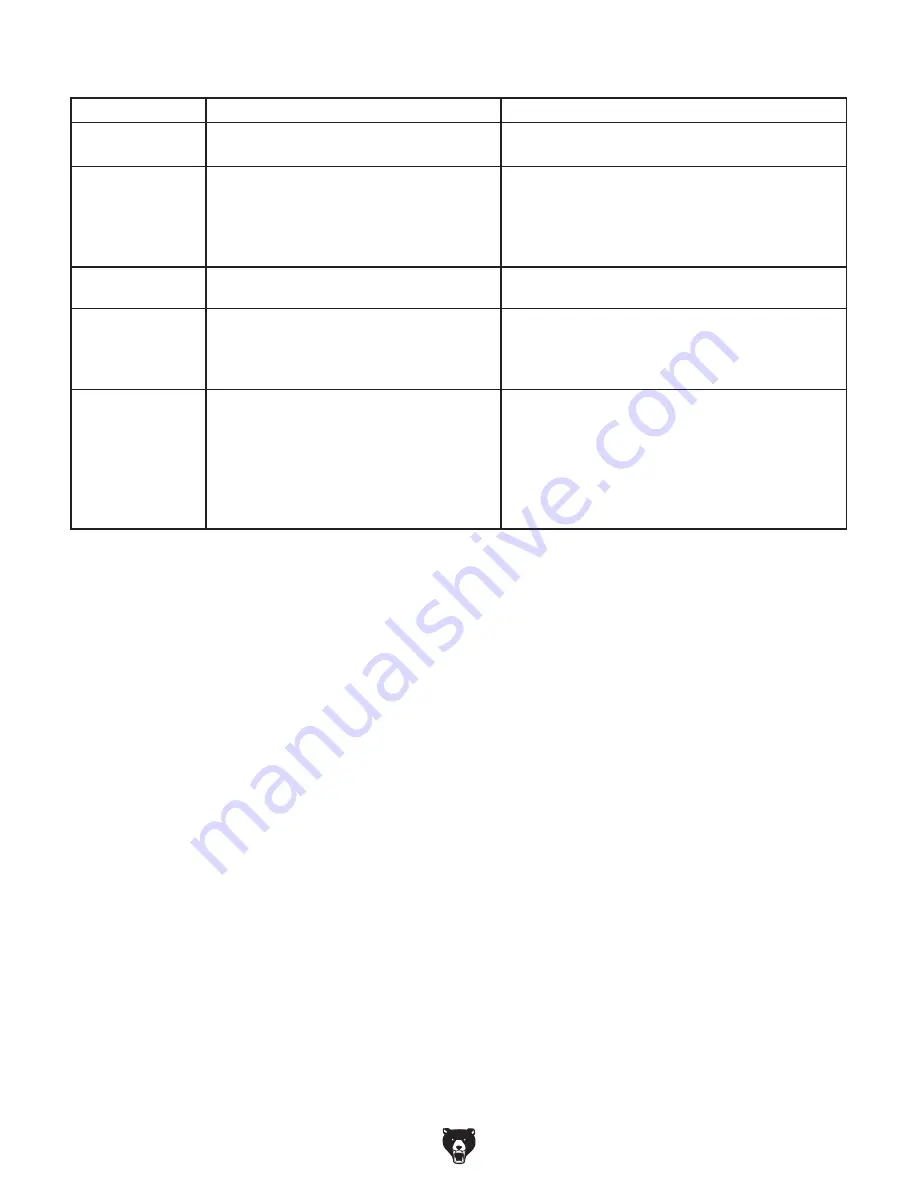
-30-
Model T10875 (Mfd. Since 01/15)
Operation
Symptom
Possible Cause
Possible Solution
M
achine slows when
operating.
1. Operator is using too much pressure.
2. RPM too low.
1. Use less pressure when grinding.
2. Adjust RPM.
Wavy condition
on surface of
workpiece.
1. Machine vibrating.
2. Workpiece not being held firmly.
3. Wheel face uneven.
4. Wheel is too hard.
1. Make sure machine is securely mounted on a solid
surface.
2. Use a holding device to firmly retain workpiece.
3. Dress grinding wheel.
4. Use softer wheel, or reduce feed rate.
Lines on surface of
workpiece.
1. Impurity on wheel surface.
2. Workpiece not being held tightly.
1. Dress grinding wheel.
2. Use a holding device to firmly retain workpiece.
Burning spots
or cracks in the
workpiece.
1. Improper type of grinding wheel.
2. Improper feed rate.
3. Workpiece requires quenching.
1. Try a wheel which is softer style or coarser grit.
2. Slow down rate of movement of workpiece into
wheel.
3. Quench workpiece in water to cool.
Wheel dulls quickly,
grit falls off.
1
. Depth of cut too great.
2. Wheel is too soft.
3. Wheel diameter too small.
4. Bad wheel dress.
5. Defective wheel bonding.
1
. Slow down rate of movement of workpiece into
wheel.
2. Wheel too soft for material being ground; select
harder bond.
3. Replace wheel.
4. Dress wheel.
5. Consult manufacturer of grinding wheel.
Summary of Contents for T10875
Page 40: ......