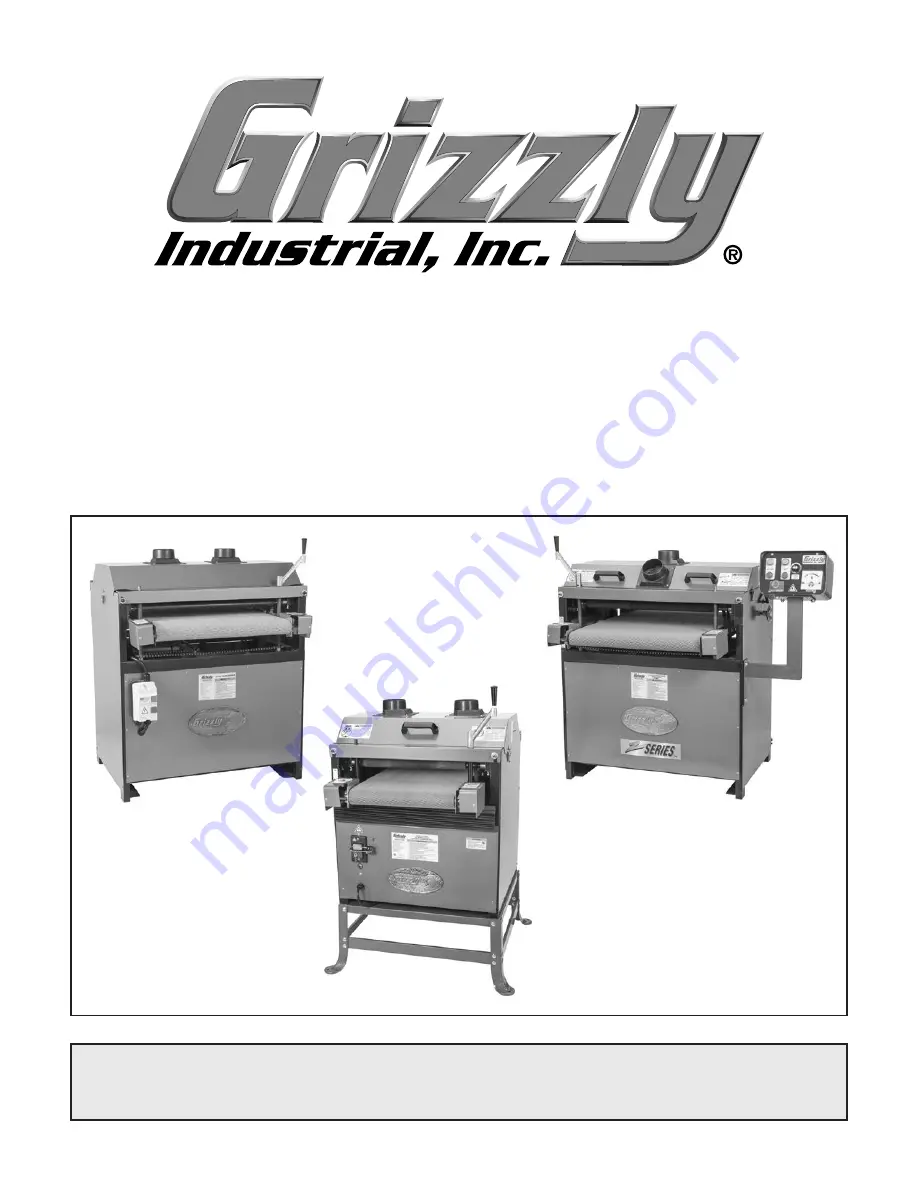
COPYRIGHT © MAY, 2002 BY GRIZZLY INDUSTRIAL, INC. REVISED OCTOBER, 2018 (ES)
WARNING: NO PORTION OF THIS MANUAL MAY BE REPRODUCED IN ANY SHAPE
OR FORM WITHOUT THE WRITTEN APPROVAL OF GRIZZLY INDUSTRIAL, INC.
#0443 PRINTED IN TAIWAN
V2.10.18
MODEL G1066R/G1066Z/G1079R
DRUM SANDER
OWNER'S MANUAL
(For models manufactured since 02/11)
Model G1066R
Model G1066Z
Model G1079R