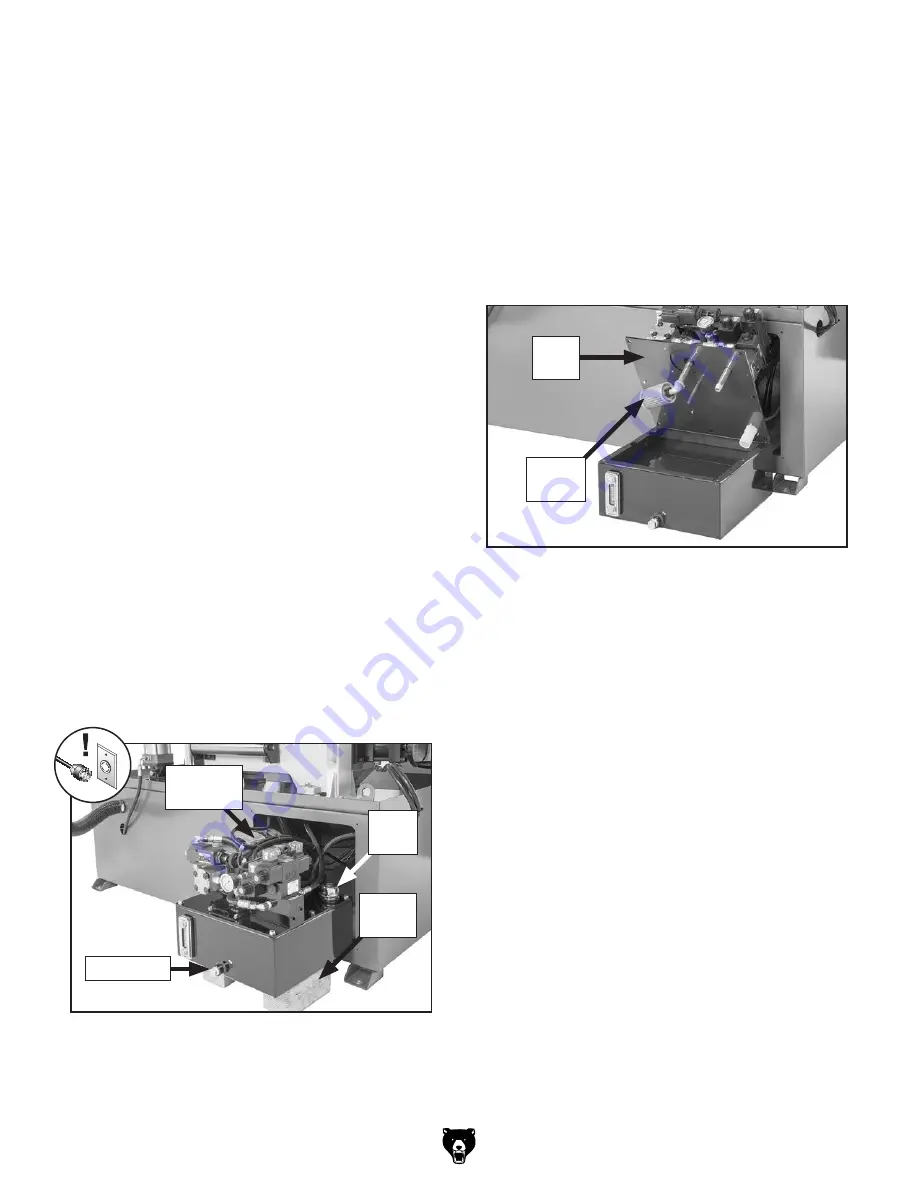
Model G0886 (Mfd. Since 01/19)
-47-
6. Clean tank cap and fill screen (see Figure 69)
on
Page 46) with mineral spirits and allow to
air dry.
7. Open tank by removing (8) hex bolts that
secure lid (see
Figure 71).
8. Clean tank and tank screen (see Figure 71)
with mineral spirits. Wipe out as much resid-
ual fluid and contaminants from tank as pos-
sible. Allow tank and tank screen to air dry.
9. Re-install tank lid and screen.
10. Re-wrap drain plug threads with Teflon tape,
re-install drain plug, then fill tank with 16
quarts of ISO 32 or equivalent hydraulic fluid.
11. Re-install tank cap, slide hydraulic unit back
into base, and re-install front access panel.
Changing Hydraulic Fluid
To change hydraulic fluid:
1. Raise/lower headstock repeatedly for approx-
imately 10 minutes to warm up hydraulic fluid.
2. DISCONNECT MACHINE FROM POWER!
3. Remove hydraulic unit access panel on rear
of machine
.
4. Slide hydraulic unit out of machine base and
support weight of hydraulic unit with wood
blocks (see
Figure 70).
5. Remove tank cap (see Figure 70), then
remove drain plug and allow tank to empty
into drain pan.
Item(s) Needed
Qty
T23963 or ISO 32 Equivalent .................... 16 Qt.
Safety Goggles .................................................. 1
Hex Wrench 4mm .............................................. 1
Wood Blocks ..................................... As Needed
5-Gallon Drain Pan ............................................ 1
Open-End or Socket Wrench 21mm.................. 1
Funnel ................................................................ 1
Clean Shop Rags .............................. As Needed
Mineral Spirits .................................... As Needed
Teflon Thread Tape ........................... As Needed
The hydraulic fluid should be changed and the
fluid tank cleaned every 5,000 hours of use.
Figure 70. Hydraulic unit removed from base.
Wood
Blocks
Tank
Cap
Hydraulic
Unit
Drain Plug
Figure 71.
Hydraulic fluid tank lid removed.
Tank
Screen
Tank
Lid
Changing Hydraulic Fluid