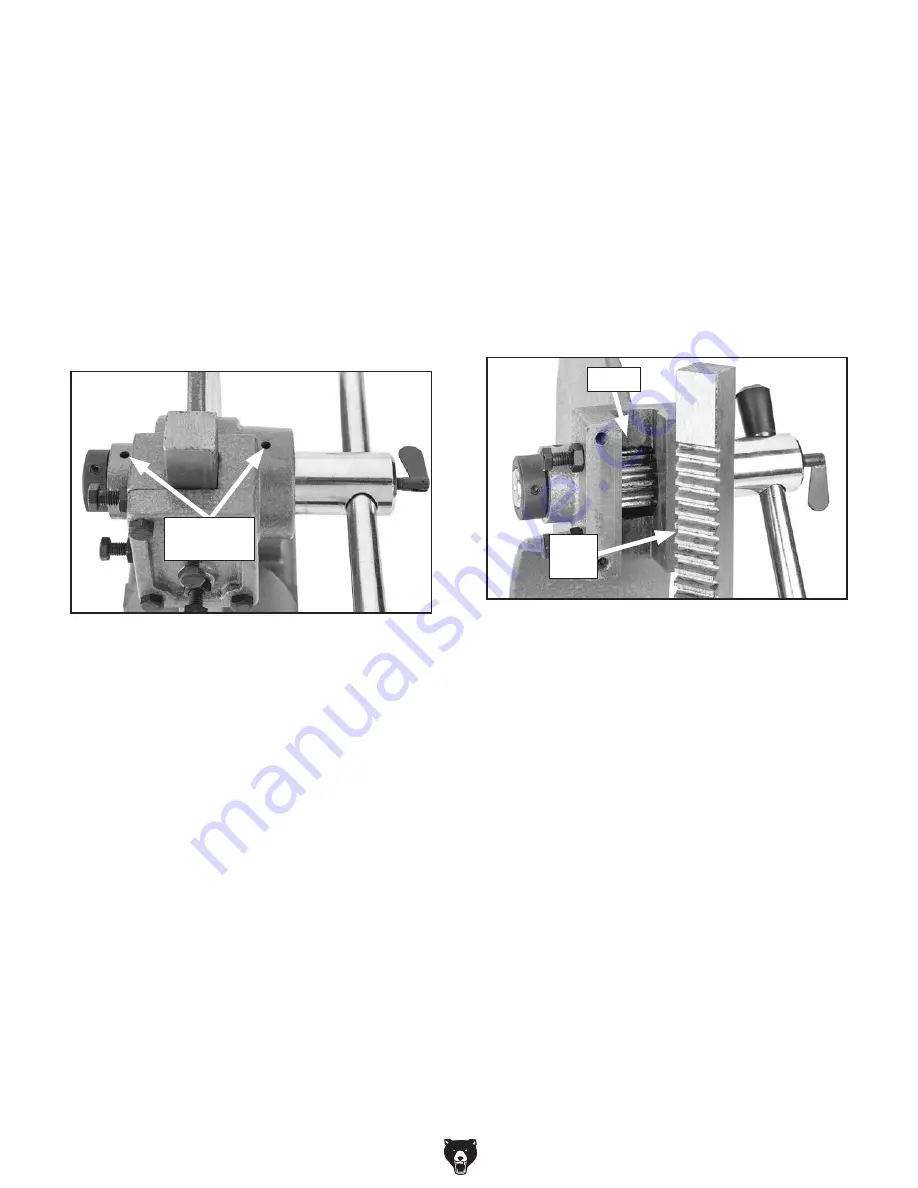
G4017–20 (Mfd. 02/15+)
-5-
Wipe the arbor press down with a clean shop rag
and mineral spirits. When dry, protect the unpaint-
ed surfaces by applying a thin film of ISO 32 oil.
Grease ..................T23964 or NLGI#2 Equivalent
Grease Amount ................................. As Needed
Lubrication Frequency .........40 Hrs. of Operation
Tools Needed
Qty
Wrench or Socket 12mm (G4017, G4018) ......... 1
Wrench or Socket 14mm (G4019, G4020) ........ 1
To grease rack and pinion:
1. Remove front plate, then remove ram to
expose pinion and rack (see
Figure 11).
2. Use shop rags, a stiff brush, and mineral spir-
its to clean teeth of rack and pinion.
3. When dry, apply a light coat of grease to rack
and pinion teeth.
4. Re-install ram and front plate.
5. Use sliding handle to move ram up and down
several times to distribute grease.
Figure 11. Ram rack and pinion exposed after
removing front plate.
Pinion
Ram
Rack
Cleaning & Protecting
Oiling Pinion Hub Shaft
Push the tip of the oil can nozzle against the oil
access hole and pump oil can once or twice. If
you see sludge and contaminants coming out
of the lubrication area, continue pumping the oil
can until the oil runs clear. Move the components
through the entire path of travel a few times to
distribute the oil. When finished, wipe away the
excess oil.
Figure 10. Locations of oil access holes to
lubricate pinion hub shaft.
Oil Access
Holes
Oil Type .................T26685 or ISO 32 Equivalent
Oil Amount ......................................... 1–2 Pumps
Lubrication Frequency ...........8 Hrs. of Operation
Proper lubrication of the pinion hub shaft is done
with a pump-type oil can with a cone tip through
the oil access holes (see
Figure 10).
Greasing Rack and Pinion