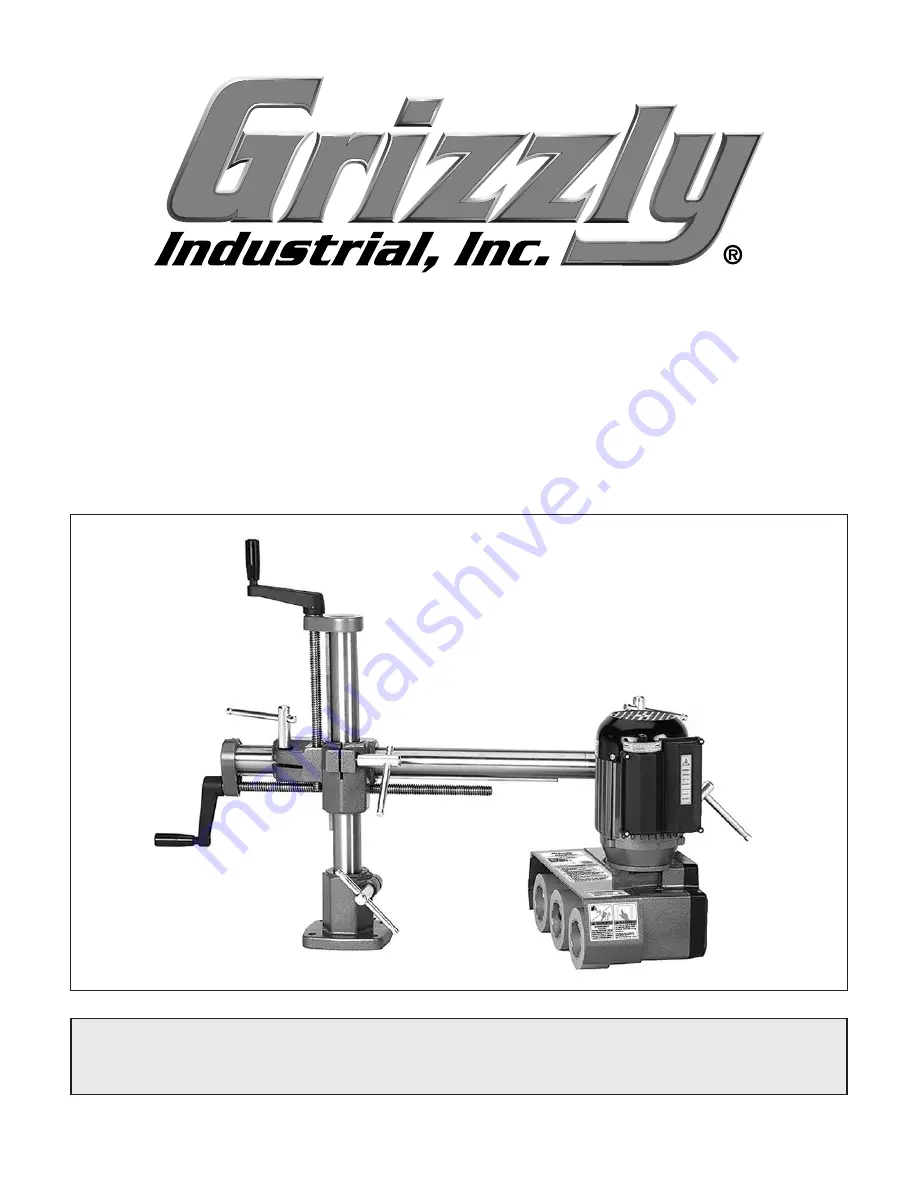
COPYRIGHT © JUNE, 2008 BY GRIZZLY INDUSTRIAL, INC., REVISED MAY, 2022 (SS)
WARNING: NO PORTION OF THIS MANUAL MAY BE REPRODUCED IN ANY SHAPE
OR FORM WITHOUT THE WRITTEN APPROVAL OF GRIZZLY INDUSTRIAL, INC.
#CR10816 PRINTED IN TAIWAN
MODEL G4179
1/2 HP POWER FEEDER
OWNER'S MANUAL
(For models manufactured since 01/22)
***Keep for Future Reference***
V3.05.22
Summary of Contents for G4179
Page 40: ......