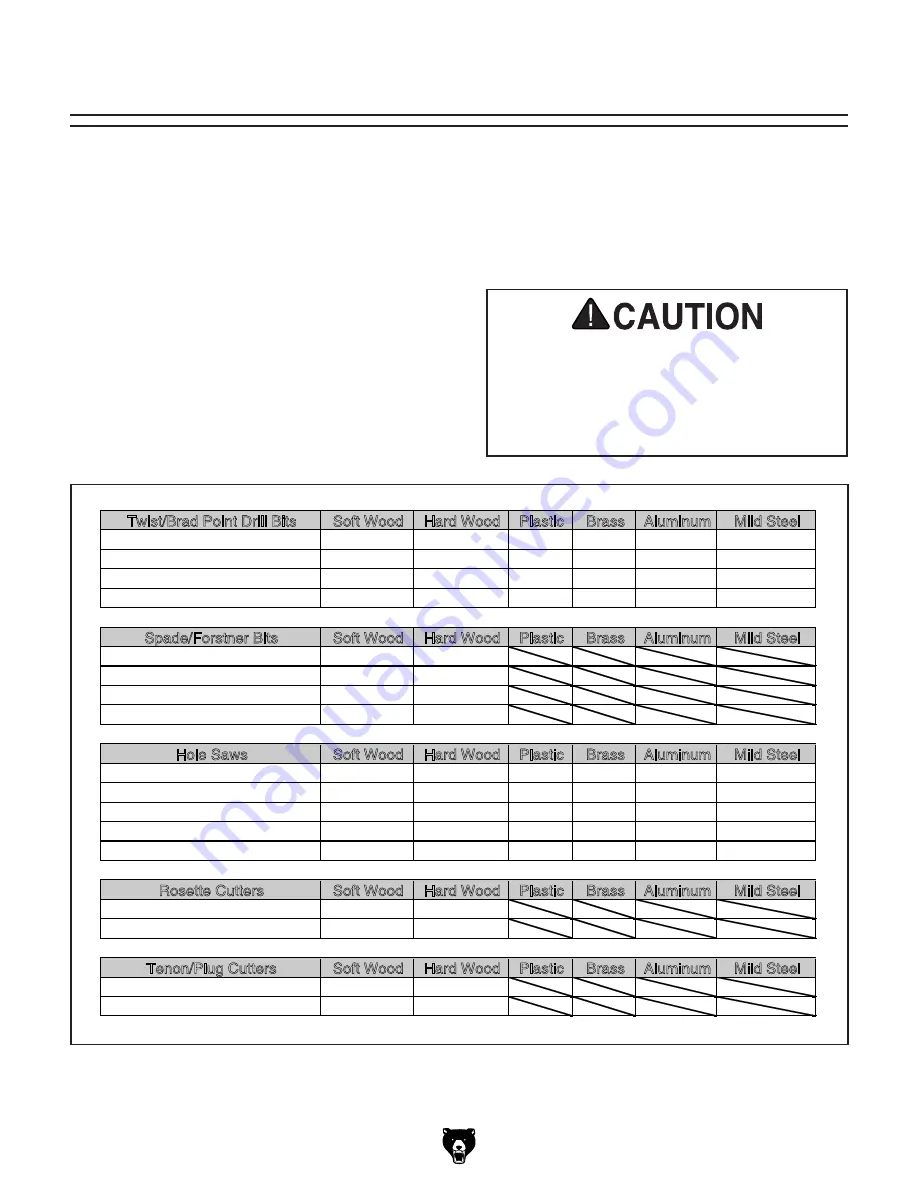
Model G0925 (Mfd. Since 02/20)
-19-
Choosing Spindle Speeds
Twist/Brad Point Drill Bits
Soft Wood
Hard Wood
Plastic
Brass
Aluminum
Mild Steel
1/16" – 3/16"
3000
2500
2500
2500
3000
2500
13/64" – 3/8"
2000
1500
2000
1250
2500
1250
25/64" – 5/8"
1500
750
1500
750
1500
600
11/16" – 1"
750
500
1000
400
1000
350
Spade/Forstner Bits
Soft Wood
Hard Wood
Plastic
Brass
Aluminum
Mild Steel
1/4" – 1/2"
2000
1500
9/16" – 1"
1500
1250
1-1/8" – 1-7/8"
1000
750
2–3"
500
350
Hole Saws
Soft Wood
Hard Wood
Plastic
Brass
Aluminum
Mild Steel
1/2" – 7/8"
500
500
600
600
600
500
1" – 1-7/8"
400
400
500
500
500
400
2" – 2-7/8"
300
300
400
400
400
300
3" – 3-7/8"
200
200
300
300
300
200
4" – 5"
100
100
200
200
200
100
Rosette Cutters
Soft Wood
Hard Wood
Plastic
Brass
Aluminum
Mild Steel
Carbide Insert Type
350
250
One-Piece Type
1800
500
Tenon/Plug Cutters
Soft Wood
Hard Wood
Plastic
Brass
Aluminum
Mild Steel
3/8" – 1/2"
1200
1000
5/8" – 1"
800
600
Using Drill Bit Speed Chart
The chart shown in
Figure 16 is intended as a
generic guide only. Always follow the manufac-
turer's speed recommendations if provided with
your drill bits, cutters, or hole saws. Exceeding
the recommended speeds may be dangerous to
the operator.
The speeds shown here are intended to get you
started. The optimum speed will always depend
on various factors, including tool diameter, drilling
pressure, material hardness, material quality, and
desired finish.
Often, when drilling materials other than wood,
some type of lubrication is necessary.
Lubrication Suggestions
Wood ...........................................................None
Plastics ............................................Soapy Water
Brass ...............................Water-Based Lubricant
Aluminum ..................... Paraffin-Based Lubricant
Mild Steel ............................. Oil-Based Lubricant
Figure 16. Drill bit speed chart (RPMs).
Larger bits turning at slower speeds tend
to grab workpiece aggressively. This can
result in operator's hand being pulled into
bit or workpiece being thrown with great
force. Always clamp workpiece to table to
prevent reduce risk of injury.
Summary of Contents for G0925
Page 44: ......