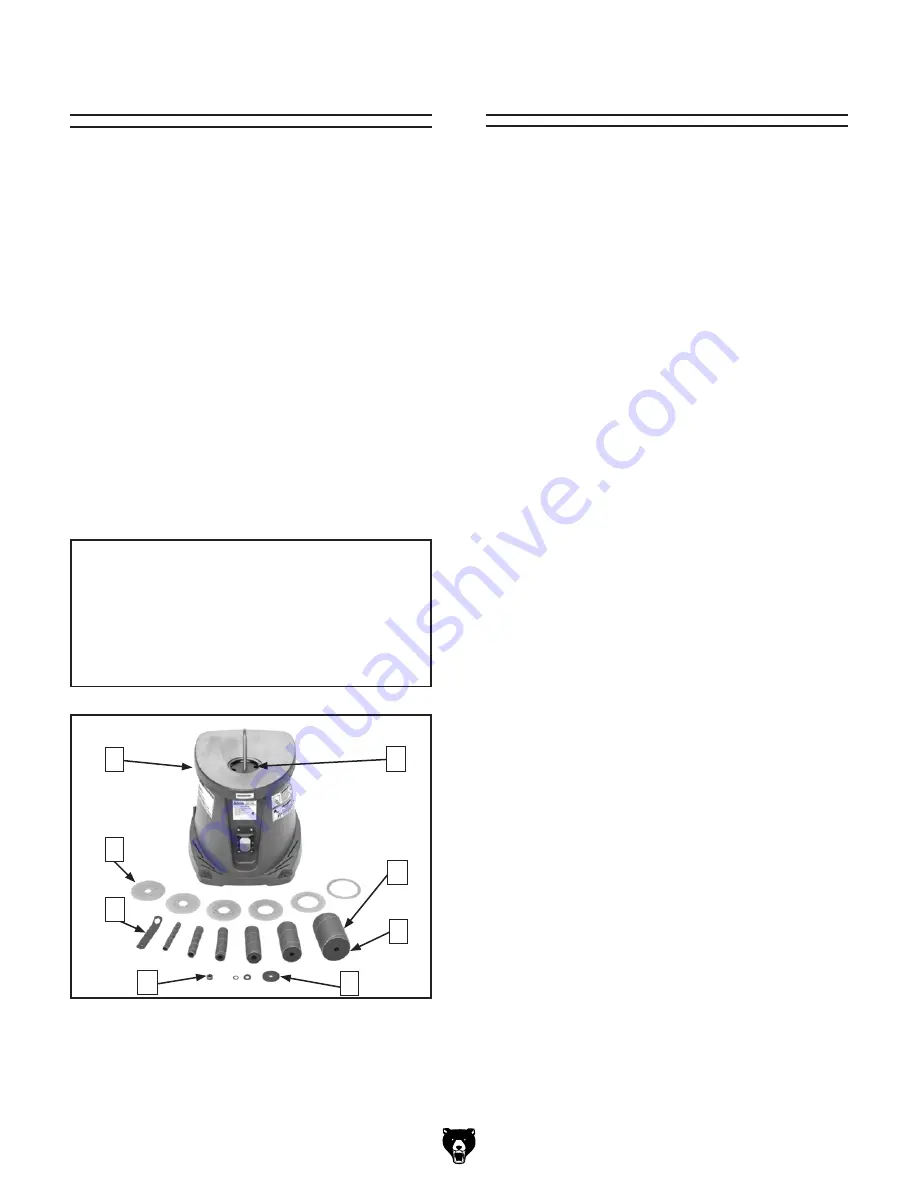
Model g0739 (Mfg. since 2/12)
-11-
Inventory
The following is a description of the main compo-
nents shipped with your machine. Lay the compo-
nents out to inventory them.
If any non-proprietary parts are missing (e.g. a
nut or a washer), we will gladly replace them; or
for the sake of expediency, replacements can be
obtained at your local hardware store.
Inventory: (figure 3)
Qty
A.
spindle sander Assembly................................1
b.
table inserts
1
⁄
2
",
3
⁄
4
",
1", 1
1
⁄
2
", 2", 3"...............6
C.
Arbor Wrench .....................................................1
D.
spindle hex nut ................................................1
E.
spindle Washers
5
⁄
8
",
7
⁄
8
", 1
3
⁄
4
"......... ...............3
f.
sanding drums
3
⁄
4
", 1", 1
1
⁄
2
", 2", 3".................5
G.
sanding sleeves
1
⁄
2
",
3
⁄
4
", 1", 1
1
⁄
2
", 2", 3"........6
h.
Base Washer 2
3
⁄
4
" .............................................1
The unpainted surfaces of your machine are
coated with a heavy-duty rust preventative that
prevents corrosion during shipment and storage.
This rust preventative works extremely well, but it
will take a little time to clean.
Be patient and do a thorough job cleaning your
machine. The time you spend doing this now will
give you a better appreciation for the proper care
of your machine's unpainted surfaces.
There are many ways to remove this rust preven-
tative, but the following steps work well in a wide
variety of situations. Always follow the manufac-
turer’s instructions with any cleaning product you
use and make sure you work in a well-ventilated
area to minimize exposure to toxic fumes.
Before cleaning, gather the following:
•
Disposable Rags
•
Cleaner/degreaser (WD•40 works well)
•
Safety glasses & disposable gloves
•
Plastic paint scraper (optional)
Basic steps for removing rust preventative:
1.
Put on safety glasses.
2.
Coat the rust preventative with a liberal
amount of cleaner/degreaser, then let it soak
for 5–10 minutes.
3.
Wipe off the surfaces. If your cleaner/degreas-
er is effective, the rust preventative will wipe
off easily. If you have a plastic paint scraper,
scrape off as much as you can first, then wipe
off the rest with the rag.
4.
Repeat
Steps 2–3
as necessary until clean,
then coat all unpainted surfaces with a quality
metal protectant to prevent rust.
Gasoline or products
with low flash points can
explode or cause fire if
used to clean machin-
ery. Avoid cleaning with
these products.
Many cleaning solvents
are toxic if concentrat-
ed amounts are inhaled.
Only work in a well-venti-
lated area.
NOTICE
Avoid chlorine-based solvents, such as
acetone or brake parts cleaner, that may
damage painted surfaces. Test all cleaners
in an inconspicuous area before using to
make sure they will not damage paint.
Cleanup
NOTICE
If you cannot find an item on this list, care-
fully check the machine and the packaging
materials. Some of these items may be pre-
installed for shipping or become misplaced
during unpacking.
figure 3.
Box Contents
C
A
B
d
E
F
g
h